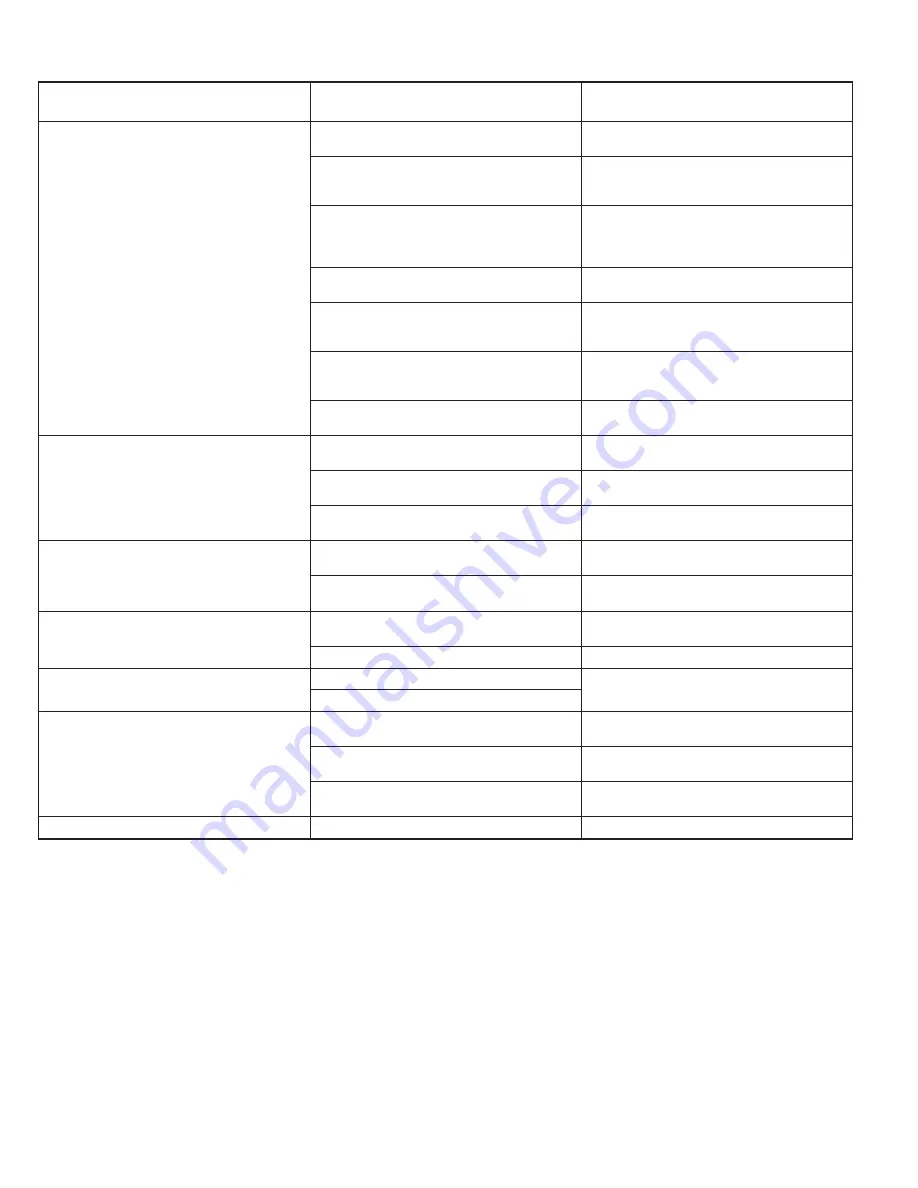
Troubleshooting Chart
PROBLEM
CAUSE
REMEDY
Motor Overheats
(Check temperature with instrumentation)
Motor not connected for proper supply
voltage
Check connection diagram on conduit box
cover and correct the wiring.
Supply voltage varies outside the allow-
able tolerance causing an undervoltage or
overvoltage condition.
Assure correct supply voltage.
Insufficient cooling air volume due to:
a. Low frequency operation on vari
able frequency drive.
b. Obstructed air flow.
Increase air flow:
a. Continuous running auxiliary fan.
b. Ensure unobstructed air flow.
Ambient temperature is too high.
Ensure cool air gets to the motor. Ducting
may be required.
Overload at rated voltage. Unit will draw
current in excess of nameplate rating and
run below rated speed.
Select a larger unit.
Motor’s allowable duty cycle is exceeded
(too many starts per hour required).
The problem may or may not be solved
with a larger motor. Contact SEW-
Eurodrive.
Single phasing due to break or loose con-
nection in supply line or blown fuse.
Repair supply lines.
Replace fuses.
Motor does not run.
Blown fuse.
Determine and correct cause of failure and
replace fuse.
Motor protection device activated.
Reset protective device. Identify and
correct cause for device activation.
Motor protection device faulty or will not
reset.
Check protection device for faults.
Motor will not start or starts sluggishly.
Motor not connnected for proper voltage.
Check connection diagram in conduit box
cover and correct the wiring.
Large voltage and/or frequency fluctuation
at starting.
Ensure stable power supply.
For reduced voltage starting, motor will not
start in Star Connection but will start in
Delta connection.
Insufficient torque in Star Connection.
Start motor directly in Delta Connection if
possible. Otherwise use a larger motor.
Faulty contact in Star/Delta starter.
Correct fault condition.
Motor hums and draws high current.
Faulty or defective winding.
Have motor repaired by qualified service
shop.
Rotor dragging.
Fuses blow or motor overcurrent protection
trips immediately.
Short circuit in power supply conductors or
in the motor.
Correct the fault condition.
Motor has ground fault or winding to wind-
ing short circuit.
Have motor repaired by qualified service
shop.
Motor improperly connected.
Check connection diagram in conduit box
cover and correct the wiring.
Motor runs in wrong direction.
Motor supply leads misconnected.
Switch two supply leads.
Note: If, after proceeding through the Troubleshooting Chart, the motor is found to be defective, contact your nearest SEW-Eurodrive Assembly Center
for warranty assistance or replacement parts.
Printed in USA
6
0201
Содержание LM1010-2x
Страница 5: ...4...
Страница 8: ...7 LM Control Box Overlay...
Страница 15: ...14 LM Machine PARTS View...
Страница 17: ...16 LM 2x Back gauge Crank Assembly...
Страница 21: ...20 LM 2x Back gauge Drive Assembly...
Страница 26: ...25 LM1010 WIRING DIAGRAM...
Страница 28: ...27 LM1010 OPTIONS WIRING DIAGRAM...