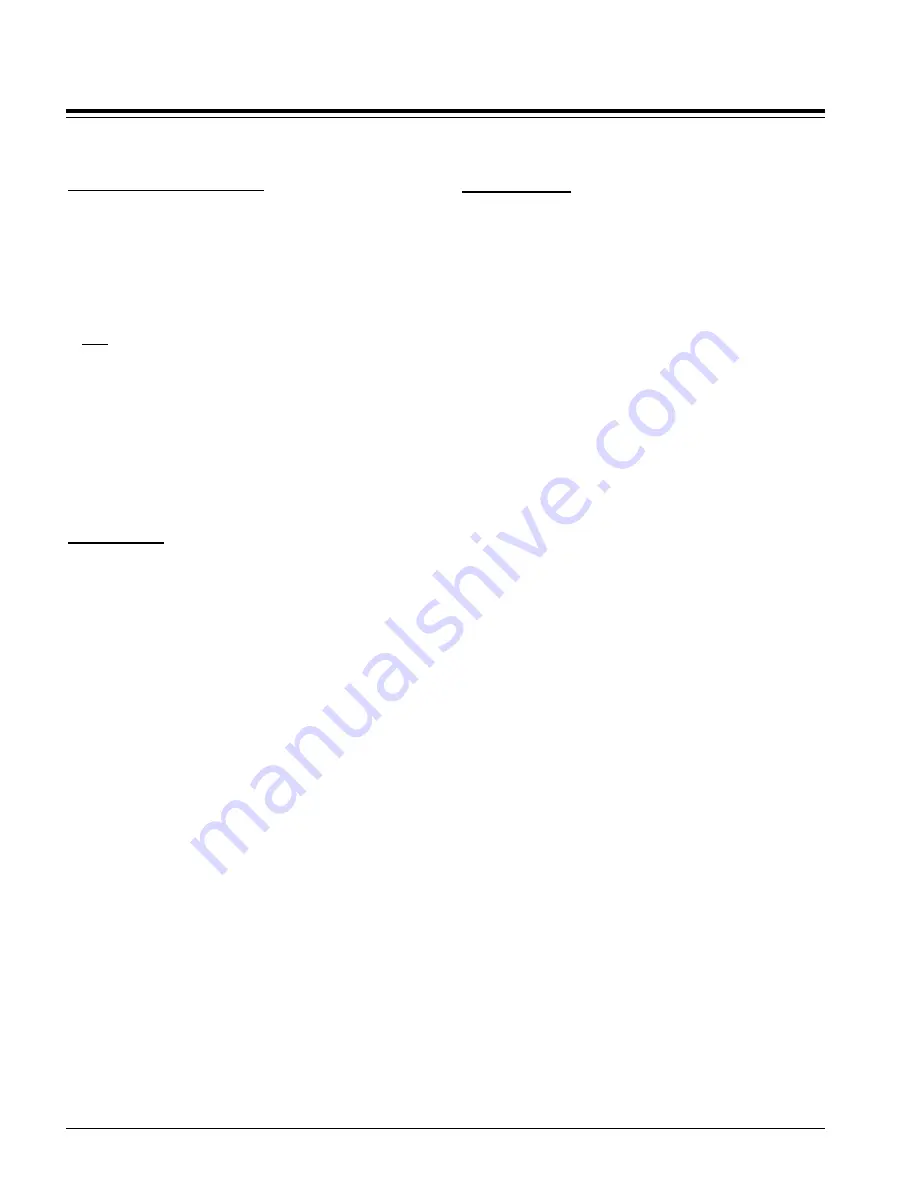
BenchMark
®
200/BM470 Marking System
6 of 8
34743A
BM470 CONTROLLER
(continued)
Environmental Considerations
The following environmental considerations must be taken into
account when installing the BM470 controller.
Contaminants.
The vented and fan-cooled controller is rated
NEMA 1 (IP30). Accordingly, in environments where solid
and/or liquid contaminants are present, the possibility exists
that these contaminants can be drawn into the controller and
possibly result in failure of a number of electronic components.
For that reason, in these types of environments, the controller
must be located in a sealed industrial enclosure.
EMI Susceptibility.
Although the system has been found to be
in compliance with pertinent susceptibility standards, care
should be taken when installing near welders and other extreme
generators of electromagnetic interference (EMI). Particular
care should be taken to ensure welder currents are not injected
through the marking head chassis. The marking head chassis is
connected to the electrical service earth ground through the
marking head cable. The marking head should be electrically
isolated from all surfaces which could become part of a welder
current path.
Interface Panel
The back panel of the controller provides various ports for
connecting the marker and optional accessories. See below.
Marker Port.
The Marker port connects the BenchMark200
marking head to the BM470 Controller. It supplies the marking
head with electrical power and provides input/output signals to
and from the controller for marker operation
TTL Port
is configured for VDC input only. It allows the system
to connect with a simple contact closure circuit such as a remote
push button station or foot pedal switch. These types of devices
can remotely control Start Print and Stop (Abort) Print operations.
Comm Port
allows connection to a remote serial device. The
Comm port may be used to connect an optional, customer-
supplied PC to access Telesis software utilities. Utility software
may be used to backup patterns stored in the controller, to
download a custom font to the controller, or to download
controller software upgrades. The Comm port also allows you to
connect an optional bar code scanner. The software reads the
scanned input and inserts the data into a variable text field within
the currently loaded pattern.
USB Port
allows you to connect a memory stick/flash drive for
pattern storage/retrieval and for software upgrades.
(optional) Auxiliary Axis Port
is available only if the controller is
configured with the optional auxiliary-axis circuit card. This
configuration allows connection to a rotational drive unit to make use
of the software’s Theta-axis features.
System Software
The system software is permanently installed in the controller. It
provides the user interface for the operator to control the marker.
The software also provides a library for storing, loading, and
editing user-defined patterns.
Patterns are files stored in the controller’s memory. Depending on
the size of the pattern files, the controller can store up to 200
patterns. Each pattern contains one or more fields; each field
defines a single object.
Printable objects may be created to define text strings, arc-text
strings, geometric shapes , graphics, and machine-readable data
matrix symbols. Printable text fields may include alphanumeric
characters, symbols, and special message flags. Message flags
automatically insert data into the text string, such as serial
numbers, times, dates and user-defined codes.
Non-printable objects may be defined to specify commands for the
marker to execute (e.g., Go To, Print, Stop).