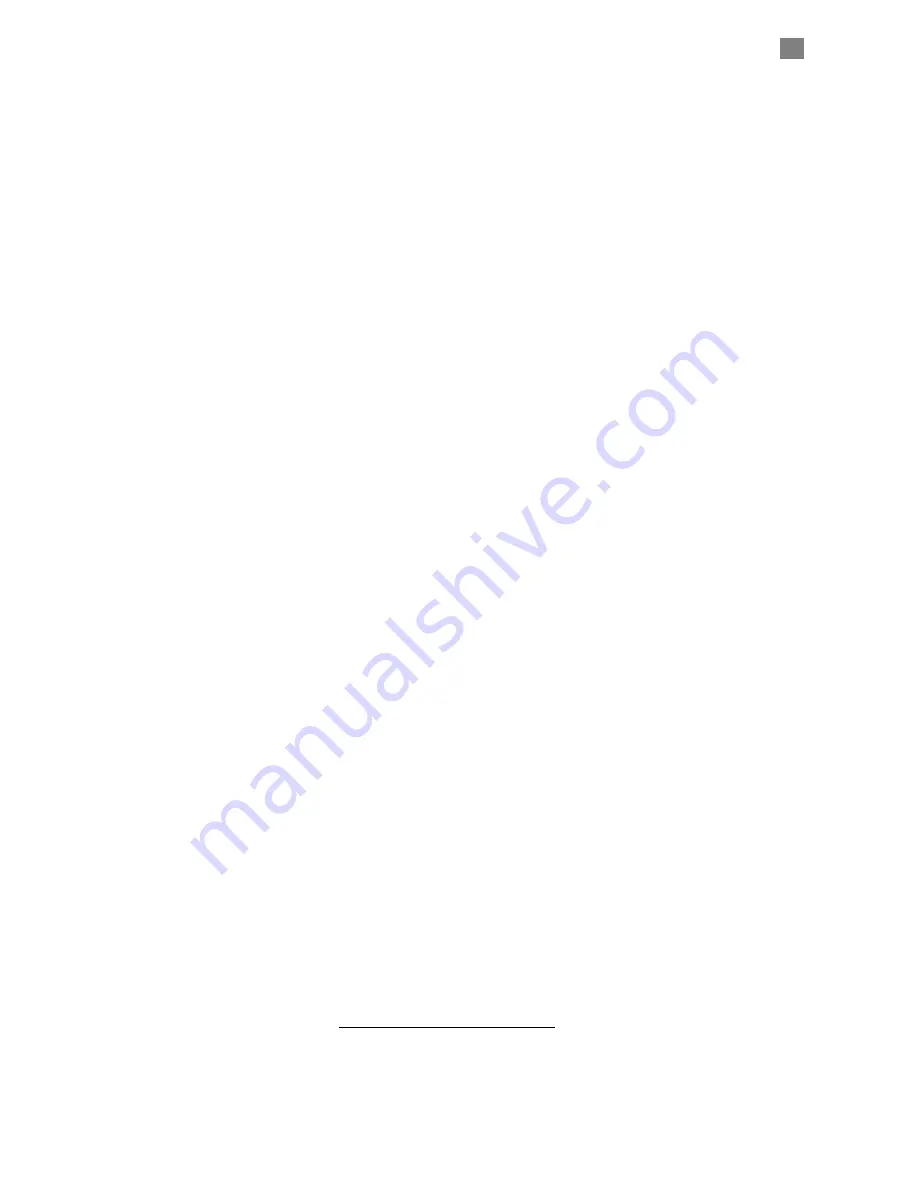
H u d s o n M a n u a l / R e v . 1 . 2 1
1 3
T
EKNIC
,
I
NC
.
P H O N E ( 5 8 5 ) 7 8 4 - 7 4 5 4
During six-step commutation, current flows in only two phases at a time (the
odd phase is always off). Example: In Step #1 above, when the commutation
sensors read binary (1 0 1) the drive sends current through Phases R and S,
while Phase T remains off. Six-step drives are less complicated in several
ways. In fact, because there is only one current path at any time, only one
loop is required to control motor phase current.
It is useful to understand that the commutation “code” changes state six times
per electrical cycle
, and thus provides a less precise fix on rotor position than
a typical sine wave drive with encoder-based commutation. While this may be
sufficient for less demanding motion applications, a high resolution feedback
device—such as an encoder—is a better choice for high precision positioning
tasks.
Pros and Cons of Six-Step Commutation
Pro:
Lower cost of implementation (relatively simple devices)
Con:
High torque ripple
Con:
No torque control loop, though does have a current loop
Con:
Lower torque efficiency (at high speeds)
Sine wave Commutation (Better)
Sine wave commutation is generally better suited to midrange applications
where greater precision of control over position, velocity and/or current is
required.
Most sine wave drives use the commutation sensors to initialize the
commutation process. First, the commutation code is read from the motor to
establish the initial rotor vs. stator position. Then the drive applies current to
the motor windings to achieve the desired relationship between the
permanent and electromagnetic fields. After this relationship is established,
the electromagnetic vector is “locked” to the encoder position, and
commutation continues based on encoder feedback (and not on the Halls).
Though more efficient than six-step drives, sine wave drives run open loop
with respect to torque control. While the current in each motor phase is
individually servo controlled, the actual torque produced at the shaft is not. In
most sine wave drives, torque errors are only corrected indirectly—after they
have resulted in velocity and position errors. This generally means sine wave
drives operate with a wider positioning error band than sine wave drives with
true vector torque control (see next topic).
Sine wave commutation with Vector Torque Control (Best)
Sine wave drives with Vector Torque Control (VTC) are often the drive of
choice for high precision, high throughput positioning and contouring
applications. A sine wave VTC drive is wired, and operates, in basically the
same way as a sine wave drive without VTC. The key difference is how
torque is controlled. While most sine wave drives servo control only the
1 Note: Hudson motors are 8-pole motors that have four electrical cycles per mechanical
revolution. This means that Hudson commutation sensors transition (6 states x 4
electrical cycles) 24 times per motor revolution.