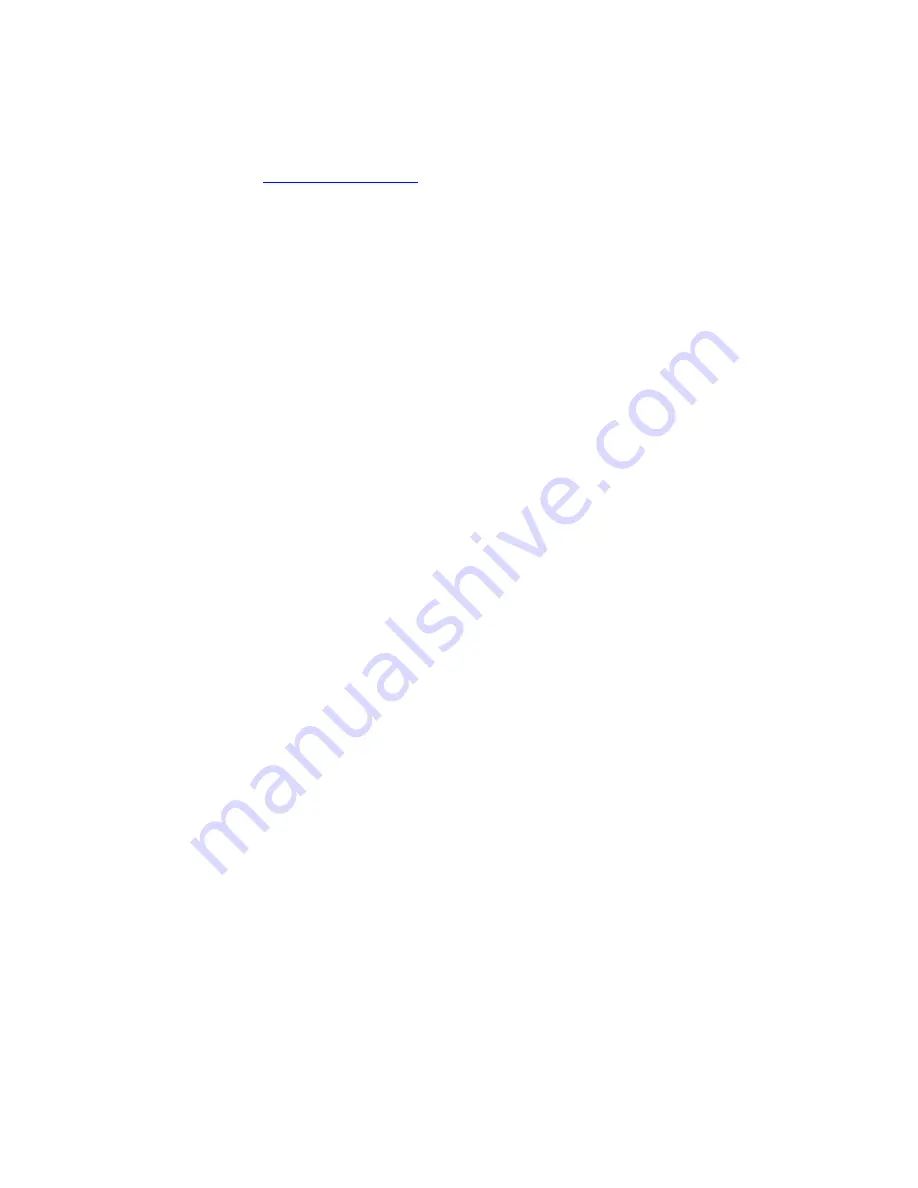
34
Calibration Cont’d
The accuracy of this setup will mainly be related to the quality of the load. If the dummy load error is 5%, then the power calculation will
be roughly 5% off. You can roughly guess at the RF resistance of your dummy load by measuring it at DC with a DMM, although that
method will most likely be inaccurate at 50 MHz, and probably at 28 MHz as well. Make sure you measure the resistance with the load
at operating temperature. Also, all connecting cables / adapters need to be as short as possible. If you are unsure of the quality of your
dummy load, I recommend visiting
to look at some of their offerings. These are high quality loads, and for a
small fee they will supply you with a calibration table and chart of the return loss of the load.
The actual diode drop will very likely be within about .2V of the assumed value in the formula, for a voltage error of under 2%.
If you don’t have access to these methods, you can send your completed LP-100A back to me for calibration if you are willing to pay for
return shipping costs.
The first step in power calibration is to set the Master Trim value. This should be done on 3.5 or 7.0 MHz. Make sure the Fine Trim
setting for this band is 1.000, then transmit at a known power level and adjust the Master Trim for the correct power reading. The Mstr
setting will not be touched after this.
To adjust the Fine power constants for each band, simply transmit on the band of interest and adjust the Dn/Up buttons for the correct
power readings. Move through all bands in sequence until they have all been adjusted. You will notice that when you transmit now, the
band indicator shows the band you are transmitting on and the Trim value changes automatically based on the band.
The Mstr Trim setting will typically be within 2% , and the variation of Fine Trim setting should be < 2% from 160-10m and <10% on 6m.
This is dependent on a number of factors to do with xfmr winding (mainly total % of core wound), positioning and wire routing, and so
will vary from builder to builder… BUT the calibration routine will eliminate any variances. Setting the fine trims to 1.000 should provide
less than 2% band-to-band variation through 10m. 6m can be as much as 10% off without specific calibration.
Log all your constants for future reference, and you’re done. There is a page at the end of this manual to make that easy.
NOTE:
Normal use of the LP-100A, including the flash programming of a new firmware version, will not disturb the saved CAL constants unless
you have the MCLoader software set to “Program Data”. Jotting the values down will allow you to return to your original settings in case
you accidentally change a value by mistake. I am planning a Windows utility to allow saving, editing and restoring of the CAL table.
Final details
If everything has checked out to this point, you can complete the assembly of the controller by adjusting the LEDs on the front panel to
line up with the holes, and snap the switch caps in place on the switches.
Note: If you need to remove the PCB in the future, you can
carefully pull of the square keycaps using a pliers or channel locks, but you will need to use a needle nose pliers on the shaft of the
power switch behind the panel to prevent stressing and damaging the internals of the switch.
Line everything up on the front and rear, and then tighten the four screws on the top of the PCB, and the four on the chassis bottom.
You can also attach the rear panel to the RCA connectors using the 4-
40 x 3/8” (9.53mm) self-tapping screw provided. Don’t
overtighten. Install the DB9 jack screws using #4 split lockwashers. Snug up but don’t overtighten. Snap the two plastic hole plugs into
the CH 2 coupler input holes.
You can now install the cover on the controller using the 4-
40 x ¼” (6.35mm) self-tapping screws provided.
Содержание LP-100A
Страница 18: ...18 Schematic Page 1...
Страница 19: ...19 Schematic Page 2 Coupler Schematic...