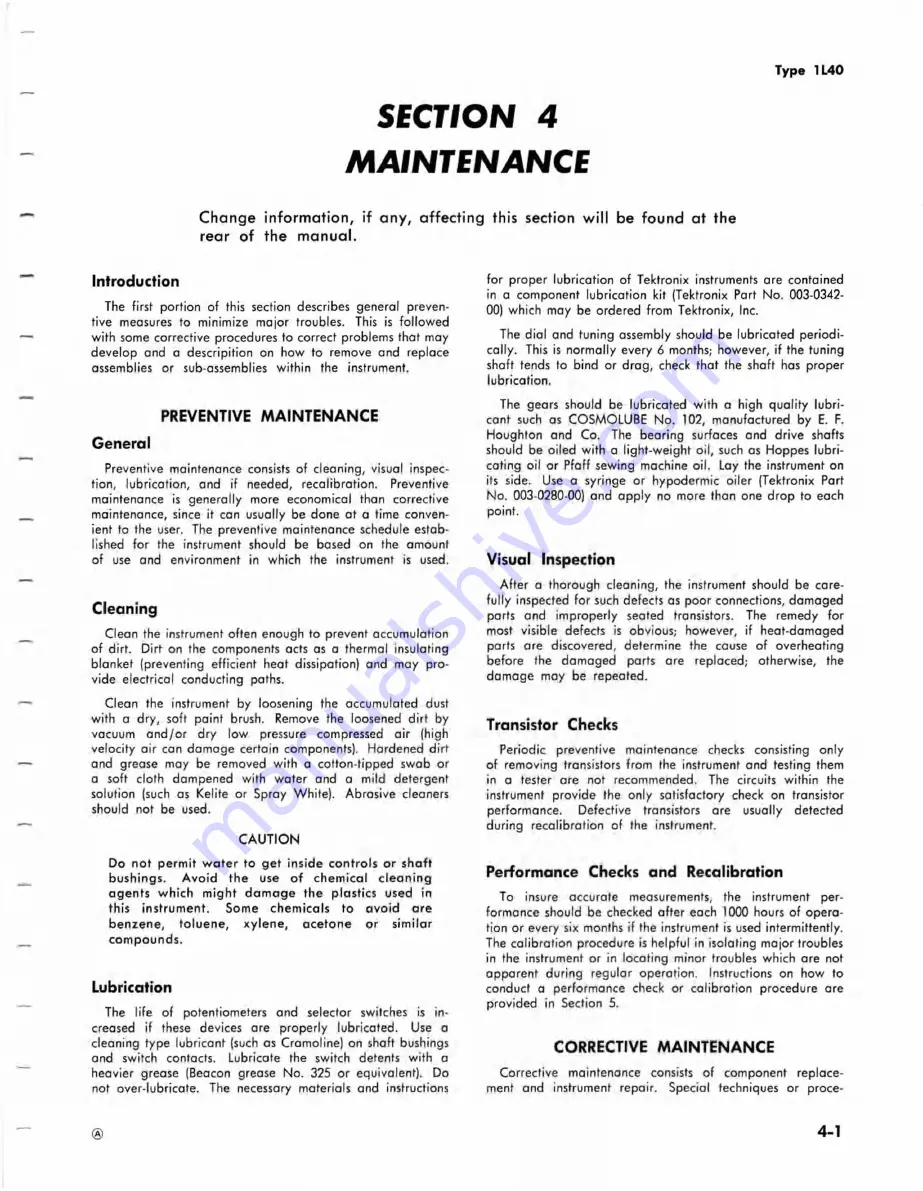
SECTION 4
MAINTENANCE
Type 1L40
Change information, if any, affecting this section will be found at the
rear of the manual.
Introduction
The first portion of this section describes general preven
tive measures to minimize major troubles. This is followed
with some corrective procedures to correct problems that may
develop and a descripition on how to remove and replace
assemblies or sub-assemblies within the instrument.
PREVENTIVE MAINTENANCE
General
Preventive maintenance consists of cleaning, visual inspec
tion, lubrication, and if needed, recalibration. Preventive
maintenance is generally more economical than corrective
maintenance, since it can usually be done at a time conven
ient to the user. The preventive maintenance schedule estab
lished for the instrument should be based on the amount
of use and environment in which the instrument is used.
Cleaning
Clean the instrument often enough to prevent accumulation
of dirt. Dirt on the components acts as a thermal insulating
blanket (preventing efficient heat dissipation) and may pro
vide electrical conducting paths.
