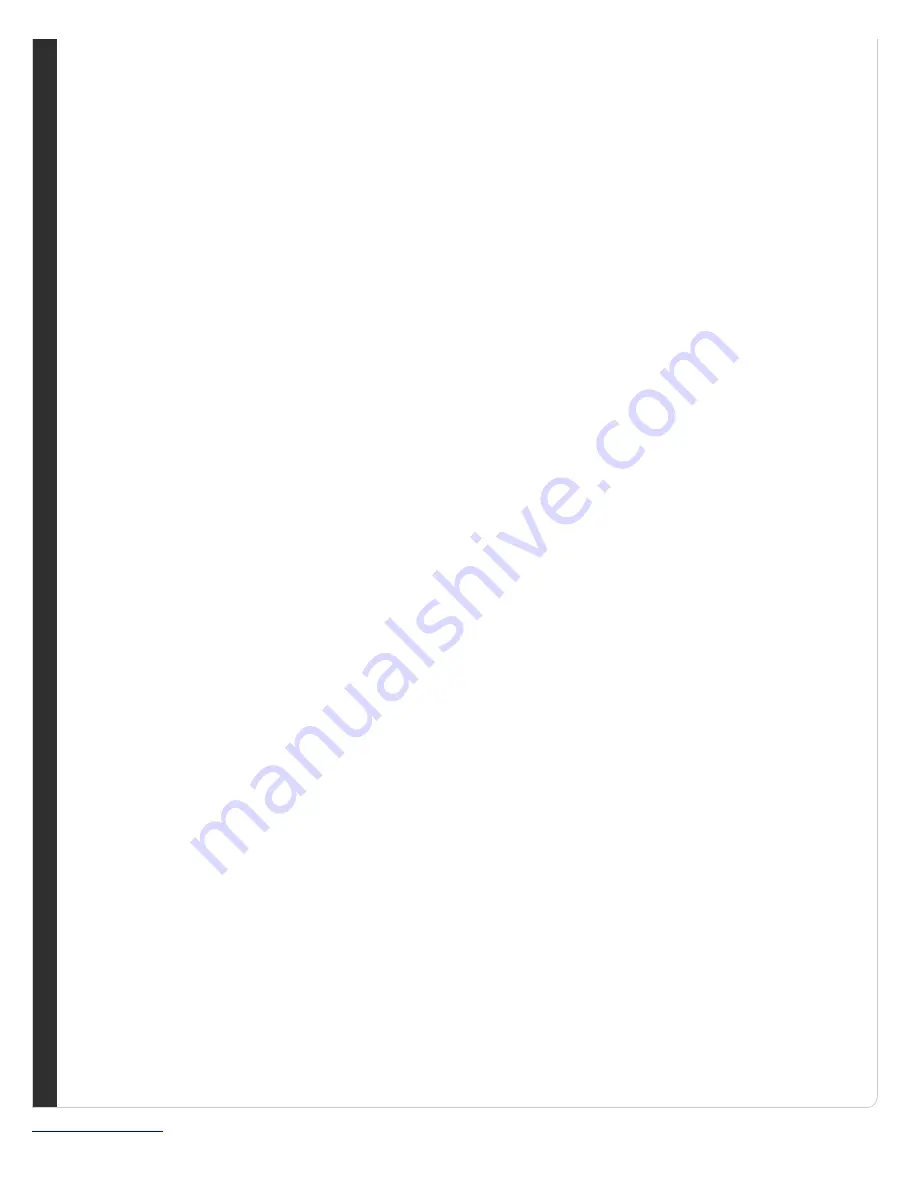
Hide The Elliptec™ Motor
appropriate ASCII message as is specified in the communications protocol manual.
The default Home position is referenced to a fixed feature on the stage assembly. If desired, the user may redefine the position of Home to be offset from the
default position by up to +90° (a quarter turn in the clockwise direction). Being able to customize the Home position can be useful when synchronizing the
orientations of two or more stages. When executing the Home command, the stage first finds the approximate location of Home, and then a fine-positioning
procedure is used to orient the stage at Home with an accuracy of 288.0 µrad. The user can specify whether the stage rotates in a clockwise or
counterclockwise direction (as defined from the perspective of looking down on the surface of the stage) during the first phase of the homing procedure, but
the fine-positioning phase is always performed in the counterclockwise direction for repeatability.
