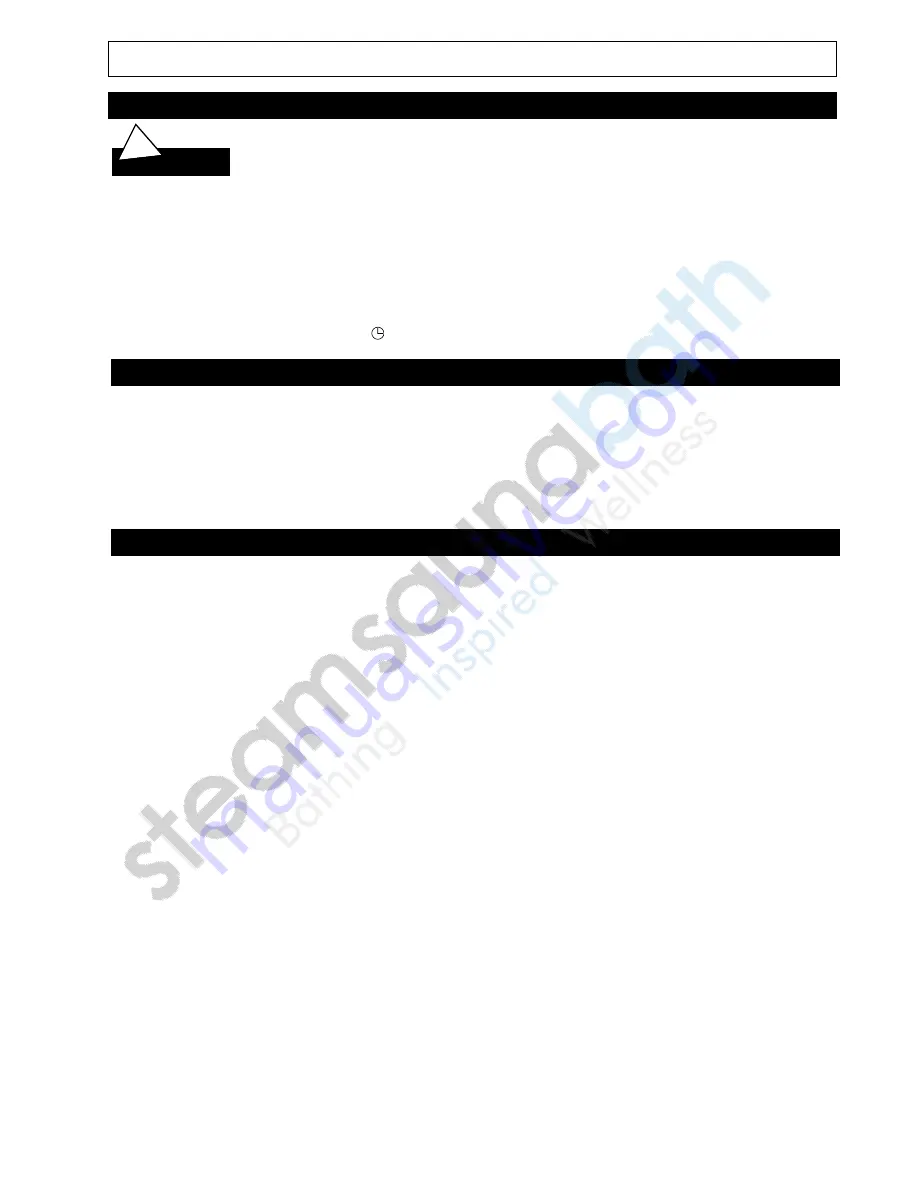
Mr
S
team CU Series
Installation, Operating & Maintenance Manual
Automatic Blowdown Operation and Testing
21
Burn Hazard. Pressurized Steam and Hot Water is discharged during blowdown.
1.
Turn the override switch to permanent ON (I).
2.
Turn the generator On/Off Switch to “ON”. On/Off Switch pilot light and generator should be “ON”. Motorized
drain valve should be closed. Autoblowdown light should be “OFF”.
3.
Turn the override switch to permanent OFF (0). On/Off Switch pilot light and generator should be “OFF”.
Autoblowdown light should be “ON” Motorized drain valve remains open for approximately 10 seconds.
4.
After10 seconds: Motorized drain valve closes. Autoblowdown light should be “OFF”. On/Off Switch pilot light and
generator remains “OFF”.
5.
Turn the override switch to automatic ( ).
1.
1. Set the F1 Plus thermostat knob to 100°F. Turn “ON” the CU steam generator.
2.
CU generator will heat up and produce steam in a few minutes then stop when steamroom temperature reaches
100˚F.
3
. Slowly turn the F1 Plus thermostat knob higher. The steam solenoid valve should open and allow steam to fill the
steamroom again.
4.
Turn the thermostat knob lower. Steam should stop.
5.
Set the F1 Plus thermostat to 100˚F or desired setting.
1.
Set the thermostat knob of CU-HL to max 130°F or to the temperature permitted by jurisdiction. Turn on the CU
steam generator.
2.
Slowly turn the thermostat knob of CU-HL lower. The CU steam generator should shut off at about the current
room temperature.
3.
Turn the thermostat knob of CU-HL back to max 130°F or to the temperature permitted by jurisdiction.
The CU steam generator should turn back on.
NOTE: The operating room temperature setting is determined by the owner/operator of
the facility. For guidance, refer to ASCM guidelines or equal reference.
!
WARNING
F1 Plus Control Operation Testing
CU-HL Operation and Testing