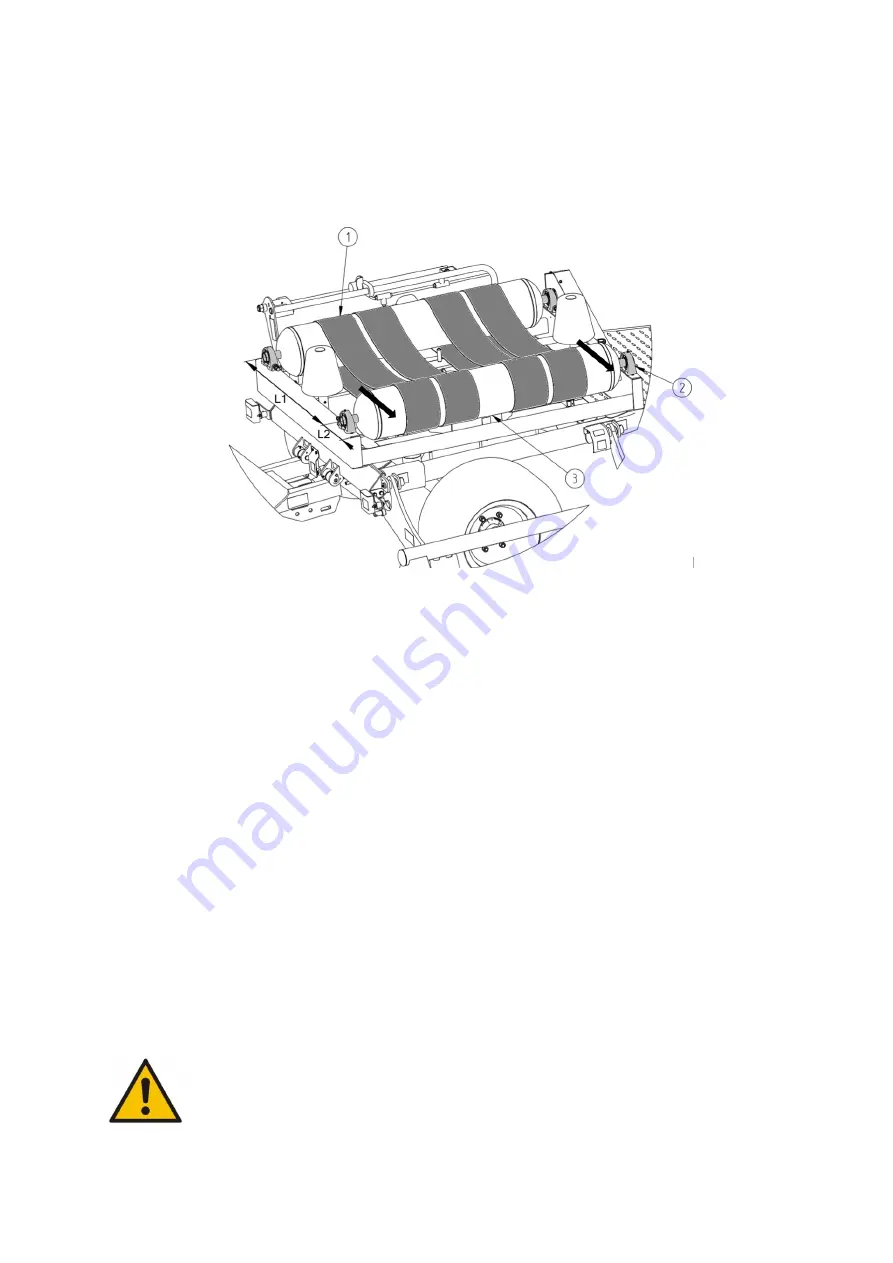
Page
53
of
129
SELF-LOADING BALE WRAPPER
SPRINTER 1500
7.4
Adjusting the tension of the belts
The belts (1) are subject to stretch in the course of the bale wrapper's use. When their lower position is
visibly evident, you must adjust the tension.
Figure 37 Adjusting the tension of the belts
(1) belts, (2) bearings, (3) idle table roller, (L1) distance between table rollers, (L2) distance between the
roller centreline and frame edge
Follow the procedure for tensioning the belts:
1.
Loosen the bearing nuts (2) which lock the idle table roller (size 21 wrench).
2.
Move the bearings of the idle table roller outwards, as per the arrows (size 19 wrench).
3.
Tighten the bearings which hold the roller in place.
4.
Check the L1 distance on both sides of the table rollers.
5.
Check the L2 distance on both sides of the table rollers.
If the distances L1 and L2 on both sides are equal, this means that the table rollers are
positioned correctly, i.e. parallel to each other, which extends the life of the belts.
If the distances L1 and L2 are different, the bearing position must be readjusted.
6.
The adjustment of the driving table roller must be carried out in the same way, considering the
chain tension (see Section 7.2).
CAUTION
If the stretch of the belts is greater than the adjustment range, the belts must be replaced.
All repairs, adjustments and maintenance works must be carried out when the machine is
stationary and secured.
Содержание SPRINTER 1500
Страница 16: ...Page 16 of 129 SELF LOADING BALE WRAPPER SPRINTER 1500 Figure 3 Signs on the machine ...
Страница 17: ...Page 17 of 129 SELF LOADING BALE WRAPPER SPRINTER 1500 Figure 4 Signs on the machine ...
Страница 89: ...89 12 1 General design ...
Страница 91: ...91 12 2 Bottom frame set ...
Страница 101: ...101 12 11 Turntable slide base set ...
Страница 105: ...105 12 14 Rotary frame set ...
Страница 122: ...122 12 28 Hydraulic system ...