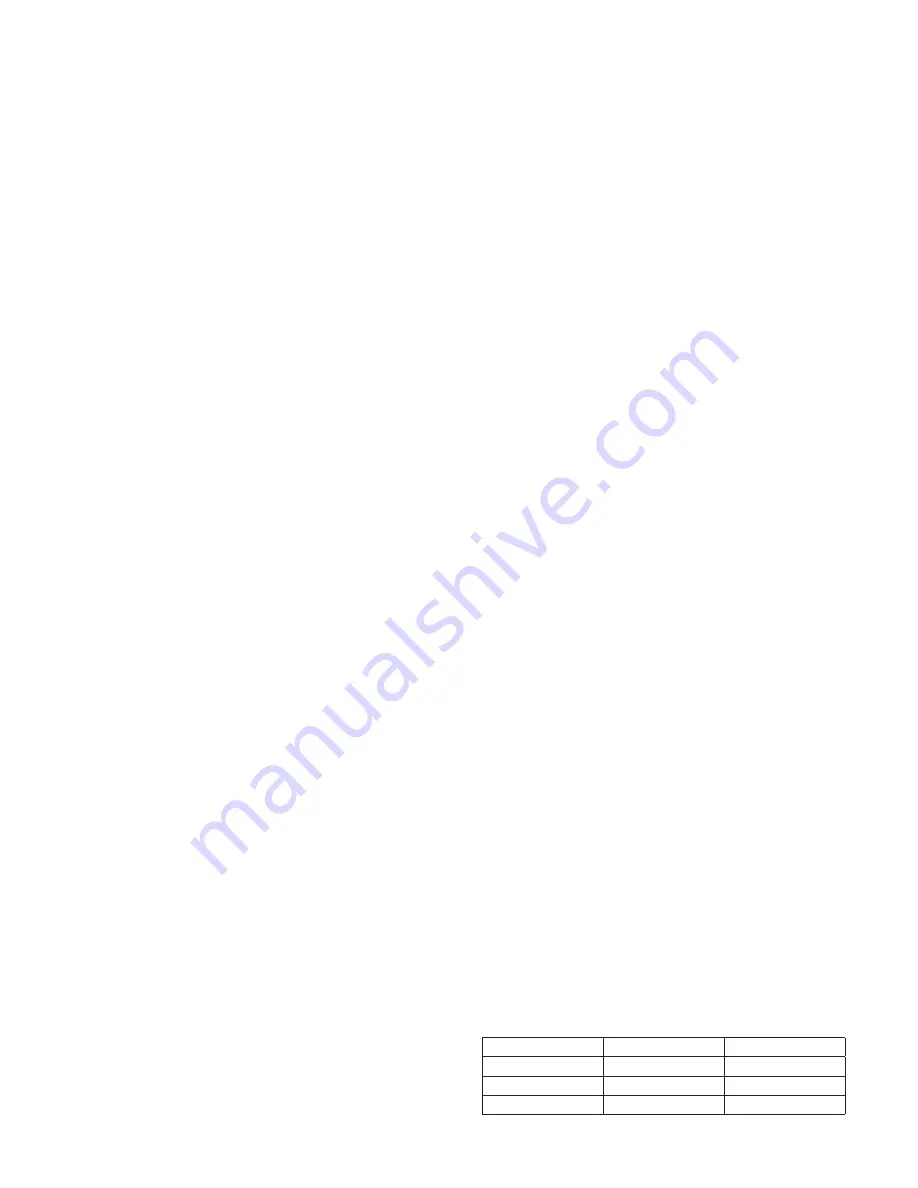
4
2.a Inspect the seal assembly to be sure O-rings are included
on the seal housing cover and the shaft sleeve. On the lock
ring, be sure the lower set screws are tight and upper set
screws are loose. See Figure A5.5.
2.b Prior to installing the shaft sleeve o-ring, lubricate with light
grease then slide complete assembly over head shaft. Seat
and bolt down the assembly against the seal housing, taking
care to be sure that the O-ring of the seal housing cover is in
its groove.
2.c To set seal, first set impeller lateral, then tighten top set of set
screws of the lock ring. Remove paper spacers and keep for
future use.
A5.6: VERTICAL MOTORS
1. Hollow Shaft Motor
1.a Clean threads and face of head shaft projecting above pack-
ing gland thoroughly, then oil threads lightly. Thread coupling
on shaft for half of its length. Stuff a rag into open end of the
shaft coupling.
1.b Remove the top cover from the motor. Unbolt the coupling
(clutch or drive block) from the motor and remove the coupling.
1.c Run a fine flat file over the motor mounting surface of the
head to remove any nicks or burrs. Thoroughly clean face
and register with solvent. Wipe a thin layer of light oil over
the surface. This will help prevent rust and will also facilitate
slight driver shifting during coupling alignment.
