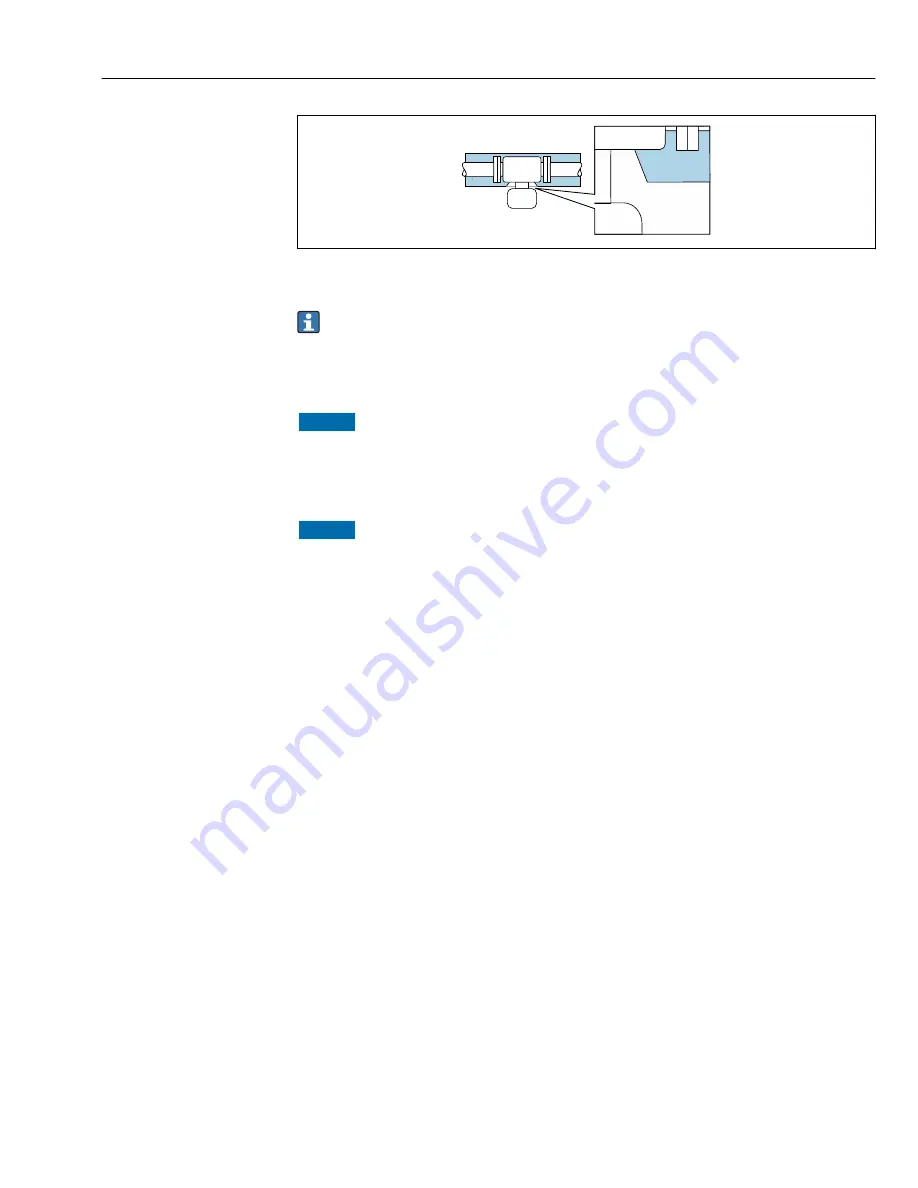
Proline Promass F 500 EtherNet/IP
Installation
29
A0034391
8
Thermal insulation with extended neck free
Low-temperature version: It is generally not necessary to insulate the sensor
connection housing. If insulation is provided, the rules that apply are the same as
those for thermal insulation.
Heating
NOTICE
Electronics can overheat due to elevated ambient temperature!
‣
Observe maximum permitted ambient temperature for the transmitter .
‣
Depending on the fluid temperature, take the device orientation requirements into
account .
NOTICE
Danger of overheating when heating
‣
Ensure that the temperature at the lower end of the transmitter housing does not
exceed 80 °C (176 °F).
‣
Ensure that convection takes place on a sufficiently large scale at the transmitter neck.
‣
Ensure that a sufficiently large area of the housing support remains exposed. The
uncovered part serves as a radiator and protects the electronics from overheating and
excessive cooling.
Heating options
If a fluid requires that no heat loss should occur at the sensor, users can avail of the
following heating options:
• Electrical heating, e.g. with electric band heaters
• Via pipes carrying hot water or steam
• Via heating jackets
Using an electrical trace heating system
If heating is regulated via phase angle control or pulse packages, magnetic fields can affect
the measured values (= for values that are greater than the values permitted by the EN
standard (sine 30 A/m)).
For this reason, the sensor must be magnetically shielded: the housing can be shielded
with tin plates or electric sheets without a privileged direction (e.g. V330-35A).
The sheet must have the following properties:
• Relative magnetic permeability µr ≥ 300
• Plate thickness d ≥ 0.35 mm (d ≥ 0.014 in)
Vibrations
The high oscillation frequency of the measuring tubes ensures that the correct operation of
the measuring system is not influenced by plant vibrations.