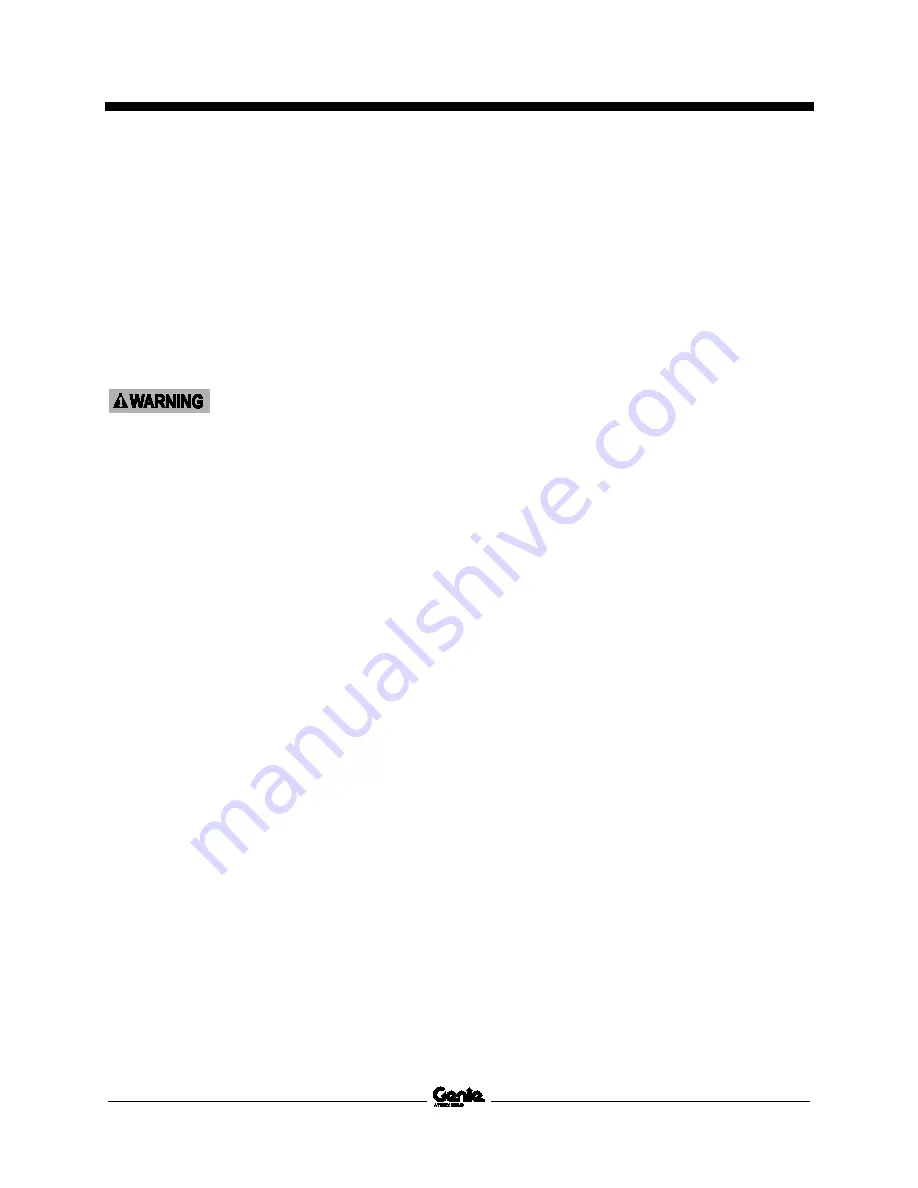
Service and Repair Manual
April 2018
Fuel and Hydraulic Tanks
40
GTH-1056
Part No. 1287211GT
10 Tag, disconnect and plug the fuel supply and
return hoses. Cap the fittings.
11 Tag, disconnect and plug the supply and
return hoses from the hydraulic tank. Cap the
fittings.
12 Support and secure the tank assembly to an
appropriate lifting device.
13 Remove the fasteners securing the tank
assembly to the chassis. Remove the tank
from the machine.
Crushing hazard. The tank
assembly could become
unbalanced and fall if not properly
supported when removed from
the machine.
Содержание Genie GTH1056
Страница 63: ...April 2018 Service and Repair Manual Manifolds Part No 1287211GT GTH 1056 53 ...
Страница 65: ...April 2018 Service and Repair Manual Manifolds Part No 1287211GT GTH 1056 55 ...
