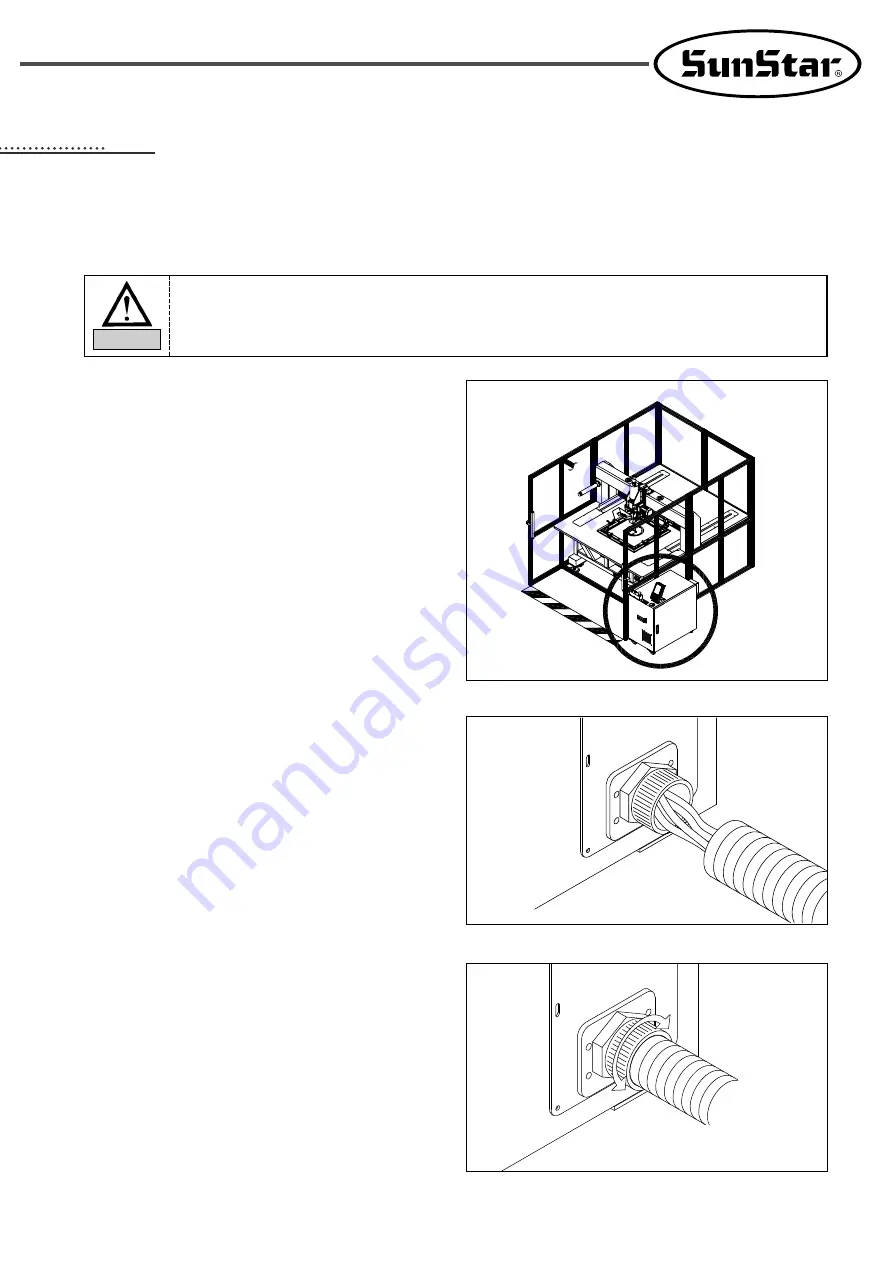
19
66
AMP Box Installation
1) AMP box installation
[ Fig. 11 ]
Please unplug during the installation of AMP box.
Plastic connector can be damaged when connecting cable, so please proceed with caution.
Please lock the cover after installing AMP box not to open it arbitrarily.
Caution
A. AMP box is on the front right side of the sewing machine.
⇒
Follow the instructions below to connect cables from the
machine and fix the AMP box.
[ Fig. 12 ]
B. Insert sewing machine connection cable into the cable
entrance at the back of the AMP box.
⇒
To turn the handle of the cable holder when inserting
cable, the cable tube can be inserted easily. [See Pic. 13]
⇒
Plastic connector can be damaged when connecting
cable, so please proceed with caution.
[ Fig. 13 ]
C. Please fix the cable tube by turning the handle of the cable
holder after inserting cable.