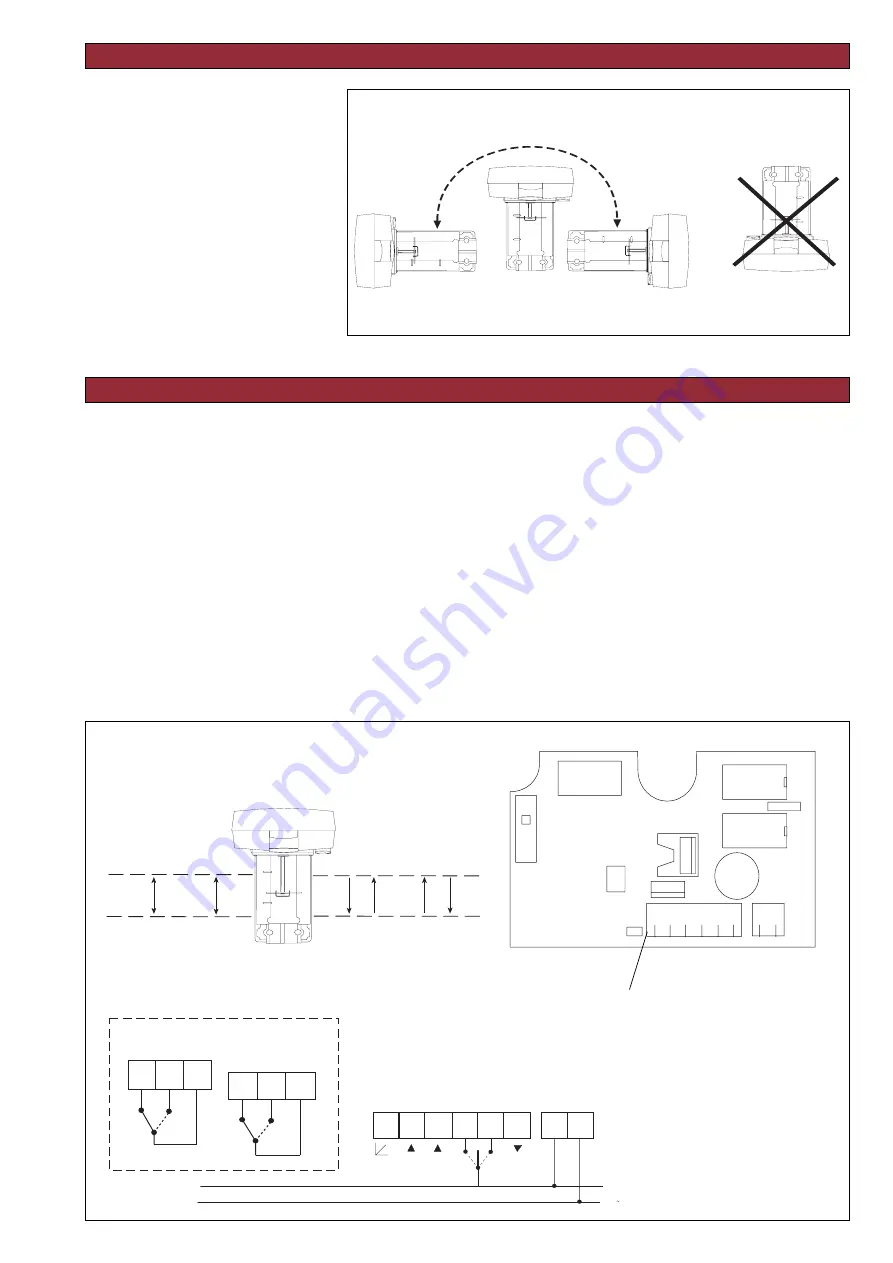
3 (6)
0-003-2060-1 (EN)
The actuator may be mounted
horizontally, vertically and in any
position in between, but not upside
down, see figure 3.
N.B.! Do not use the actuator for the
DN15 valves V298, V282, V294, V384,
V386 and V394.
To mount the actuator on a valve, slide
the actuator onto the valve neck, thus
making the square nut on the valve
spindle fit into the groove on the cross
bar. Then slide the brace into the
groove on the valve neck and secure
the nuts.
MOUNTING
CONNECTIONS
N.B.! When installed with 3
conductors, where the control signal
reference is connected to G0, the motor
current of the actuator will cause
varying voltage loss in the cable and
thus in the reference level. Forta, which
has a highly sensitive control signal
input, will detect the varying signal and
follow it, which makes it difficult for the
actuator to find a stable position.
This variation may be accepted in
simplified installations on the following
conditions: the cables between the
controller and actuator
are shorter than 100 m (328 ft.), the
cross-sectional area is larger than
1,5 mm2 (AWG 16) and the cables are
only connected to one actuator. Please
refer to the figures labelled “Simplified
installation” for wiring instructions.
Cable lengths
The cables to G, G0 and G1 should be
max. 100 m (328 ft.) and have a cross-
sectional area of min. 1,5 mm² (AWG
16).
Other cables should be max. 200 m
(656 ft.) and have a cross-sectional
area of min. 0,5 mm² (AWG 20).
Block Function
Description
G
24 V AC
Supply
G0
24 V AC rtrn
voltage
X1
Input
Control sign-
MX
Input, neutral
als (VH, VC
VH
Increase
short-circuited
VC
Decrease
to G0)
G1
16 V DC
Supply for RC
Y
0–100 %
Feedback
signal
}
}
2V
10V
NORM
VH
VC y
10V
2V
VH
VC y
10V
X1
10V
y
INV
NORM
X1
10V
0(2)V
10V
y
INV
2V
0(2)V
2V
Y X1 MX VH VC G1
1
2
3
4
5
6
7
8
G0 G
Terminal
block
Y X1 MX VH VC G1
G0 G
Forta P
24 V
0 V
K1 K2 KC1
CLOSING RELAY
OPENING RELAY
S2
Ej endläge Non ending position
Endläge Ending position
KC2
K3 K4
Ej endläge Non ending position
Endläge Ending position
Figure 3
Figure 4