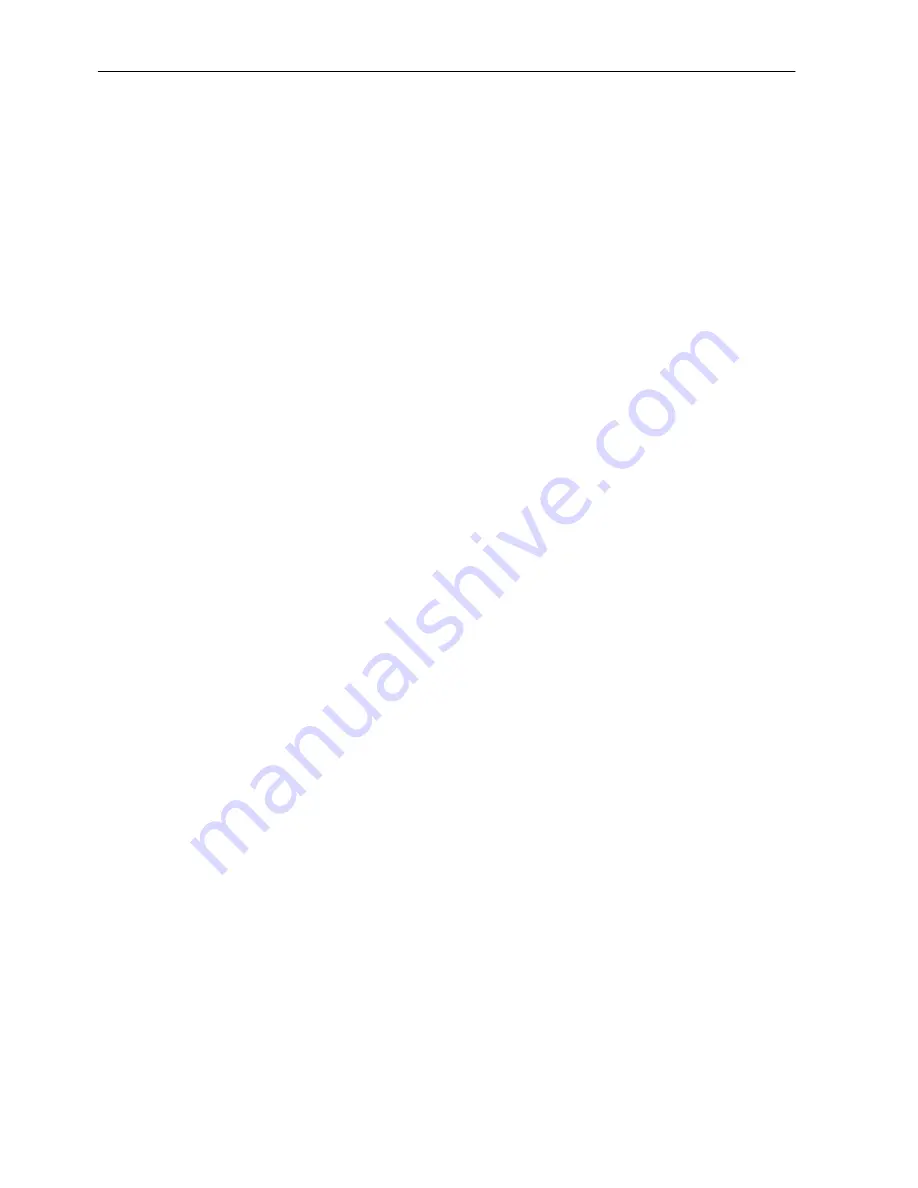
Refrigeration Service Operations
118
Compressor
Removal
1. Pump down the compressor and equalize the
pressure to slightly positive.
2. Loosen and remove the belts from the
compressor pulley.
3. Front seat the discharge and suction service
valves. Recover the remaining refrigerant
from the compressor.
4. Unbolt the discharge valve and suction valves
from the compressor.
5. Disconnect the high pressure cutout switch
wires.
6. Remove the compressor mounting bolts.
7. Lift the compressor out of the unit. Keep the
compressor ports covered to prevent dust, dirt,
etc., from falling into the compressor.
NOTE: When the compressor is removed
from the unit, the oil level should be noted,
or the oil removed from the compressor
should be measured so that the same amount
of oil can be added before placing the
replacement compressor in the unit.
Installation
1. Lift the compressor into the unit and install
the mounting bolts.
2. Install the service valves using new gaskets
soaked in refrigeration oil. Connect the high
pressure cutout switch wires.
3. Pressurize the compressor and test for
refrigerant leaks.
4. If no leaks are found, evacuate the
compressor. Replace the belts and adjust the
tensions.
5. Back seat the suction and discharge service
valves.
6. Operate the unit at least 30 minutes and then
inspect the oil level in the compressor. Add or
remove oil if necessary.
7. Check the refrigerant charge and add
refrigerant, if needed.
Condenser/Radiator Coil
Removal
1. Remove the refrigerant charge.
2. Remove the grille assembly.
3. Drain engine coolant and disconnect the
coolant hoses from the condenser/radiator
coil.