Clean the instrument by loosening the accumulated dust
with a dry, soft paint brush. Remove the loosened d irt by
vacuum a n d /o r dry low pressure compressed air (high
velocity air can damage certain components). Hardened dirt
and grease may be removed with a cotton-tipped swab or
a soft cloth dampened with water and a mild detergent
solution (such as Kelite or Spray White). Abrasive cleaners
should not be used.
CAUTION
Do n o t perm it w a te r to get inside controls o r shaft
bushings.
A void the use o f chemical cleaning
agents w hich m ight dam age the plastics used in
this instrum ent.
Some chemicals to avoid are
benzene,
toluene,
xylene,
acetone or
sim ilar
compounds.
Lubrication
The life of potentiometers and selector switches is in
creased if these devices are properly lubricated. Use a
cleaning type lubricant (such as Cramoline) on shaft bushings
and switch contacts. Lubricate the switch detents with a
heavier grease (Beacon grease No. 325 or equivalent). Do
not over-lubricate. The necessary materials and instructions
for proper lubrication of Tektronix instruments are contained
in a component lubrication kit (Tektronix Part No. 003-0342-
00) which may be ordered from Tektronix, Inc.
The dial and tuning assembly should be lubricated periodi
cally. This is normally every 6 months; however, if the tuning
shaft tends to bind or drag, check that the shaft has proper
lubrication.
The gears should be lubricated with a high quality lubri
cant such as COSMOLUBE No. 102, manufactured by E. F.
Houghton and Co. The bearing surfaces and drive shafts
should be oiled with a light-weight oil, such as Hoppes lubri
cating oil or Pfaff sewing machine oil. Lay the instrument on
its side. Use a syringe or hypodermic oiler (Tektronix Part
No. 003-0280-00) and apply no more than one drop to each
point.
Visual Inspection
After a thorough cleaning, the instrument should be care
fully inspected for such defects as poor connections, damaged
parts and improperly seated transistors. The remedy for
most visible defects is obvious; however, if heat-damaged
parts are discovered, determine the cause of overheating
before the damaged parts are replaced; otherwise, the
damage may be repeated.
Transistor Checks
Periodic preventive maintenance checks consisting only
of removing transistors from the instrument and testing them
in a tester are not recommended. The circuits within the
instrument provide the only satisfactory check on transistor
performance.
Defective transistors are usually detected
during recalibration of the instrument.
Performance Checks and Recalibration
To insure accurate measurements, the instrument per
formance should be checked after each 1000 hours of opera
tion or every six months if the instrument is used intermittently.
The calibration procedure is helpful in isolating major troubles
in the instrument or in locating minor troubles which are not
apparent during regular operation. Instructions on how to
conduct a performance check or calibration procedure are
provided in Section 5.
CORRECTIVE MAINTENANCE
Corrective maintenance consists of component replace
ment and instrument repair. Special techniques or proce-
4-1
Содержание 1L40
Страница 30: ...Fig 3 1 Type 1L40 Block Diagram CO K ISO 2 5 0 MHz 75 MHz Circuit Description Type 1L40 ...
Страница 40: ...NOTES ...
Страница 54: ...NOTES ...
Страница 85: ...NOTES ...
Страница 103: ......
Страница 117: ...I ...
Страница 119: ...T Y P E I L 4 0 S F t C T R U M A N A U V t R A ...
Страница 120: ...L R O G 8 R F P H A S E L O C K D I A G R A M A ...
Страница 124: ... 75V T Y P L I L A Q S P f c C T R U M A N A L Y Z t R ...
Страница 126: ... T y p t S P E C T R u M A N A U V 2 f e R A ...
Страница 127: ...4 A P H A S t L O C K C I R C U I T ...
Страница 128: ...iv r AMPUH19 1 rRon J9A 4 T Y P E L 4 0 S P E C T R U M A N A L Y Z C R A I ...
Страница 130: ......
Страница 133: ... IF ATTEW de 1 C 151 LI5I C I52 ci 7 V 185 C 168 FORM A LOW PASS FILTER CHARACTERISTIC I F 1068 ATTENUATOR ...
Страница 134: ... IS MHZ IP lO M Hx OSCILLATOR r T Y P E IL 4 0 SPECTRUM ANALYZED ...
Страница 135: ... lL I z 5 a or lJ ui Ul X i u tt O a i d id u it l h 5 12 2 a or PO S 3 J3 ...
Страница 139: ...DETECTORS i 4 1066 OUTPUT AMPLIPIER ...
Страница 140: ...FIG 1 FRONT REAR TYPE 1L40 SPECTRUM ANALYZER ...
Страница 141: ...FIG 2 IF CHASSIS PHASE LOCK AS 6 1 ...
Страница 142: ...F CHASSIS PHASE LOCK ASSEMBLIES TYPE 1L40 SPECTRUM ANALYZER ...
Страница 145: ......