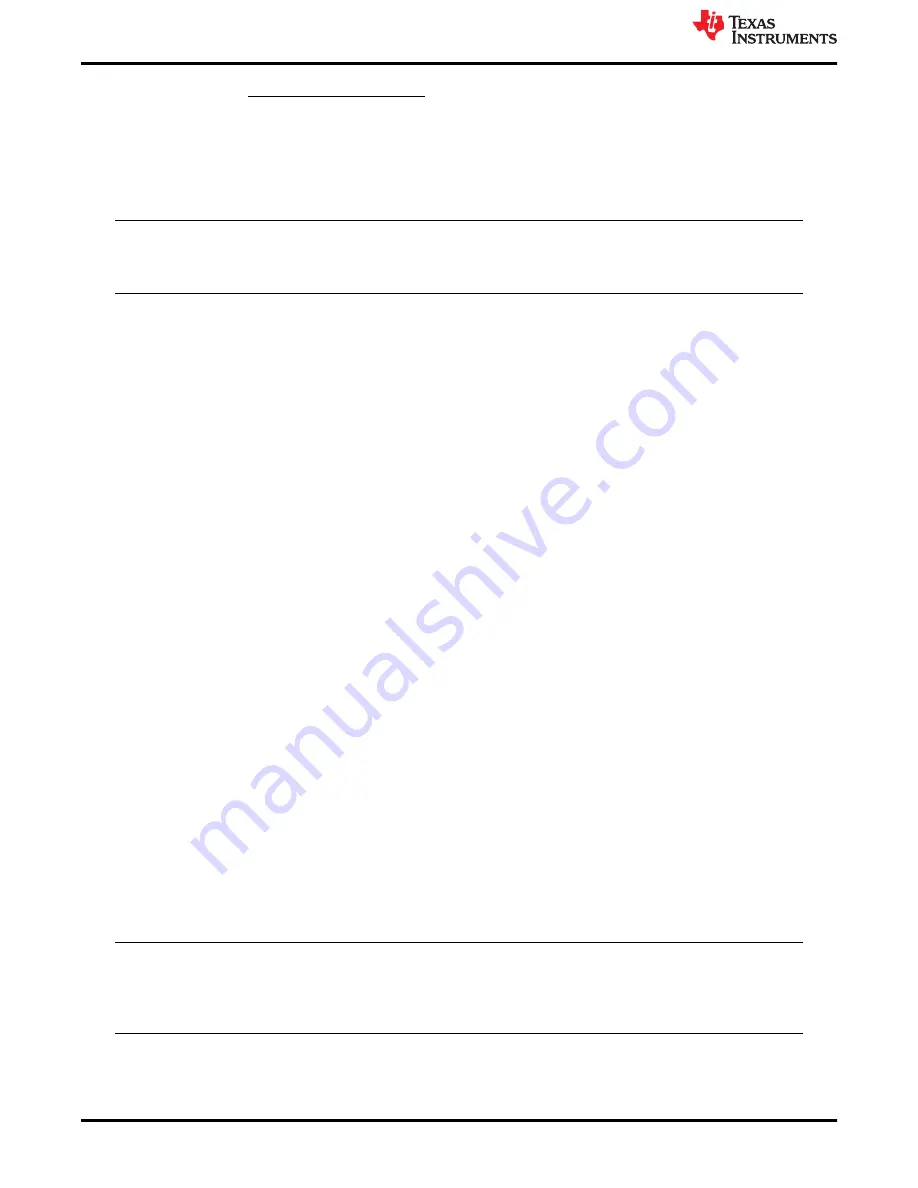
Speed loop Kp =
Iq reference at maximum speed
Maximum Electrical Speed in Hz
(6)
Step 9: Speed loop Ki [SPD_LOOP_KI] is calculated using equation
.
Speed loop Ki = 0.1 × Speed loop Kp
(7)
Step 10: Enable speed loop [SPEED_LOOP_DIS]
Note
Tuning speed loop Kp and Ki is experimental. If the above recommendation doesn’t work, then we
recommend to manually tune Speed loop Kp and Ki till the desired results are achieved.
4.3.8 Stopping Motor Quickly
For applications that require stopping the motor quickly, it is recommended to configure Motor stop options
[MTR_STOP] to either High side braking or Low side braking.
Step 1: Configure Motor stop options [MTR_STOP] to either High side braking or Low side braking.
Step 2: Select Speed threshold for BRAKE pin and Motor STOP options. Setting speed threshold to higher
speed would result in FETs carrying large current. Setting speed threshold to lower speed would increase the
stop time of the motor. It is recommended to start with 50% of the maximum speed. If the device triggers
Overtemperature warning [OTW] or Overtemperature shutdown [OTS], it is recommended to decrease the
threshold. If the stop time is too high, it is recommended to increase the threshold.
4.3.9 Preventing Supply Voltage Overshoot During Motor Stop.
For applications that require preventing supply voltage overshoots during motor stop, it is recommended to
select active spin down or recirculation brake as Motor stop options. Recirculation brake can be used as a motor
stop option in applications where fast stop is not required, but any inductive energy going back to power supply
is not acceptable. Active spin down can be used as a motor stop option in applications where fast stop is not
required but some amount of inductive energy going back to power supply is acceptable
Option 1:
Recirculation Mode
Step 1: Configure Motor stop options [MTR_STOP] to Recirculation Mode.
Step 2: Configure Recirculation Brake Time [RECIR_BRK_TIME].. If there is voltage overshoot on Vm during
motor stop, configure RECIR_BRK_TIME long enough to prevent overshoot on Vm pin.
Option 2:
Active spin down
Step 1: Configure Motor stop options [MTR_STOP] to Active spin down
Step 2: Configure active spin down speed threshold [ACT_SPIN_THR]. It is recommended to set the
ACT_SPIN_THR to 50% of the maximum speed. If there is voltage overshoot seen on the power supply, it
is recommended to decrease the ACT_SPIN_THR till the voltage overshoot reaches acceptable limit.
4.3.10 Protecting Against Rotor Lock or Stall Condition
Follow below recommendations if the motor stalls or gets locked in closed loop when the motor is overloaded.
Increase lock detection current threshold [LOCK_ILIMIT]
Note
MCF8316A provides options to either latch LOCK_LIMIT fault or auto retry for
[AUTO_RETRY_TIMES] after every [LCK_RETRY] seconds. This can be configured in
LOCK_ILIMIT_MODE. We have defaulted the auto retry time and lock retry.
Basic Controls
20
MCF8316A Tuning Guide
SLLU335A – AUGUST 2021 – REVISED JANUARY 2022
Copyright © 2022 Texas Instruments Incorporated