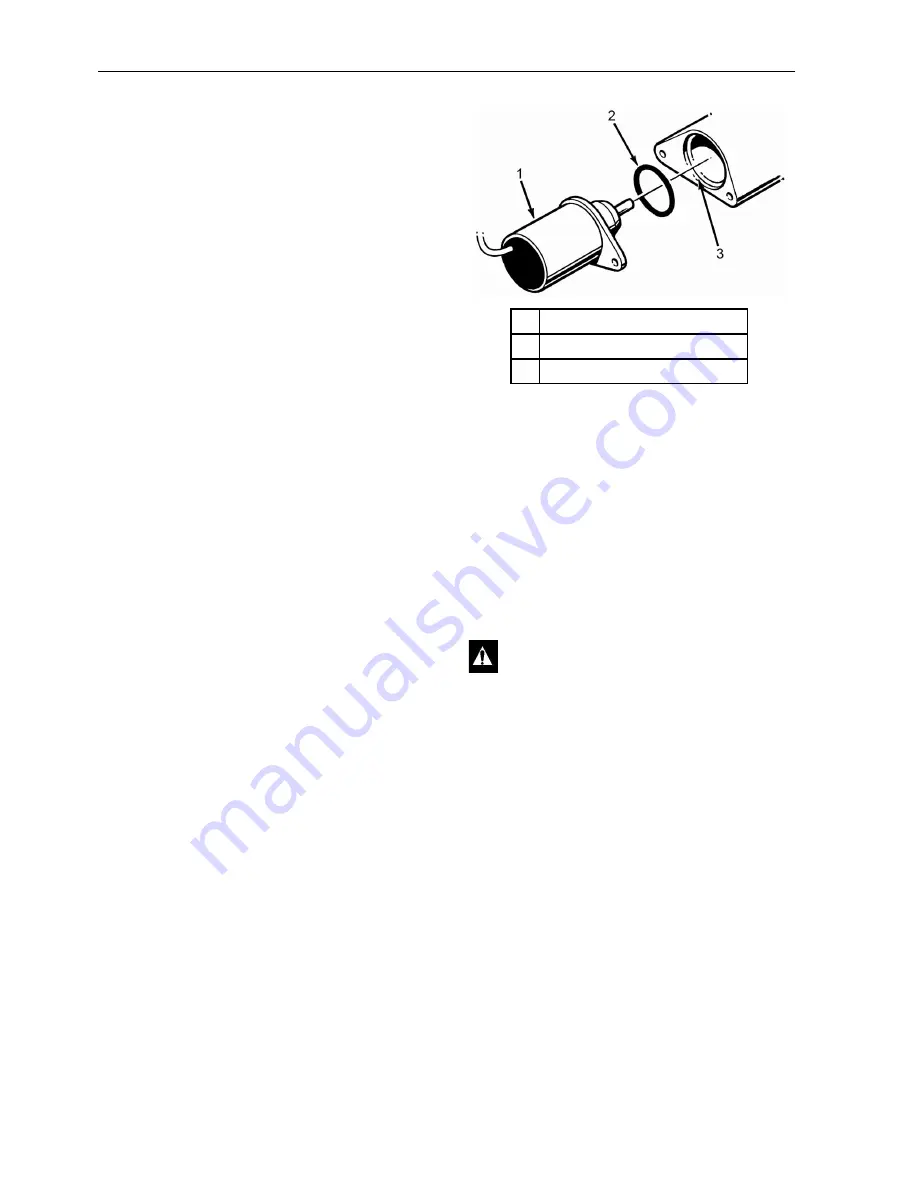
Engine Maintenance
90
b. Momentarily energize the pull-in coil by
placing a jumper between the white wire
(8DP—pin B) in the fuel solenoid
connector and the positive battery
terminal. The fuel solenoid should make a
definite click when the pull-in coil is
energized, but should not click when the
pull-in coil is de-energized.
c. De-energize the hold-in coil by removing
the jumper from the red wire (8D—pin A)
and the 2 terminal. The fuel solenoid
should make a definite click when the
hold-in coil is de-energized.
d. If the hold-in coil does not function
properly, check the resistance of the
hold-in coil by placing an ohmmeter
between the red wire (8D—pin A) and the
black wire (CH—pin C) in the fuel
solenoid connector. The resistance of the
hold-in coil should be 24 to 29 ohms. If
the resistance of the hold-in coil is not in
this range, replace the fuel solenoid.
Fuel Solenoid Replacement
1. Disconnect the fuel solenoid wire connector
from the main wire harness and remove the
old fuel solenoid.
2. Connect the new fuel solenoid wire connector
to the main wire harness.
3. Press the
O
N
key to turn the unit on.
4. Use the microprocessor keypad to enter the
Interface Board Test Mode. Refer to the
appropriate Microprocessor Diagnostic
Manual for specific information about the
Relay Test Mode.
5. Energize the fuel solenoid by energizing the
run relay with the Interface Board Test Mode.
NOTE: The fuel solenoid must be energized
when it is installed. If not, the plunger and
the linkage may not line up correctly and the
fuel solenoid will not function properly.
6. Place the O-ring in the groove in the end of
the fuel injection pump. Make sure that the
O-ring is positioned correctly during
installation to avoid damage and leaks.
7. Install the new fuel solenoid.
8. Press the
O
FF
key to turn the unit off after
installing the fuel solenoid.
Engine Valve Clearance Adjustment
1. Remove the rocker arm cover.
2. Remove the round cover (plug) from the
timing mark access hole on the front of the
bell housing.
3. Place the engine at top dead center of the
compression stroke for the number one
cylinder. Refer to steps a. through d.
a. Rotate the engine in the normal direction
of rotation (clockwise viewed from the
water pump end) until the 1-4 timing mark
on the flywheel lines up with the index
mark in the timing mark access hole.
1.
Fuel Solenoid
2.
O-ring
3.
Groove in Fuel Injection Pump
Figure 79: Fuel Solenoid Components
CAUTION: Loosen all of the injection
lines at the injection nozzles to prevent the
possibility of the engine firing while it is
being rotated.
AEA635
Содержание SB-210
Страница 4: ...4 ...
Страница 12: ...List of Figures 12 ...
Страница 31: ...Unit Description 31 Unit Photos Figure 6 Front View AJA1617 ...
Страница 32: ...Unit Description 32 1 Defrost Damper 2 X430L Compressor 3 TK 486 Engine Figure 7 Back View 2 3 1 AJA1930 ...
Страница 36: ...Unit Description 36 ...
Страница 49: ...Operating Instructions 49 Figure 32 Viewing Sensors Screen Sequence ...
Страница 54: ...Operating Instructions 54 Figure 40 Datalogger Screen Sequence ...
Страница 101: ...Engine Maintenance 101 ...
Страница 102: ...Engine Maintenance 102 ...
Страница 140: ...Electric Standby Diagnosis 140 ...
Страница 150: ...Index 150 ...
Страница 152: ...Wiring Diagram Index 152 ...
Страница 153: ...153 Model 30 and 50 Schematic Diagram Page 1 of 3 ...
Страница 154: ...154 Model 30 and 50 Schematic Diagram Page 2 of 3 ...
Страница 155: ...155 Model 30 and 50 Schematic Diagram Page 3of 3 ...
Страница 156: ...156 Model 30 and 50 Wiring Diagram Page 1 of 4 ...
Страница 157: ...157 Model 30 and 50 Wiring Diagram Page 2 of 4 ...
Страница 158: ...158 Model 30 and 50 Wiring Diagram Page 3 of 4 ...
Страница 159: ...159 Model 30 and 50 Wiring Diagram Page 4 of 4 ...