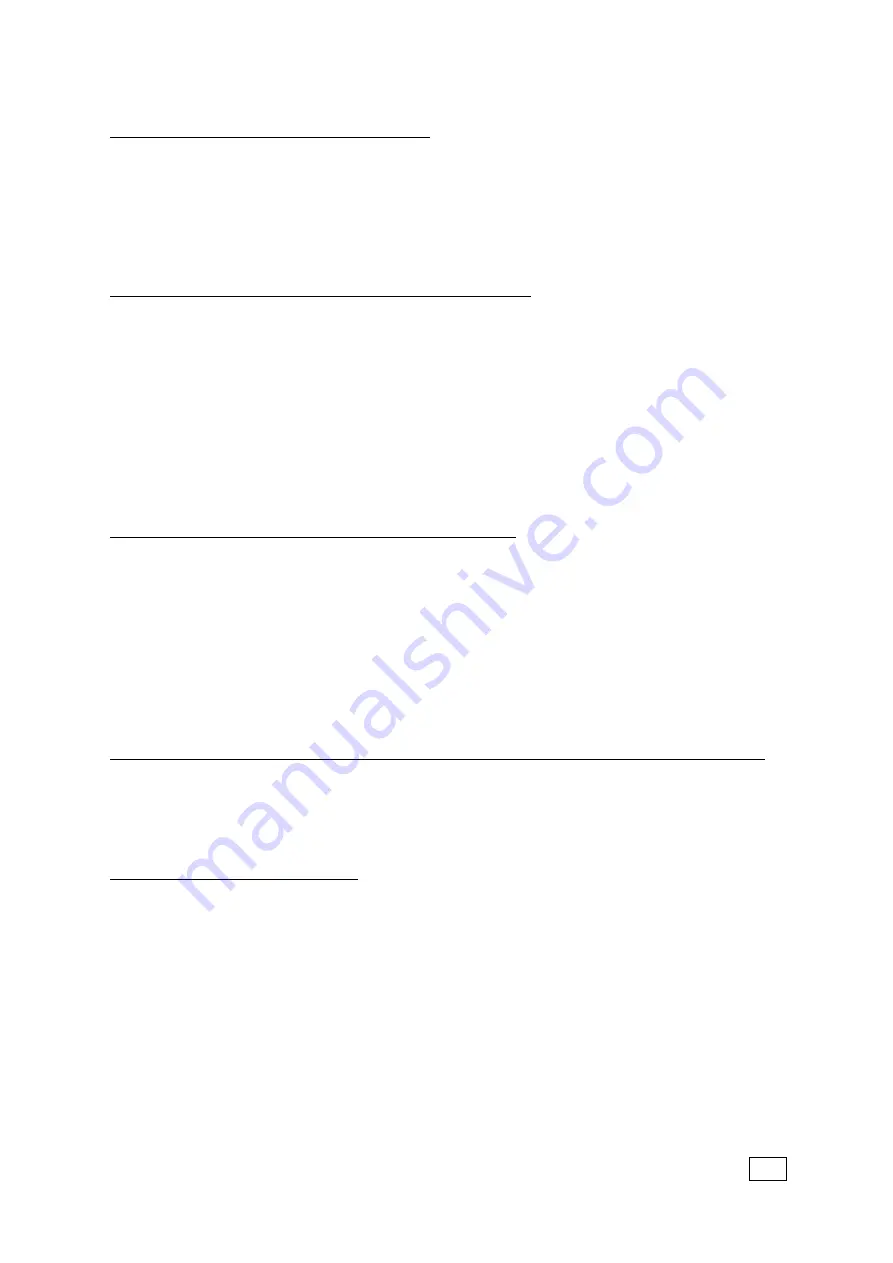
V
-
21A
STUDWELDING TECHNIQUES
19
The operating instructions given previously in this guide apply to the majority of general
applications where it is possible to use the pistol in the down hand position and with
standard cable lengths. For many applications these conditions do not apply and the
following notes will give some guidance as to the methods used to obtain satisfactory
results for a variety of applications.
1. WELDING TO A PLATE IN THE HORIZONTAL POSITION.
In this position there is a tendency for the weld metal to run to the underside of the stud
during welding, due to the action of gravity, resulting in an uneven fillet. The effect is
more noticeable as stud diameter increases and generally speaking it is not recommended
that studs of 12 mm diameter and over be welded to vertical plates for this reason. The
essential requirement to obtain satisfactory fillet formation is to use the shortest weld time
possible with increased welding current. Welding to a vertical surface reduces the
maximum size of the stud a given power source will weld.
It must be remembered, that greater care is required to ensure that the stud is
perpendicular to the work piece. A special tripod foot attachment can be supplied if
required. Take particular care to keep the ferrule grip, foot adapter and chuck clean.
2. WELDING TO A PLATE IN THE OVERHEAD POSITION.
IMPORTANT ! You must protect your face and shoulders with a helmet and cape before
carrying out overhead welding operations. Weld spatter can do a lot of damage !
Firstly, obtain satisfactory weld settings in the down hand position before making attempts
in the overhead position. Since the weld metal is transferred from stud to plate in small
particles in the down hand position, it follows that, when welding overhead, the transfer
takes place against gravity. As with vertical welding the best results will be achieved using
the shortest possible weld time with increased welding current.
It is important that the ferrule grip, foot adapter and chuck are kept free from spatter build
up as this can cause stud return problems or possibly short out/bridge out the weld.
3. PISTOL ADJUSTMENTS WHEN WELDING IN THE VERTICAL OR OVERHEAD POSITIONS.
Problems may be encountered when welding in the vertical or overhead positions with a
damped pistol. To prevent problems occurring, where it is possible to do so, the damping
effect should be removed or turned off.
Welding can then continue as outlined in sections 1. and 2.
4. USING LONG CABLE LENGTHS.
Frequently the pistol must be used some distance from the nearest available mains
supply, for instance on board ship, in power stations and building construction, in
workshops building large pre-fabricated structures etc. In these cases long lengths of
welding cable are used and it must be realised at the outset that, the longer the cables the
smaller the maximum diameter of stud which can be welded with a given power source.
To help get over this problem, if larger diameter studs are to be welded with long lengths
of cable, increase the welding cable conductor size.
Try to avoid running the pistol cables and the earth cables alongside each other as this can
cause a choking effect, reducing power. Also avoid coiling any excess cable as this will
have the same effect.