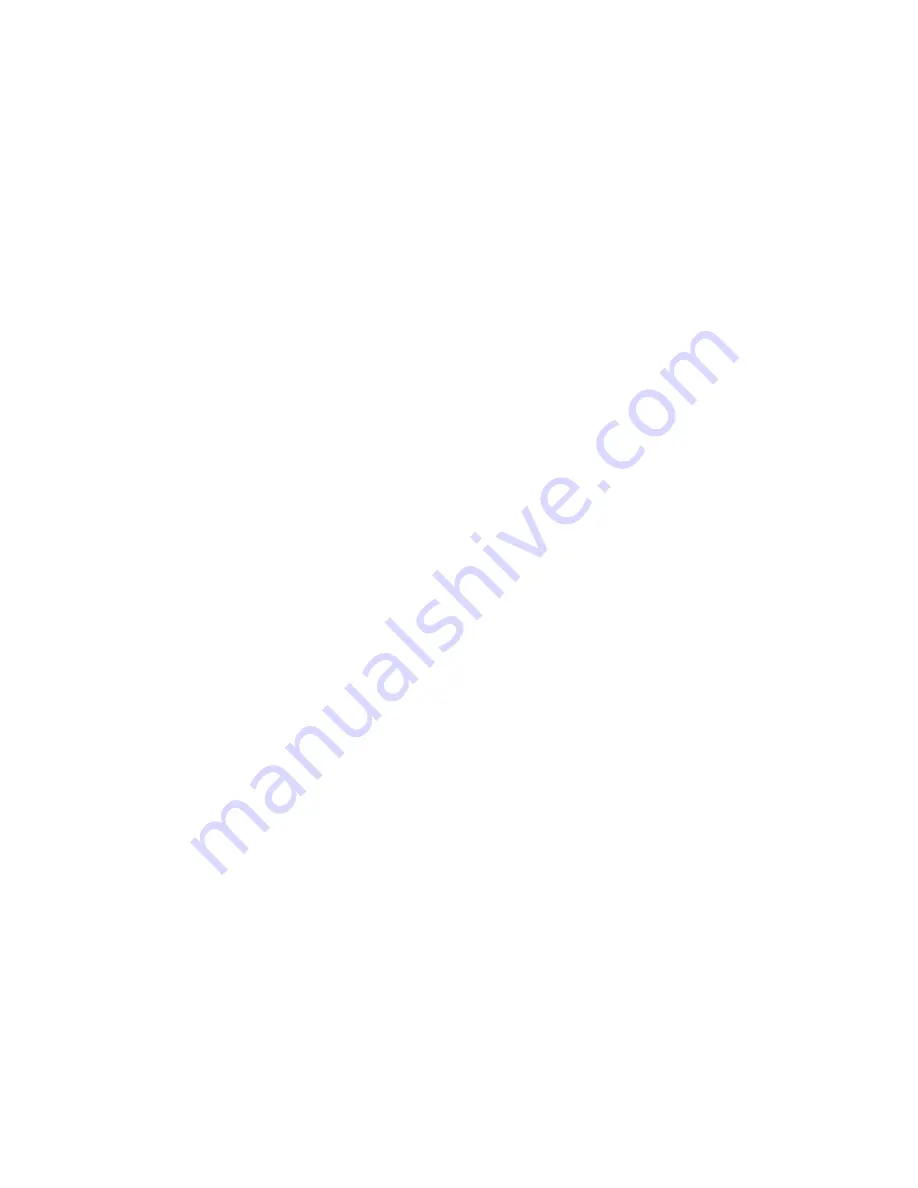
1 Operation
The SC82 is capable of driving eight servo motors. Each output (servo) can individually be assigned any switch (turnout)
address. It has eight inputs for local control of the outputs and eight programmable routes.
There are two modes of operation. The modes are based on how the servo is used. All servo outputs function in either mode 1
or 2 i.e. modes can not be mixed between servo outputs.
The first mode is moving all servos to two positions (default).
Mode 1
- The servo outputs can be used for switch (turnout) control. There is a separate switch address for each output so
they can be controlled individually. There are a total of eight switch addresses used.
The second mode is for moving all servos to three positions.
Mode 2
- The servo outputs can be used for semaphore control. There are 24 switch addresses used. In this mode three
addresses are used to control each servo, address A(throw) will command the servo to one end, address A+1(throw) will
command it to the center and address A+2(throw) will command it to the other end.
The SC82 supports routes. A route allows for the control of multiple switches (turnouts) with just one switch command. Each
route is made up of eight cells (switch addresses) and one top level address (or route execution switch address). Each top
address is completely independent of a servo address. Complex routes with more than eight servo addresses can be created by
assigning the same address to more than one top level address. Routes are executed by issuing a switch command.
Since the SC82 is an accessory decoder, it can be controlled via DCC commands. It can also be controlled via the serial bus
(LocoNet
®
compatible). For non-Digitrax systems a DCC gateway feature allows DCC switch commands to be passed
directly to the serial bus. This allows DCC switch commands to control devices connected to this serial bus.
1.1 LED Indicators
LED 1 flashes indicates “Smart” programming. LED 2 flash indicates accepted program value or a valid received address.
LED 3 slow flash indicates heartbeat and fast flash indicates serial bus short.
2 Getting Started
The SC82 comes from the factory ready to use with addresses of 1 to 8. Once you plug in the servos cables, centered the
servos (section 2.2) and mounted them you are ready to use the SC82. If you want to change some of the addresses or adjust
servo movement see the “Smart” Programming section. For very custom programming see section 4, Configuration Variables
for various options.
Before doing any programming, it is strongly recommended that you verify basic operation.
2.1 Control via LocoNet - Digitrax Users
The SC82 comes from the factory ready to use by control from DCC commands when it is connected to track power. To
control the SC82 via LocoNet
®
, it must be enabled. LocoNet
®
can be enabled using section 3, “Smart” programming Part 3 or
the programming track. If the programming track is used, connect the SC82 track power terminals to the programming track
and program CV9 with a value of 48. The SC82 can now be powered from a 12 volt supply and controlled via LocoNet
®
.
2.2 Servo Mounting
Before mounting and/or linking the servo arm (horn) to the turnout or semaphore, the servo should be centered and then the
arm attached so that when linked the turnout or semaphore will be in the approximate center of their travel.
To center the servo, press the Smart button then turn on power and continue to press the button until LED2 (green) begins to
flicker. Several seconds after releasing the button, all the servo will move to the center position.
NOTE: for mounting orientation it may be useful to know that a turnout throw command causes the servo to rotates CCW
when viewing the servo shaft (factory default operation).
2.3 Servo Move Direction
It may be that after you have installed the servos issuing a close or throw command causes the switch to move to the opposite
intended position. That is, close causes the switch to move to the thrown position. The direction can be reversed without
programming if a push button is used for switch control. To reverse the servo direction press and hold the “Smart” program
button until after power is turned on. If LED2 (green) begins to flicker you have pressed the “Smart” button too long. After
power has been on for at least 5 seconds, press and hold the respective push button for the servo to be reversed for at least 4
seconds. Direction can also be changed in “Smart” programming Part 2.
2.4 Switch Position Indication
If LEDs are used to indicate the status (position) of the switch on a panel or facia, they will flash during the time the
respective servo is moving. It may be that after they are installed that the lighted color does not match the switch position.
That is, green may be lit instead of red. The lighted color can be reversed without programming if a push button is used for
switch control. To reverse the lighted color during normal operation, press and hold the push button for at least 4 seconds.
3