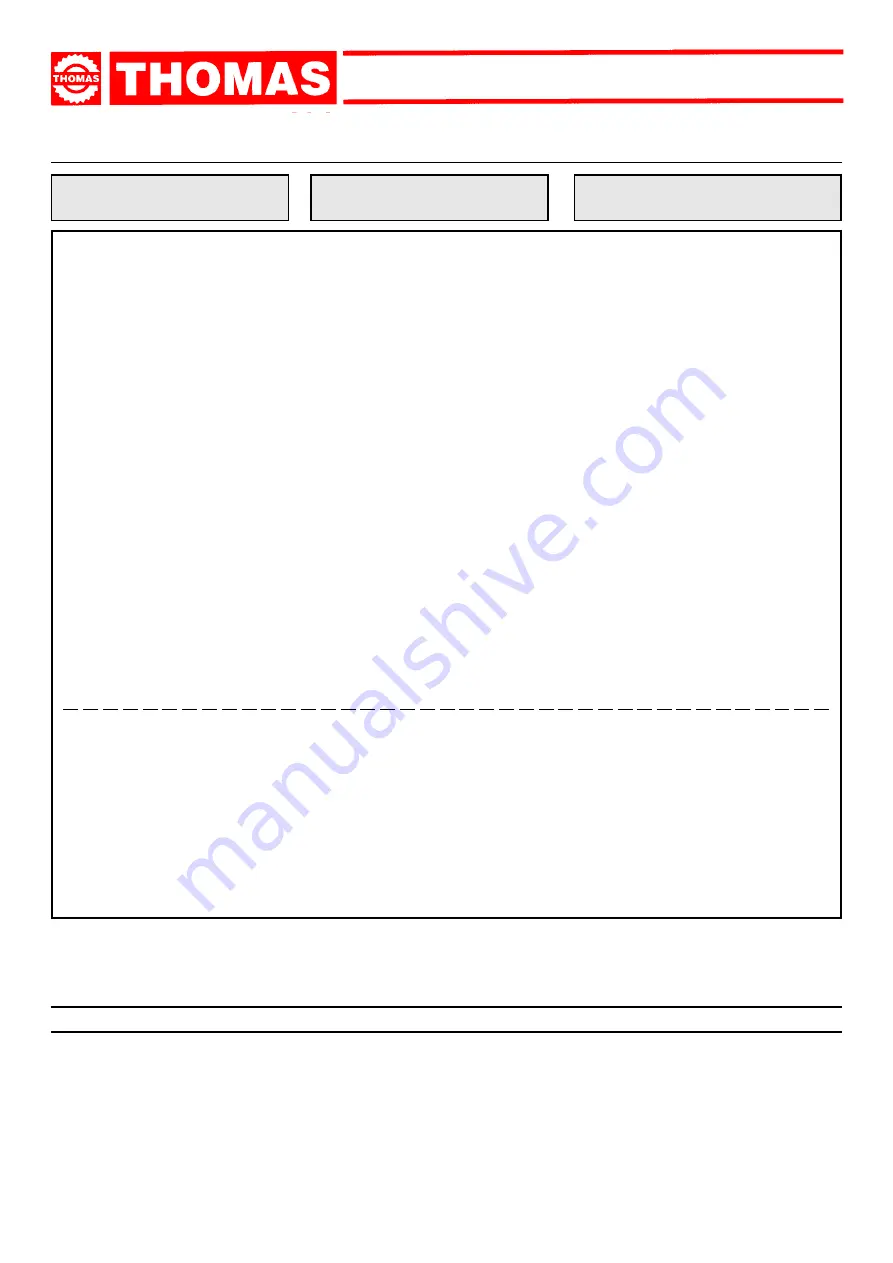
21
SUPER CUT
SUPER CUT
SUPER CUT
SUPER CUT
SUPER CUT
NOISE TESTS
In accordance with point 1.7.4.f of the Machines Directive EEC 89/392
SOUND LEVEL CALIBRATOR MOD. BRUEL & KIAER 2260
2 measurements with the machine.
- The microphone was been located close to the operator's head, at medium height.
- The weighted equivalent continuous acoustic pressure level was 71,6 dB (A).
- The maximum level of the WEIGHTED instantaneous acoustic pressure C was always less than 130 dB.
NOTE: with the machine operating, the noise level will vary according to the different materials being processed. The user must
there-fore assess the intensity and if necessary provide the operators with the necessary personal protection, as required by Law
277/1991.
12.2 - Electrical components diagnosis
FAULT
PROBABLE CAUSE
REMEDY
13
THE GREEN PILOT LIGHT
“HL” DOES NOT LIGHT UP
Fused lamp
Power supply
Fuses “FU 1”
Short circuits
Speed switch “SA” in position “0”
Emergency button “SB 1” on
Cycle reset or line button “SB 2”
Thermal probe built into the stator
winding has tripped due to motor
overheating
Transformer “TC 1”
Fuse “FU 2”
Auxiliary relay “KA”
Change it.
Check: - phases
- cables
- socket
- plug
Voltage must arrive upstream from the
fuses.
Check for efficiency.
Identify and eliminate.
It must be turned to position 1 or 2.
Ensure that it is off and that its contacts
are unbroken.
Check mechanical efficiency.
Check current continuity on the two wires
in the prone after letting the motor cool
for about 10-15 minutes. If after this time
there is no current continuity in the two
wires, the motor must be changed or
rewound.
Check that the supply voltage is the same
as the line voltage and that it gives a value
of 24 V at output.
Check fuse efficiency and ensure there
are no short circuits causing the protection
to trip.
Check that 24 V reach the coil terminals
when the button “SB 2” is pressed; if this
happens and the relay is not self-fed, it
must be changed.
MOTOR STOPPED WITH PILOT
LIGHT “HL” LIT
Socket and plug connecting the
electric box/ microswitch in the handle
Microswitch “SQ 1” in the handle
Remote-control switch “KM”
Motor “M 1”
Check that the plug is correctly inserted
and look for any bad connections inside
the box.
Check operation and/or efficiency; replace
if broken.
Check that phases are present at both
input and output; ensure that it is not
blocked, that it closes when fed, that it
does not cause short circuits; otherwise
change it.
Check that it is not burnt and that it turns
freely.
It may be rewound or changed.