1.d Attach the erector sling to the motor lifting lugs. Hoist motor
sufficiently to allow easy access to mounting flange. Remove
nicks and burrs on the mounting flange with a fine flat file and
thoroughly clean with solvent.
1.e If there is sufficient head room to install the head shaft after
placing the motor on the discharge head, prepare the shaft
as described in Step 1.g below, then lower the head shaft
through the motor with the keyway end up. Install the adjust-
ing nut and thread it on 4 or 5 threads, then allow the shaft to
suspend inside the motor.
1.f Hoist motor sufficiently to clear the stand and swing it over
until motor is resting on mounting ring. Properly place conduit
box, align mounting holes and install, but do not tighten cap
screws.
1.g Clean the head shaft thoroughly and dress the threads and
keyway with a 3-cornered file, if necessary. Lift the head shaft
and carefully lower it through the quill or hollow shaft (end
with keyway goes toward the top) and allow shaft to contact
head coupling. Remove the rag in the coupling. Screw the
head shaft into the motor coupling on the head shaft and
tighten.
1.h Make temporary electrical connection to motor, bump starter
to determine correct rotation (counter clockwise as viewed
from above). Install and tighten cap screws to the motor and
discharge head/motor stand. If power is not available, DO
NOT make final drive shaft connections (Steps 1.i and 1.j)
until power is available and correct rotation is determined.
1.i Slide clutch over head shaft, seat against drive plate, install
and tighten bolts.
1.j IMPELLER ADJUSTMENTS: Turn clutch until keyways in
shaft and clutch align; install and seat gib key. Thread head
adjusting nut onto head shaft until it seats against top of the
clutch. Hold the clutch to keep from turning and turn head nut
until the impellers clear the bottom allowing the rotor to turn
freely. Continue to tighten head nut until impellers are elevated
a sufficient distance (about 1
1
⁄
2
turns) to accommodate pump
hydraulic thrust and associated shaft stretch. Align holes
in head nut with taps in clutch, install and tighten machine
screws. Place top cover on driver and secure.
2. Solid Shaft Motor
2.a Slide the pump hub of the adjustable motor coupling onto the
head shaft and insert the key. Screw the adjuster nut onto the
head shaft.
2.b Attach the erector sling to the motor lifting lugs. Hoist motor
sufficiently to allow easy access to mounting flange. Remove
nicks and burrs on the mounting flange with a fine flat file and
thoroughly clean with solvent.
2.c While the motor is suspended from the erector sling, slide the
motor hub of the adjustable motor coupling onto the motor
shaft. Insert the key into the keyway of the motor hub far
enough up the motor shaft to expose the keeper key seat on
the shaft. Seat the keeper key onto the motor shaft. Pull the
motor hub down over the keeper key.
2.d Bolt the spacer to the motor hub, if applicable.
2.e Hoist motor sufficiently to clear the stand and lower it until the
motor is resting on the discharge head. Properly place the
conduit box, align mounting holes and install cap screws.
2.f IMPELLER ADJUSTMENT: Adjust the adjuster nut until the
clearance between the spacer/adjuster nut and the motor
hub is equal to the impeller adjustment as stated in Section
A5.6, 1.j. Add additional clearance to the above adjustments
to accommodate pump hydraulic thrust and the associated
shaft stretch.
2.g Make temporary electrical connections to motor, bump starter
to determine correct rotation (counter clockwise when viewed
from above). If power is not available, DO NOT make final
drive shaft connections (Step 2.h) until power is avail-
able and correct rotation is determined.
2.h Align holes and taps of the motor hub, pump hub, adjuster
nut, and spacer (if applicable). Install and tighten cap screws.
A5.7: MISCELLANEOUS ASSEMBLIES
1. Discharge Piping
1.a Above and below floor piping should be installed in such a
manner as to eliminate the possibility of the discharge head
being strained. Gate valves, check valves, and other piping
items must not depend upon the pump head for support.
1.b If a flexible joint, such as a dresser coupling, is to be used,
the tie bolts and lugs used to span the flexible joint should
be of sufficient strength to resist the force created by the
discharge pressure at the pump head. None of this force
should be imposed on the head or the foundation bolts. The
tension should be taken carefully on these tie bolts so that
any amount of forward movement induced to the head will
be counteracted during operation so that alignment is main-
tained throughout the operation.
2. Air Release Valve
Install the air release valve on the pump head or just beyond
on the discharge piping. It is suggested that if a throttling valve is
not furnished, a throttling device be used to restrict the discharge
of air to insure that a cushion of air is available in the discharge
head. Placement of the throttling device should be such that the
air release valve is between the discharge head and throttling
valve. Note: Exhausting the air from a head too quickly often
causes breakage.
3. Gauges and Miscellaneous Pipe Connections
PRESSURE
“L” PORT
“U” PORT
0-100 PSI
Grease
Grease
100-300 PSI
Grease
Grease
300-450 PSI
Bypass
Grease