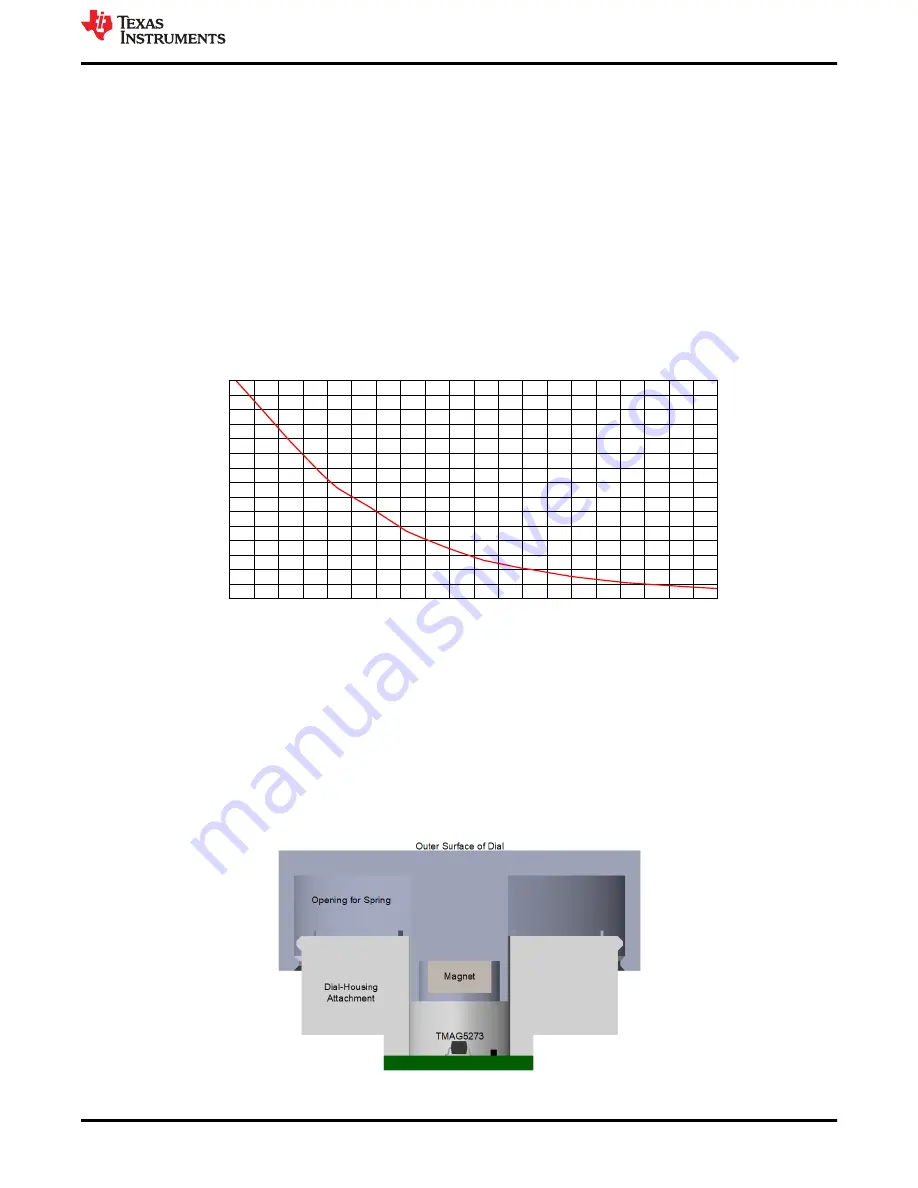
2.2.4 Magnetic Dial Implementation
The TMAG5273 is a 3D hall-effect sensor used to implement the dial in this design. Being a 3D device
allows it to detect the angle and magnitude of the magnet which enables the push-button functionality on the
dial. The integrated CORDIC engine of this device makes angular position sensing easy to implement in this
application. The angle of magnet is reported through the device register so no calculations are needed from
the MCU. Another device that can be used for this application is the TMAG5170-Q1, an automotive qualified
part that provides similar functionality. It also has the built in CORDIC engine and reports the magnet angle and
magnitude through the registers. The two parts are slightly different in that the TMAG5170-Q1 is a high precision
device that uses SPI for communication while the TMAG5273 is low power and uses I2C. This reference design
does not need high resolution to display the angle and has I2C as the main communication protocol so the
TMAG5273 was chosen. If automotive qualification is needed, the TMAG5170-Q1 would be used instead.
The magnet used in this device is an N42 diametric cylinder measuring 1/4th in diameter by 1/8th inch thick. This
magnet was chosen because it provides an input that uses a significant portion of the full-scale output range.
This provides a better SNR performance for the device when used at a suitable distance for the design while still
being small and it is easy to obtain.
Distance [mm]
M
ag_B
(mT
esla)
0
0.4
0.8
1.2
1.6
2
2.4
2.8
3.2
3.6
4
4.4
4.8
5.2
5.6
6
6.4
6.8
7.2
7.6
8
0
15
30
45
60
75
90
105
120
135
150
165
180
195
210
225
Figure 2-5. Magnetic Field Strength Over Distance
The push functionality of the dial is achieved by adding a spring to the design. Most springs are ferromagnetic
and will interact with the magnetic field but the magnet chosen for this design has a field strong enough that
the spring can still be implemented without needing to find a specific non-ferromagnetic version. However, the
decrease in field strength also reduces the SNR for this design. This is combated by implementing averaging in
the magnetic measurement. The TMAG5273 has a register setting that can be used to change the averaging of
the sensor data. Since high speed measurements are not needed in this application, the maximum averaging is
chosen for consistent results. Alternatively, the averaging can be turned down to the necessary value and the
sleep timer in the device can be used to put the device in low-power mode between samples for lower power
applications.
Figure 2-6. Magnetic Dial Push Button Stackup
System Overview
Inductive Touch and Magnetic Dial Contactless User Interface Reference
Design
7
Copyright © 2022 Texas Instruments Incorporated