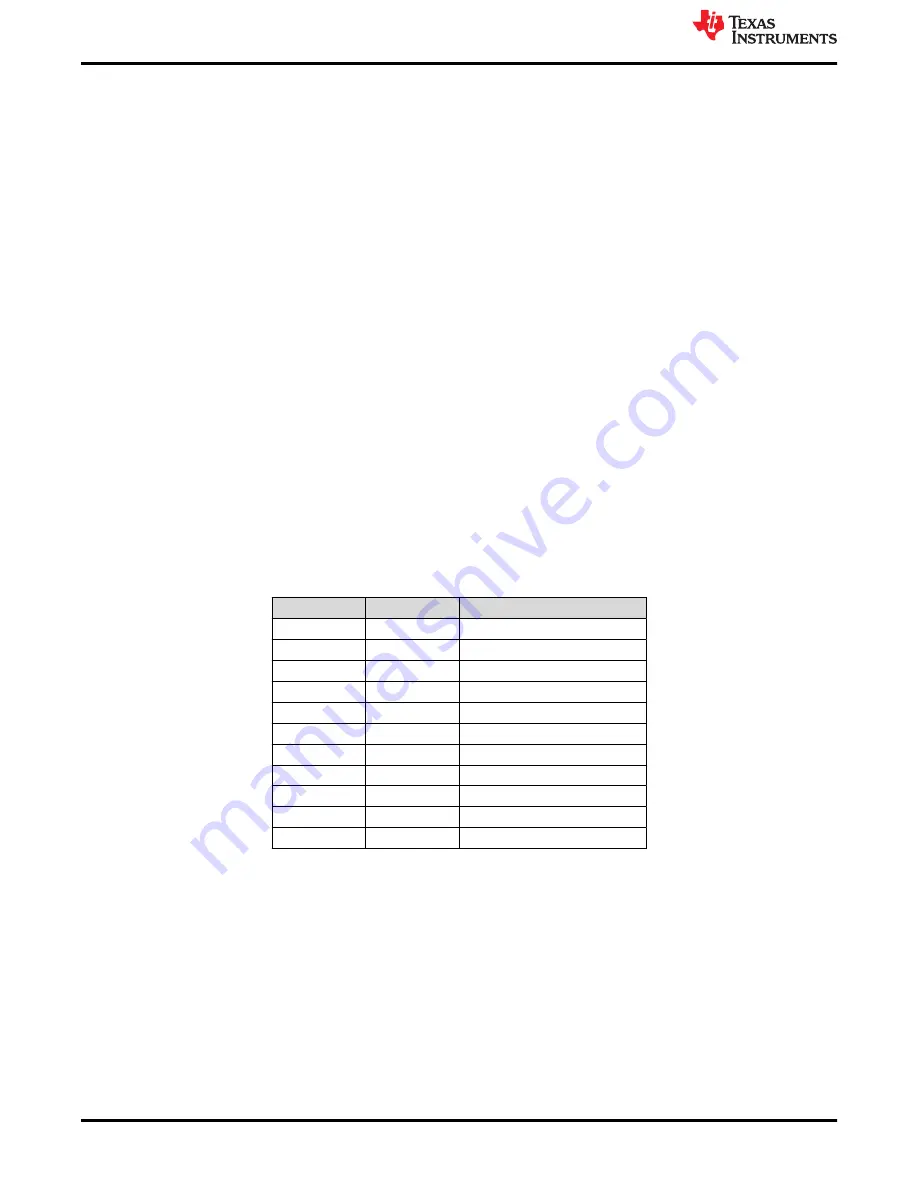
8 Test Procedure
8.1 Line/Load Regulation and Efficiency Measurement Procedure
1. Ensure that the load is set to constant resistance mode and to sink 0 A
DC
.
2. Ensure that the jumper provided in the EVM shorts on JP1 before V
IN
is applied.
3. Increase V
IN
from 0 V to 12 V, using V1 to measure input voltage.
4. Remove the jumper on JP1 to enable the controller.
5. Vary load from between 0 A
DC
and 25 A
DC
. V
OUT
should be remain in load regulation.
6. Vary V
IN
from 8 V to 14 V. V
OUT
should remain in line regulation.
7. Put the jumper on JP1 to disable the controller.
8. Decrease the load to 0 A.
9. Decrease V
IN
to 0 V.
8.2 Control Loop Gain and Phase Measurement Procedure
The TPS51113-EVM contains a 20-Ω series resistor in the feedback loop for loop response analysis.
1. Set up the EVM as described in
2. Connect the isolation transformer to test points marked TP4 and TP3.
3. Connect an input signal amplitude measurement probe (channel A) to TP4.
4. Connect an output signal amplitude measurement probe (channel B) to TP3. Connect the ground lead of
channel A and channel B to TP9 and TP10.
5. Inject around 40-mV or less signal through the isolation transformer.
6. Sweep the frequency from 100 Hz to 1 MHz with a 10-Hz or lower post filter. The control loop gain and
phase margin can be measured.
7. Disconnect the isolation transformer from the bode plot test points before making other measurements
(Signal injection into feedback may interfere with accuracy of other measurements).
8.3 Test Points
Table 8-1. Test Point Functions
TEST POINTS
NAME
DESCRIPTION
TP1
V
IN
+
12-V input
TP2
GND
PGND for V
IN
TP3
CHB
Input B for loop injection
TP4
CHA
Input A for loop injection
TP5
SW
Monitor switch node voltage
TP6
V
OUT
V
OUT
TP7
COMP
Enable/COMP
TP8
GND
PGND for V
OUT
TP9
GND
GND for loop measurement
TP10
PGND
PGND
TP11
PGOOD
Power Good
8.4 Equipment Shutown Procedure
1. Shut down the load.
2. Shut down V
IN
.
3. Shut down the fan.
Test Procedure
6
TPS51113 Buck Controller Evaluation Module User's Guide
SLUU359A – APRIL 2009 – REVISED FEBRUARY 2022
Copyright © 2022 Texas Instruments Incorporated