Страница 115: ...April 2018 Service and Repair Manual 105 Harness Map Harness Legend ...
Страница 116: ...Service and Repair Manual April 2018 106 GTH 1056 Part No 1287211GT Harness Map Harness Legend ...
Страница 117: ...April 2018 Service and Repair Manual Part No 1287211GT GTH 1056 107 Harness Map Control System Electronic Joystick ...
Страница 118: ...Service and Repair Manual April 2018 108 Harness Map Control System Electronic Joystick ...
Страница 119: ...April 2018 Service and Repair Manual 109 Harness Map Deutz T4F Engine ...
Страница 120: ...Service and Repair Manual April 2018 110 GTH 1056 Part No 1287211GT Harness Map Deutz T4F Engine ...
Страница 121: ...April 2018 Service and Repair Manual Part No 1287211GT GTH 1056 111 Harness Map Deutz T3 Engine ...
Страница 122: ...Service and Repair Manual April 2018 112 Harness Map Deutz T3 Engine ...
Страница 123: ...April 2018 Service and Repair Manual 113 Harness Map Perkins T4i Engine ...
Страница 124: ...Service and Repair Manual April 2018 114 GTH 1056 Part No 1287211GT Harness Map Perkins T4i Engine ...
Страница 125: ...April 2018 Service and Repair Manual Part No 1287211GT GTH 1056 115 Harness Map Perkins T3 Engi ne ...
Страница 126: ...Service and Repair Manual April 2018 116 Harness Map Perkins T3 Engine ...
Страница 127: ...April 2018 Service and Repair Manual 117 Harness Map Road Lights ...
Страница 128: ...Service and Repair Manual April 2018 118 GTH 1056 Part No 1287211GT Harness Map Road Lights ...
Страница 129: ...April 2018 Service and Repair Manual Part No 1287211GT GTH 1056 119 Harness Map Work Lights ...
Страница 130: ...Service and Repair Manual April 2018 120 Harness Map Work Lights ...
Страница 131: ...April 2018 Service and Repair Manual 121 Harness Map Deutz HVAC Option ...
Страница 132: ...Service and Repair Manual April 2018 122 GTH 1056 Part No 1287211GT Harness Map Deutz HVAC Option ...
Страница 133: ...April 2018 Service and Repair Manual Part No 1287211GT GTH 1056 123 Harness Map Perkins HVAC Option ...
Страница 134: ...Service and Repair Manual April 2018 124 Harness Map Perkins HVAC Option ...
Страница 135: ...April 2018 Service and Repair Manual 125 Harness Map Enclosed Cab Heater ...
Страница 136: ...Service and Repair Manual April 2018 126 GTH 1056 Part No 1287211GT Harness Map Enclosed Cab Heater ...
Страница 137: ...April 2018 Service and Repair Manual Part No 1287211GT GTH 1056 127 Harness Map Proximity Sensor Beacon Lockout Options ...
Страница 138: ...Service and Repair Manual April 2018 128 Harness Map Proximity Sensor Beacon Lockout Options ...
Страница 139: ...April 2018 Service and Repair Manual 129 Electrical Schematic View 1 ...
Страница 140: ...Service and Repair Manual April 2018 130 GTH 1056 Part No 1287211GT Electrical Schematic View 1 ...
Страница 141: ...April 2018 Service and Repair Manual Part No 1287211GT GTH 1056 131 Electrical Schematic View 2 500 ...
Страница 142: ...Service and Repair Manual April 2018 132 Electrical Schematic View 2 ...
Страница 143: ...April 2018 Service and Repair Manual 133 Electrical Schematic Deutz T4F Eng Harness ...
Страница 146: ...Service and Repair Manual April 2018 136 Electrical Schematic Deutz T4F Eng Harness ...
Страница 147: ...April 2018 Service and Repair Manual 137 Electrical Schematic Deutz T4F Eng Harness ...
Страница 149: ...April 2018 Service and Repair Manual Part No 1287211GT GTH 1056 139 Electrical Schematic Deutz Tier 3 Eng Harness ...
Страница 150: ...Service and Repair Manual April 2018 140 Electrical Schematic Deutz T3 Eng Harness ...
Страница 151: ...April 2018 Service and Repair Manual 141 Hydraulic Schematic ...
Страница 152: ...Service and Repair Manual April 2018 142 GTH 1056 Part No 1287211GT Hydraulic Schematic ...
Страница 153: ...April 2018 Service and Repair Manual Part No 1287211GT GTH 1056 143 Hydraulic Schematic ...
Страница 155: ......