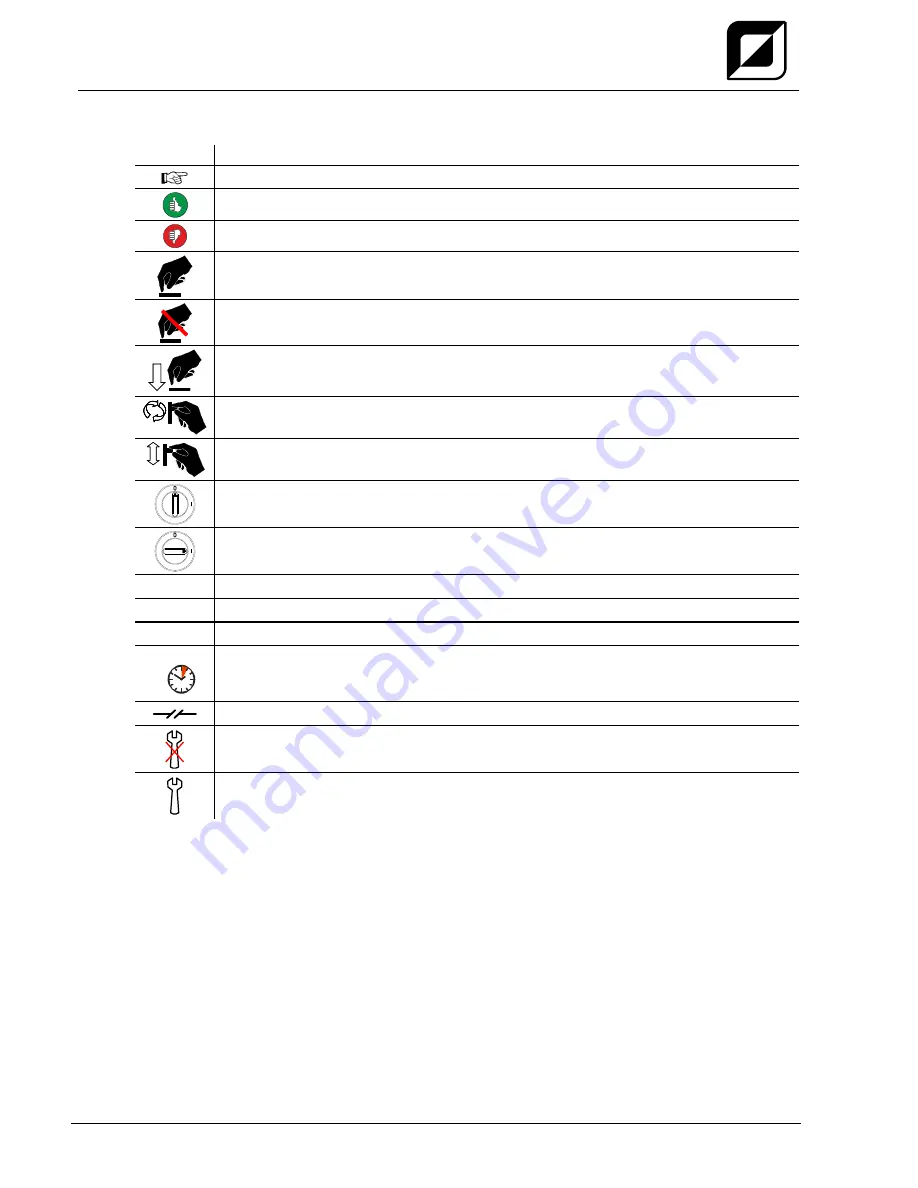
Safety instructions
Explanation of icons
6
299-030500-TWD01
25.09.2015
2.2
Explanation of icons
Symbol
Description
Special technical points which users must observe.
Correct
Wrong
Press
Do not press
Press and keep pressed
Turn
Switch
Switch off machine
Switch on machine
ENTER
enter the menu
NAVIGATION
Navigating in the menu
EXIT
Exit the menu
4 s
Time display (example: wait 4s/press)
Interruption in the menu display (other setting options possible)
Tool not required/do not use
Tool required/use