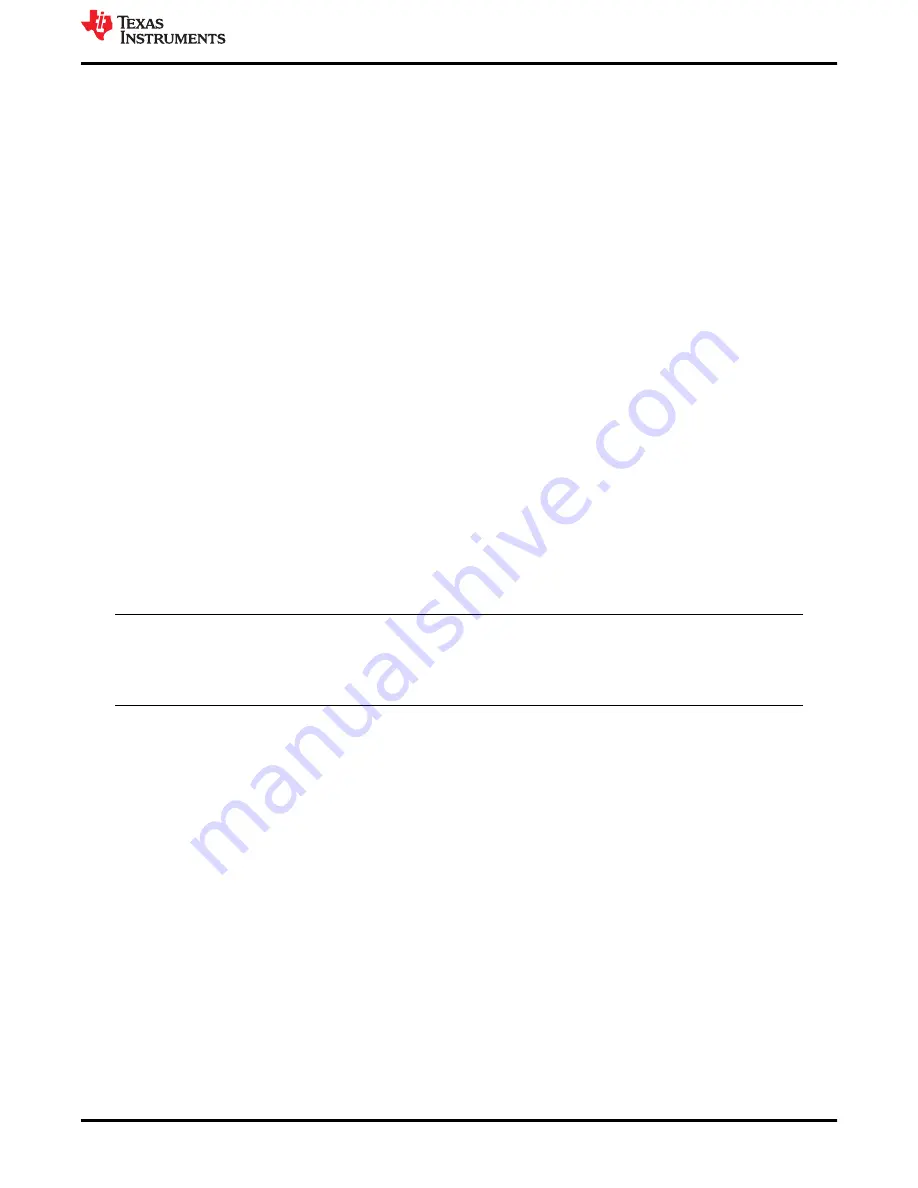
Step 1: Configure Motor stop options [MTR_STOP] to Recirculation Mode.
Step 2: Configure Recirculation Brake Time [RECIR_BRK_TIME] to “Auto configured”.
Preventing supply voltage overshoot during motor deceleration:
Enable Anti-voltage surge (AVS) [AVS_EN]
4.3.9 Protecting against rotor lock or stall condition
Follow below recommendations based on the type of fault triggered by MCT8316A.
Case 1: Follow below recommendations ff motor gets locked due to LOCK_LIMIT fault. Device triggers
LOCK_LIMIT fault when the motor accelerates in closed loop or when the motor is overloaded.
Step 1: Increase lock detection current threshold [LOCK_ILIMIT]
Step 2: Increase the Lock detection current limit deglitch time [LOCK_ILIMIT_DEG] if the motor can withstand
[LOCK_ILIMIT] for [LOCK_ILIMIT_DEG] time.
Step 3: Decrease CL_ACC.
Step 4: Enable dynamic degauss.
Case 2: Follow below recommendations if the device triggers CBC_ILIMIT, MTR_LCK, LOSS_OF_SYNC or
ABN_SPEED.
Step 1: Increase CBC current limit
Step 2: Decrease CL_ACC.
Step 3: Enable dynamic degauss.
Case 3: If the device does not trigger any fault and if the motor vibrates, decrease abnormal speed threshold.
Case 4: If the motor is loaded at lower speeds, MTR_LCK fault might get triggered when Min duty cycle is set
too low. We recommend to se the Min duty cycle after loading the motor at lower speeds.
Note
MCT8316A provides options to either latch LOCK_LIMIT fault or auto retry for
[AUTO_RETRY_TIMES] after every [LCK_RETRY] seconds. This can be configured in
LOCK_ILIMIT_MODE. We have defaulted the auto retry time and lock retry.
4.3.10 Maximizing thermal efficiency and increasing thermal performance
Thermal performance can be improved by minimizing power dissipation. Power dissipation across R
DS(on)
,
Switching losses and operating supply current dissipation are the major sources of Power dissipation in
MCT8316A. Power dissipation across R
DS(on)
is fixed as MOSFETs are integrated in MCT8316A. Please follow
below recommendations to minimize switching losses and operating supply current dissipation.
Step 1: Increase Gate driver Slew rate [SLEW_RATE]
Please note that increasing Slew rate will increase EMI noise.
Step 2: Decrease PWM output frequency [PWM_FREQ_OUT]
Please note that decreasing PWM output frequency may lead to discontinuous phase current for very low
inductance motors.
Step 3: Disable Buck regulator [BUCK_DIS]. Disabling buck regulator will reduce the device standby and sleep/
quiescent current.
Please note that any external load on buck regulator will have to be powered by external power source and not
by the device.
Step 4: Configure PWM modulation [PWM_MODUL] to Mixed modulation. In this modulation scheme, the
switching losses among high and low side MOSFETs are evenly distributed.
Basic Controls
SLLU336 – MAY 2021
MCT8316A Tuning Guide
21
Copyright © 2021 Texas Instruments Incorporated