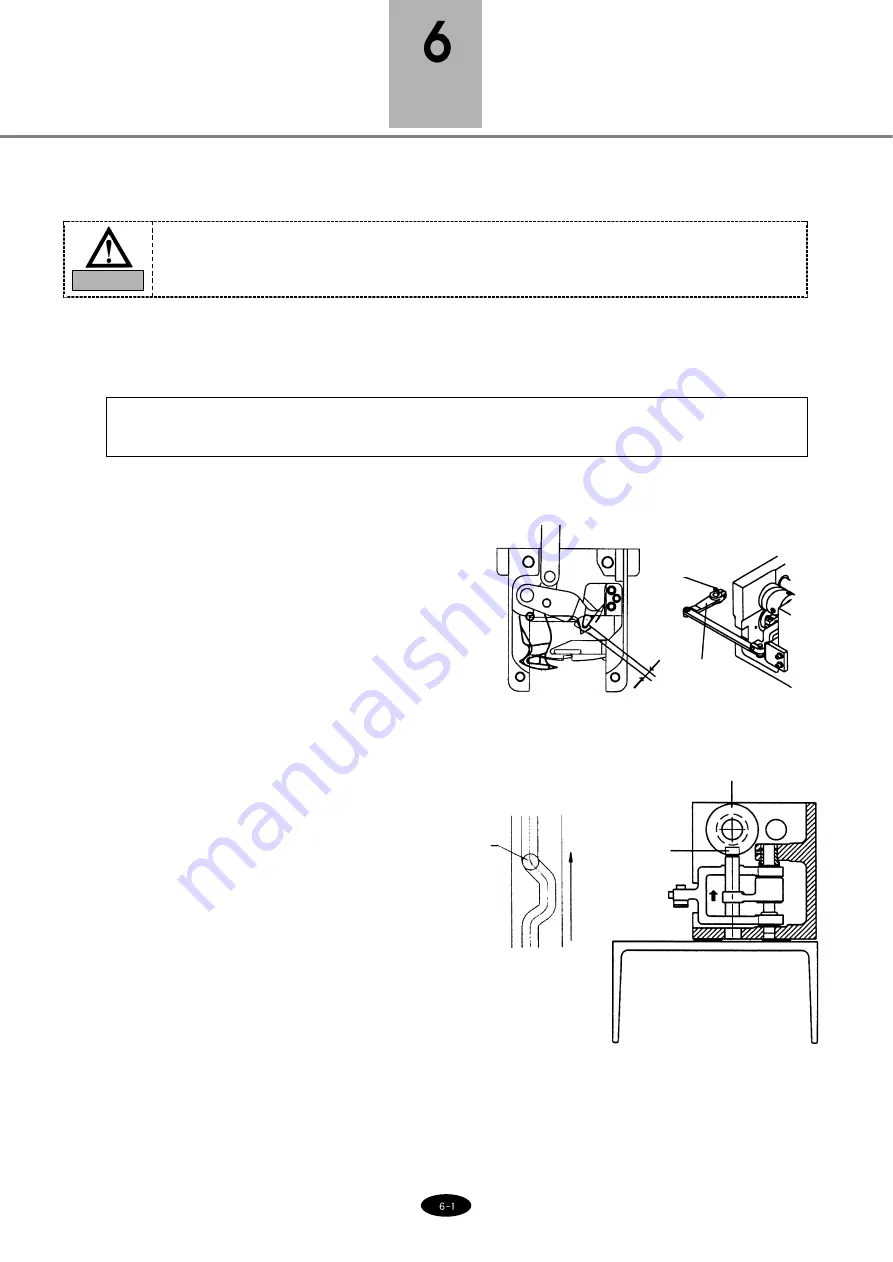
6-1) ADJUSTING THE TRIMMERS
6-1-1) Adjusting the Position of the Trimming Cam (Insert Angle of Movable Blade)
The movable blade is started by the trimmer cam in the angle it is inserted. As one of the basic trimming
functions, it arranges the upper thread tails in the needle after trimming.
1) Adjusting the position of the movable blade
①
Check if the movable blade is in the correct
position.
②
Cutting point of the movable blade should be
inserted 1mm at the end of the fixed blade. Incorrect
position of the movable blade can cause trimming
errors or deviation of the upper thread.
③
Unfasten the crank screw to adjust the location of
the movable blade (see [Fig.6-1]).
2) Adjusting the angle of the movable blade
①
Unfasten two screws on the blade cam. Adjust the
upper shaft rotary angle at 290°.
②
Insert the trimming cam roller into the trimming
cam. Turn the cam and when the roller aligns with
the curve of the cam, fasten the two screws back.
③
Run the manual handle and check if the movable
blade is well-inserted at 290°. Always check after
the adjustment.
[Fig.6-1]
WARNING
Turn OFF the main power when adjusting the machine.
MAJOR MACHINE ADJUSTMENTS
App.
1mm
Screw
Trimming
drive crank
Blade cam
Roller
Roller
Direction
of cam
movement
[Fig.6-2]