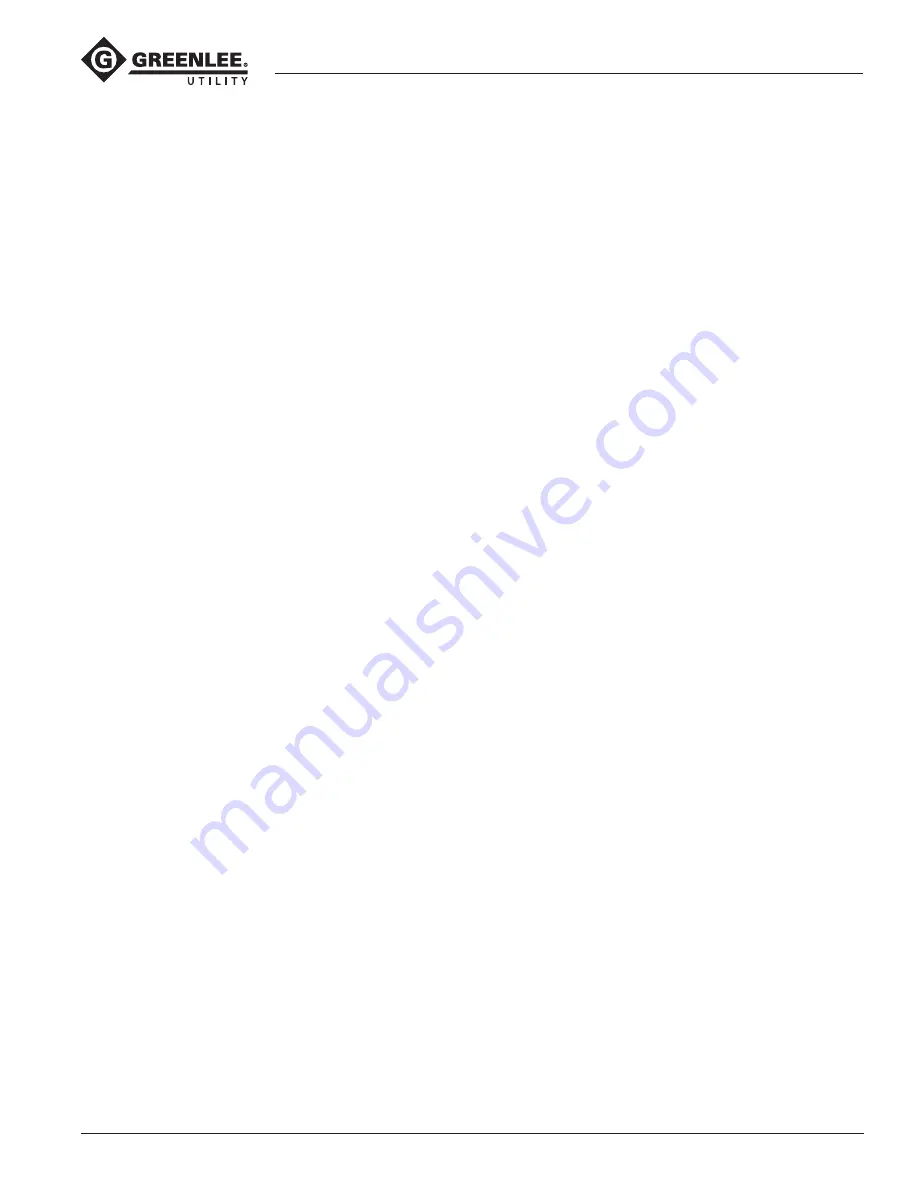
H4665A Submersible Pump
Greenlee / A Textron Company
4455 Boeing Dr. • Rockford, IL 61109-2988 USA • 815-397-7070
51
SERVICE
Disassembly
Complete disassembly of the tool is not recommended.
If a complete overhaul is necessary, return the tool to
your nearest Greenlee Utility Authorized Service Center.
The disassembly procedure is divided into sections of
the tool. Disassemble only the section(s) necessary to
complete the repair.
Disassemble the tool on a flat, clean surface. Take care
not to lose or damage any parts that may fall free during
disassembly.
Base and Inlet Screen (Strainer)
Note: Mating surfaces of impeller (29) and inlet (32) are
critical. Use every caution to prevent damage to these
parts.
1. Remove six hex head cap screws (35), lock washers
(36) and flat washers (37) to remove base (34), inlet
screen (strainer) (38), and six bushings (33).
2. Remove inlet (32) and shim(s) (31) from volute (24).
Impeller
Lock impeller (29) in place by placing a screwdriver
between the blades. Remove left-handed acorn nut (30)
by turning it clockwise. Remove impeller (29), key (28)
and shims (26, 27) from drive shaft (3).
Handle, Motor, and Volute
1. Remove two socket head cap screws (25) to remove
handle assembly from volute (24). If necessary,
remove two hex head cap screws (41) to disassem-
ble handle components (39, 40).
2. Remove the other three socket head cap screws
(25) to remove motor assembly from volute (24).
Retainer
Serial number 97720 and after:
1. Remove six socket head cap screws (22) to remove
retainer (18) from motor assembly.
2. Remove quad ring/O-ring (16) and two O-rings
(19, 20) from retainer (18).
3. If necessary, remove retaining ring (17) from retainer
(18) to remove bearing (15).
Retainer and Seal Carrier
Serial number before 97720:
1. Remove six socket head cap screws (22) to remove
retainer (B) from motor assembly.
2. Remove retaining ring (G) to remove seal carrier (F)
from retainer (B).
3. Remove two quad rings (D) and two O-rings (C, E)
from seal carrier (F).
4. Remove two O-rings (A) and one O-ring (19) from
retainer (B).
Motor
1. Scribe a line across motor cap (12) and motor body
(1) to align parts correctly during assembly.
2. Remove eight socket head cap screws (14) and pull
motor cap (12) off motor body (1). Remove gasket
(11). If necessary, remove two dowel pins (6) from
motor body (1).
3. Pull idler shaft (8) with gear out of motor body.
Remove gear (7) from idler shaft (8). If necessary,
remove drive pin (9) from idler shaft.
4. Remove gear (7) and Woodruff key (10) from drive
shaft (3).
5. Pull drive shaft (3) by removing retaining ring (5).
6. Remove O-ring (23) from motor body (1).
Note: Serial number before 97720: Remove
O-ring (H) below bearing in motor body (I) using an
O-ring tool.
Needle and Bearing Removal
Note: If the needle bearings (2, 13) in motor cap (12) or
motor body (1) are damaged or worn, Fairmont recom-
mends to replace the components as an assembly with
the bearings already pressed in.
1. Do not remove the needle bearings (2, 13) unless
they are damaged or worn. Bearings will be ruined
when they are removed.
2. Use a blind-hole bearing puller to remove the bear-
ings from the motor cap or motor body.
Inspection
Clean all parts with solvent and dry them thoroughly.
Inspect each component as described in this section.
Replace any component that shows wear or damage.
1. Bearings (4, 15) and Drive Shaft (3): Insert shaft into
bearings. Spin shaft. If shaft does not spin smoothly,
replace bearings and drive shaft.
2. Motor Cap (12) and Motor Body (1): Inspect mating
surfaces, gear cavities, oil passageways, etc. for
grooves or nicks. If any component shows wear or
damage, replace the component as an assembly
with the bearings already pressed in.
3. Inspect all other disassembled components for
cracks, grooves, or nicks.