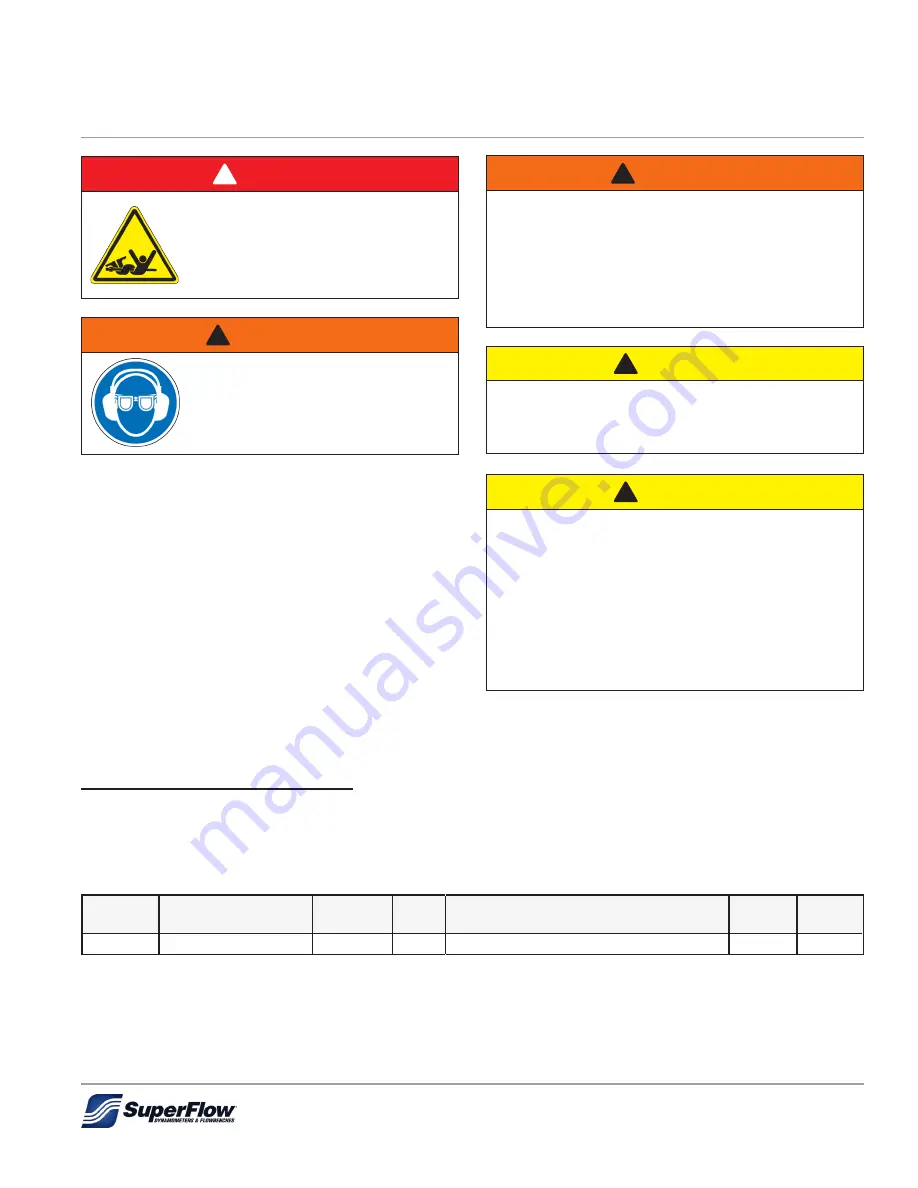
15
5.0 Operation
DO NOT remove any safety guards
while the machine is in operation,
and be sure the safety guards are
correctly mounted before operating
the device.
!
DANGER
WEAR
EYE
and
HEARING
PROTECTION. Proper eye and
hearing protection should be worn
at all times when the equipment is
operating.
!
WARNING
5.1 Modbus Operational Examples
The SF-1020i flowbench has been designed
to network with, and be controlled by various
consumer automation systems. The flowbench
uses an industrial grade programmable logic
controller (PLC) connection to control the internal
components by utilizing a Modbus TCP/IP network
via the PLC. This option allows customers to
connect the flowbench controller directly to their
automated control systems Modbus TCP/IP
network, which facilitates flowbench control and the
exchange of data. Superflow does offer optional
control packages. Please contact your sales representative for more information.
5.1.1 Setting the Servo Mode
The SF-1020i is capable of controlling the airflow to either
test pressure
or
flow rate
. In test pressure
mode, the air pressure is set and the flow rate measured. In flow rate mode, the airflow is set and the test
pressure measured.
Servo Mode Register
Register
Function
Data Type
Read/
Write
Value
Units
Scale
40002
Servo_Mode
Int-16
R/W
0 = Test pressure mode 1 = Flow rate mode
Register
40002 Servo_Mode
provides the status (state) that the flowbench is currently in when read.
It also allows for the ability to change (set) states when this register receives commands. The following
commands are accepted:
0
= Test Pressure Mode
1
= Flow Rate Mode
•
Keep the air ducts free of dust or dirt.
•
Keep loose material away from the inlet and
exhaust ducts.
!
CAUTION
•
Inspect the equipment monthly to ensure that
there are no broken or worn parts which could
cause injury to personnel or damage to the
equipment.
•
Only qualified operators and maintenance
personnel should perform the procedures
covered in this manual.
!
WARNING
Follow this warm-up procedure if the flowbench
has been static for more than 2 consecutive weeks
without being ran;
•
Set Flow Rate to 10 cfm.
• Set Range to 3.
•
With daily reference plate installed run
flowbench for 3 minutes.
This is done to avoid bearing damage, ensuring
grease is spread evenly throughout the bearings.
!
CAUTION