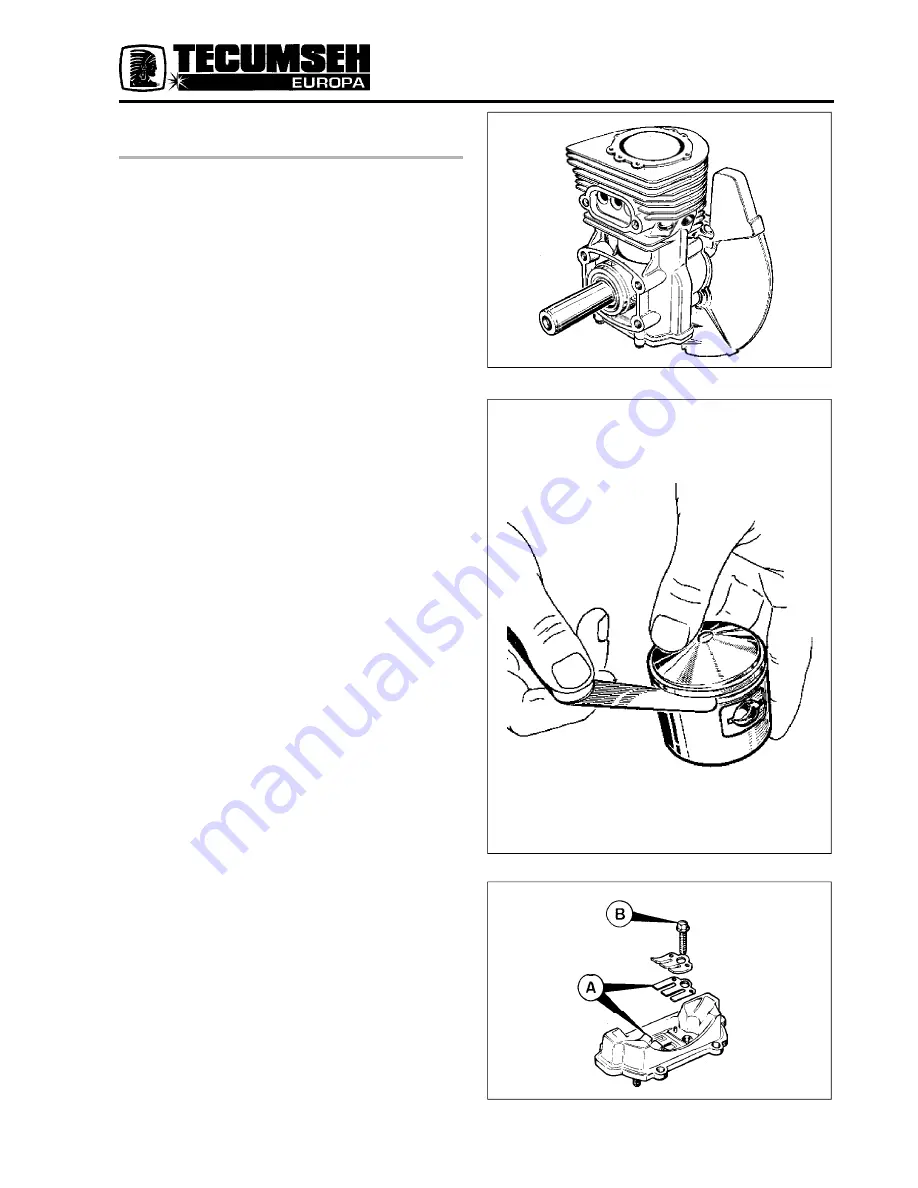
58
I. TWO-STROKE MECHANICAL EN-
GINE PARTS
1. UNIBLOCK ENGINES
(AV520-600-750-125)
a)
INTRODUCTION
Fig. 1 shows the short block.
Fig. 2 shows an exploded view of the engine.
As may be seen the momoblock is compact (combined
crankcase and cylinder) and it is sealed in the upper part
by the shroud mounting base.
b)
EXTERNAL INSPECTION REED PLATE
Fig 3 shows the reed plate. In case of a broken or damaged
reed it is necessary to change the two reeds (
A
) by
removing the two screws (
B
).
NOTE
- Use Loctite or similar for sealing when fitting
the two screws (
B
).
Fig. 1
Fig. 2
Fig. 3
www.mymowerparts.com
For Discount Tecumseh Engine Parts Call 606-678-9623 or 606-561-4983