4. Unsolder the inlet line and liquid line
connections.
5. Unbolt and remove the condenser/radiator
coil.
Installation
1. Clean the tubes for soldering.
2. Place the condenser/radiator coil in the unit
and install the mounting hardware.
3. Solder the inlet line and liquid line
connections.
4. Pressurize refrigeration system and test for
leaks. If no leaks are found, evacuate the
system.
5. Connect the coolant hoses to radiator and refill
the cooling system tank with 50/50 ethylene
glycol/water solution.
6. Recharge the unit with refrigerant.
7. Reinstall the front grille.
Drier
Removal
1. Pump down the low side and equalize the
pressure to slightly positive.
2. Disconnect the ORS nuts at the ends of the
drier.
3. Loosen the mounting hardware and remove
the drier.
Содержание 920000
Страница 4: ......
Страница 10: ...Table of Contents 10...
Страница 22: ...Specifications 22...
Страница 41: ...Unit Description 41 Unit Photographs Figure 12 Front View Figure 13 Top View ARD026 AGA267...
Страница 42: ...Unit Description 42 Figure 14 Engine Side Door Open ARD041...
Страница 76: ...Electrical Maintenance 76...
Страница 132: ...Hilliard Clutch Maintenance 132...
Страница 134: ...Structural Maintenance 134...
Страница 146: ...Refrigeration Diagnosis 146...
Страница 148: ...Remote Evaporator Specifications 148...
Страница 150: ...Remote Evaporator Maintenance Inspection Schedule 150...
Страница 154: ...Remote Evaporator Unit Description 154...
Страница 158: ...Remote Evaporator Structural Maintenance 158...
Страница 160: ...Remote Evaporator System Diagnosis 160...
Страница 164: ...Wiring and Schematic Diagrams Index 164...
Страница 165: ...165 MD RD MT Model 30 w In Cab Schematic Diagram Page 1 of 2...
Страница 166: ...166 MD RD MT Model 30 w In Cab Schematic Diagram Page 2 of 2...
Страница 167: ...167 MD RD MT Model 30 w In Cab Wiring Diagram Page 1 of 3...
Страница 168: ...168 MD RD MT Model 30 w In Cab Wiring Diagram Page 2 of 3...
Страница 169: ...169 MD RD MT Model 30 w In Cab Wiring Diagram Page 3 of 3...
Страница 170: ...170 MD RD MT Model 30 w In Cab CYCLE SENTRY Schematic Diagram Page 1 of 2...
Страница 171: ...171 MD RD MT Model 30 w In Cab CYCLE SENTRY Schematic Diagram Page 2 of 2...
Страница 172: ...172 MD RD MT Model 30 w In Cab CYCLE SENTRY Wiring Diagram Page 1 of 3...
Страница 173: ...173 MD RD MT Model 30 w In Cab CYCLE SENTRY Wiring Diagram Page 2 of 3...
Страница 174: ...174 MD RD MT Model 30 w In Cab CYCLE SENTRY Wiring Diagram Page 3 of 3...
Страница 175: ...175 MD RD MT Model 30 CYCLE SENTRY Wiring Diagram Page 1 of 3...
Страница 176: ...176 MD RD MT Model 30 CYCLE SENTRY Wiring Diagram Page 2 of 3...
Страница 177: ...177 MD RD MT Model 30 CYCLE SENTRY Wiring Diagram Page 3 of 3...
Страница 178: ...178 MD RD MT Model 50 w In Cab Schematic Diagram Page 1 of 2...
Страница 179: ...179 MD RD MT Model 50 w In Cab Schematic Diagram Page 2 of 2...
Страница 180: ...180 MD RD MT Model 50 w In Cab Wiring Diagram Page 1 of 3...
Страница 181: ...181 MD RD MT Model 50 w In Cab Wiring Diagram Page 2 of 3...
Страница 182: ...182 MD RD MT Model 50 w In Cab Wiring Diagram Page 3 of 3...
Страница 183: ...183 MD RD MT Model 50 w In Cab CYCLE SENTRY Schematic Diagram Page 1 of 2...
Страница 184: ...184 MD RD MT Model 50 w In Cab CYCLE SENTRY Schematic Diagram Page 2 of 2...
Страница 185: ...185 MD RD MT Model 50 w In Cab CYCLE SENTRY Wiring Diagram Page 1 of 3...
Страница 186: ...186 MD RD MT Model 50 w In Cab CYCLE SENTRY Wiring Diagram Page 2 of 3...
Страница 187: ...187 MD RD MT Model 50 w In Cab CYCLE SENTRY Wiring Diagram Page 3 of 3...
Страница 188: ...188 MD RD MT Model 50 CYCLE SENTRY Wiring Diagram Page 1 of 3...
Страница 189: ...189 MD RD MT Model 50 CYCLE SENTRY Wiring Diagram Page 2 of 3...
Страница 190: ...190 MD RD MT Model 50 CYCLE SENTRY Wiring Diagram Page 3 of 3...