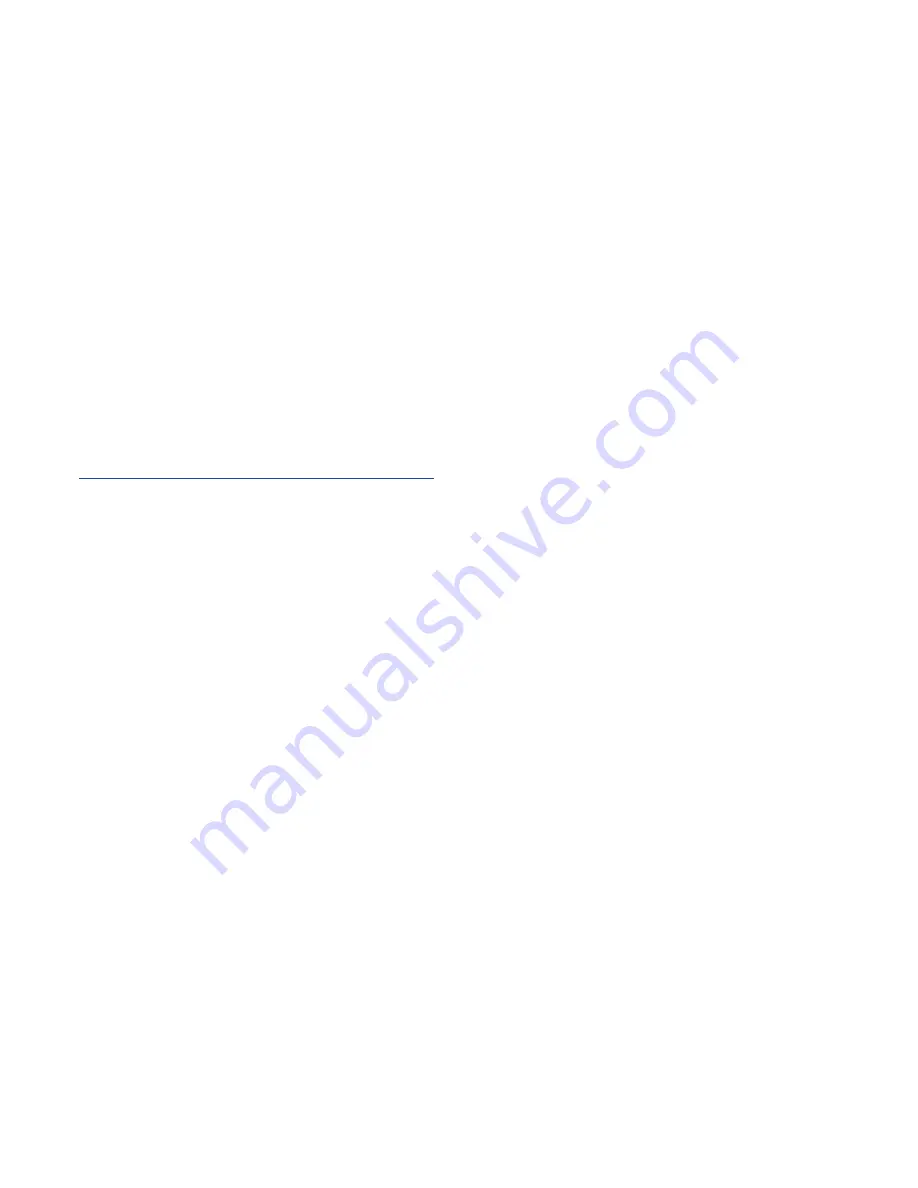
3
Chillers with an integral water-cooled or air-cooled
condenser ship with a full refrigerant charge. Chillers
designed for use with a remote air-cooled condenser
and the remote condensers themselves ship with a
nitrogen holding charge. Check the remote
condenser for signs of leaks prior to rigging. This will
ensure no coil damage has occurred after the unit
left the factory. The condenser ships with the legs
removed. Mount the legs to the condenser using the
provided nuts, bolts, and washers.
Unit Storage
When storing the unit it is important to protect it
from damage. Blow out any water from the unit;
cover it to keep dirt and debris from accumulating or
getting in, and store in an indoor sheltered area that
does not exceed 145°F.
Installation - Chiller
Foundation
Install the unit on a rigid, non-warping mounting
pad, concrete foundation, or level floor suitable to
support the full operating weight of the equipment.
When installed the equipment must be level within
¼ inch over its length and width.
Unit Location
The unit is available in many different configurations
for various environments. Refer to the proposal and
order acknowledgement document for the
equipment to verify the specific design conditions in
which it can operate.
To ensure proper airflow and clearance space for
proper operation and maintenance allow a minimum
of 36 inches of clearance between the sides of the
equipment and any walls or obstructions. Avoid
locating piping or conduit over the unit to ensure
easy access with an overhead crane or lift to lift out
heavier components during replacement or service.
In addition, ensure the condenser and evaporator
refrigerant pressure relief valves can vent in
accordance with all local and national codes.
Air-cooled chillers use the surrounding air for
cooling the condenser and require free passage of
air in and out of the chiller and provision for removal
of the warm air from the area.
Rigging
The chiller has a frame to facilitate easy movement
and positioning with a crane or forklift. Follow
proper rigging methods to prevent damage to
components. Avoid impact loading caused by
sudden jerking when lifting or lowering the chiller.
Use pads where abrasive surface contact may occur.
Chilled Process Fluid Piping
Proper insulation of chilled process fluid piping is
crucial to prevent condensation. The formation of
condensation adds a substantial heat load to the
chiller.
The importance of properly sized piping cannot be
overemphasized. See the ASHRAE Handbook or
other suitable design guide for proper pipe sizing. In
general, run full size piping out to the process and
reduce pipe size at connections as needed. One of
the most common causes of unsatisfactory chiller
performance is poor piping system design. Avoid
long lengths of hoses, quick disconnect fittings, and
manifolds wherever possible as they offer high
resistance to water flow. When manifolds are
required, install them as close to the use point as
possible. Provide flow-balancing valves at each
machine to assure adequate water distribution in the
entire system. Typically, when piping is overhead
with a total run over 90 feet, there should be a check
valve in the supply line and an inverted P trap with a
vacuum break valve installed 12 inches above the
highest point in the system.
All standard portable chillers include an internal
coolant pump and reservoir. Nominal coolant flow
rates assume a 10°F rise across the evaporator at
50°F set point and 85°F entering condenser water for
water-cooled chillers or 95°F entering air for integral
air-cooled or remote air-cooled condenser chillers.
Condenser Water Piping
(Water-Cooled Condenser Units Only)
The performance of a water-cooled condenser is
dependent on the flow and temperature of the
cooling water used. Insufficient cooling of the
condenser will result in the reduction of cooling
capacity of the chiller and under extreme conditions
may result in the chiller shutting down due to high
refrigerant pressure. Allowing the condenser to plug
up from contaminants in the condenser water