The default Home position is found by using first an optical IR sensor and then a relative (incremental) magnetic sensor. The optical sensor is located under
the stage, and its 980 nm emission is confined by the underside of the stage and the top surface of the PCB. The magnetic sensor's encoder is connected to a
shaft that revolves 64 times for each rotation of the stage. The encoder generates one command pulse for each revolution of the shaft, which results in 64
command pulses being generated for each rotation of the stage, effectively defining 64 sectors within a full rotation. Each sector consists of 4096 individual
increments. Using the output of the magnetic sensor alone, it is not possible to uniquely identify any of the 64 sectors defined by the encoder. Accurate
positioning of the stage requires referencing the readings from the magnetic sensor to a known location, and the IR sensor signal is used to establish the
required reference point. At the start of the procedure to find the default Home position, the stage is rotated and the signal from the IR sensor is monitored.
The IR sensor's detection of the fixed feature on the stage assembly triggers the rotation stage assembly to start monitoring the signal from the magnetic
sensor. The stage continues to rotate until it detects the first subsequent command pulse generated by the magnetic sensor's encoder. The location
corresponding to this command pulse is defined as the default Home position. If the user specifies the position of Home to be offset from the default Home
position, the offset is applied in the clockwise direction. After the Home position is found, readings from the magnetic sensor, which can resolve angular
increments of 24.0 µrad, are used to position the stage and when executing the Home command.
Positioning the Rotation Stage
Note that the rotation stage is not intended for continuous operation. We recommend operation with duty cycles of less than 40% during general use, while
operation with duty cycles greater than 60% should be limited to a few seconds.
Before the stage may be positioned, the Home position of the stage must be found. Please see the previous section for details. The movement of the stage
may be controlled by pressing buttons on the interface board, through computer control via the Elliptec™ software package that may be downloaded, or by
sending simple signals to digital lines on the stage's board. The buttons on the interface board can be seen in the image of the interface board above. A link
to download the software and accompanying documentation can be found in the
Software
tab. The interface board may be used as an accessory while
interfacing with the stage through the Elliptec software; all changes in the position of the rotation stage that occur as a result of pressing buttons on the
interface board are registered by the software, and the software may independently control the rotation stage while the interface board is connected. It is also
possible to effect the simultaneous movement of several rotation stages by connecting all to the communications bus. When this is done, the software can
send separate commands to each stage, while commands originating from buttons pressed on the handset will be sent to all connected stages. The
communications protocol manual describes how to use the software to individually address each connected stage.
The interface board can be used to move the stage forward and backward in increments by pressing and holding the JOG button while pressing and releasing
the FW or BW button, respectively. The default increment is 45°, and a custom increment can be set using the Elliptec software or by sending the appropriate
ASCII message(s) as specified in the communications protocol manual. The Elliptec software can be used to move the stage to absolute and relative positions,
in addition to jogging the stage forward or backward. The software is also used to set the jog step size, read the position of the stage, and adjust the position
of Home, as is described in the previous section.
Readings from the magnetic sensor, which can resolve angular increments of 24.0 µrad, are used to position the stage and when executing the Home
command. The travel range of the stage is not limited, but the reported orientation of the stage is always expressed as a value between 0° and 359.99°. The
minimum incremental movement of the stage is 288.0 µrad, and it can be positioned with a repeatability of 434 µrad in response to signals from the magnetic
sensor.
The stage learns to efficiently position itself precisely using a position error compensation algorithm. After the stage moves into a new position, it detects the
error between the requested and actual positions. The position of the stage is then corrected, and an error compensation value is calculated. The algorithm is
then updated with the error compensation value, so that it is applied when the stage is move to its next position. Typically, an optimum error compensation
value is found after between two and six movements.
Resonance Frequencies
On power-up, the factory default setting instructs each motor driving the rotation stage to search for the resonance frequencies that will deliver the best
performance. During this process, the rotation stage will translate a forward and backward by a small amount. If movement on start-up is undesirable, it is
possible to disable this calibration procedure by using the serial port to initialize the frequencies on power-up. A new search for optimal resonance frequencies
may be performed at any time; to maintain optimal performance, it is recommended that new searches be performed after changes in loading and/or ambient
temperature. Please see Section 3.3 of the manual for details.