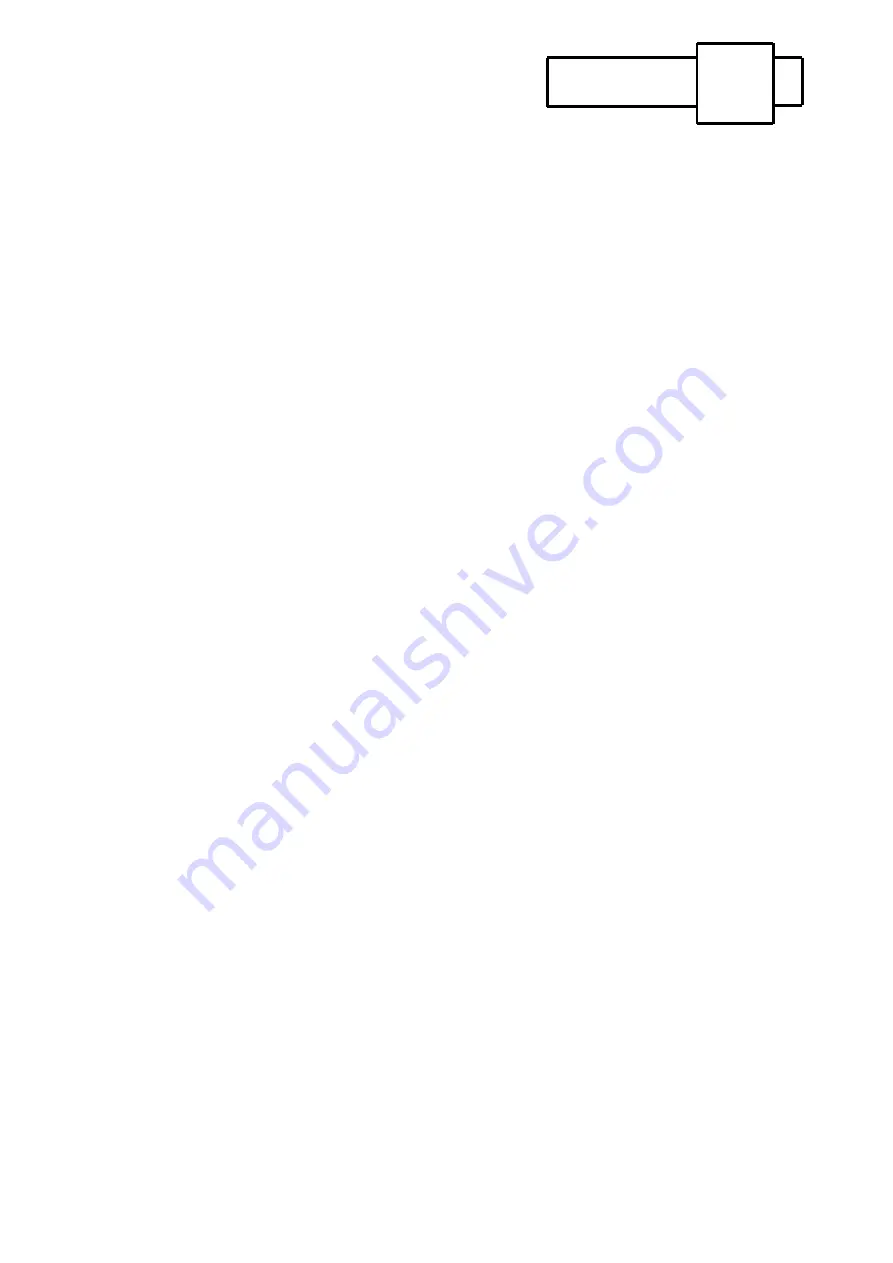
OUTLET HEAD ASSEMBLY
SECTION
A1
GENERAL
A1.4 ADJUSTMENT OF VARIABLE PURGE
The variable purge needle valves are situated in the top or rear of the outlet head on the dryer.
NOTE:
The dryer purge needle valves are factory set for 20% of rated flow of the dryer at 7
barg (102 psig) inlet pressure (18% actual @ 6 barg) The purge needle valves only
require adjustment if the inlet pressure to the dryer is not 7 bar g (102 psig).
TO ADJUST THE PURGE
A.
B.
C.
D.
E.
F.
G.
H.
Turn both valve adjusting screws clockwise until they are fully closed .
DO NOT OVER TIGHTEN THESE SCREWS.
The 4mm or 6mm plastic pipe which connects both valves together should be removed
from the push in connections on the valves by pressing on the face of the connection to
release the collet.
A flow meter (not supplied) which is capable of measuring the amount of purge air
required should be fitted to either one of the purge needle valves.
Allow the column, on which the purge needle valve functions to pressurise. Turn the
adjusting screw in an anticlockwise direction until the desired purge flow setting is
obtained. If the flow meter does not register after THREE TURNS, the adjacent
column is pressurising, wait for the desired column to pressurise and continue.
The operating pressure must be maintained throughout in order for the purge flow
setting to be correct.
When the above operation is complete and the correct purge flow is obtained, wait until
the adjacent column pressurises. Remove the flow meter from the previously adjusted
valve and attach to the unadjusted valve. Turn the adjusting screw anticlockwise until
the desired purge flow setting is obtained.
After adjustment has been carried out, remove the flow meter from the previously
adjusted valve. Replace the 4mm or 6mm plastic pipe. A proportionate amount of
purge air will exhaust when this pipe is being fitted, relative to the capacity of the
dryer.
The correctly adjusted unit is now ready for use. For settings other than 7 bar g, consult
the manufacturer.
NOTE: The maximum rated capacity of the flow meter as recommended by the
manufacturers instructions should be checked before use.
Page 7 of 30
Содержание SAR 003
Страница 1: ...MODELS SAR 003 TO SAR 175 DESICCANT DRYERS MAINTENANCE MANUAL DATE 24Mar2000 REV 1 ...
Страница 9: ...OUTLET HEAD ASSEMBLY SECTION A1 SAR003 to SAR 013 OUTLET HEAD Page 9 of 30 ...
Страница 10: ...OUTLET HEAD ASSEMBLY SECTION A1 OUTLET HEAD SAR 024 to SAR 088 Page 10 of 30 ...
Страница 11: ...OUTLET HEAD ASSEMBLY SECTION A1 SAR 106 to SAR 175 DUPLEX OUTLET HEAD Page 11 of 30 ...
Страница 12: ...Page 12 of 30 SECTION A2 COLUMN ASSEMBLY A2 1 A2 2 A2 3 Column Desiccant Removal Desiccant Replacement General ...
Страница 16: ...INLET HEAD ASSEMBLY SECTION A3 SAR 003 TO SAR 013 INLET HEAD Page 16 of 30 ...
Страница 17: ...INLET HEAD ASSEMBLY SECTION A3 SAR 024 TO SAR 088 INLET HEAD Page 17 of 30 ...
Страница 18: ...INLET HEAD ASSEMBLY SECTION A3 SAR 106 TO SAR 175 INLET HEAD Page 18 of 30 ...
Страница 21: ...CAM TIMER ASSEMBLY SECTION A4 SAR 003 TO SAR 013 CAM TIMER ASSEMBLY Page 21 of 30 ...
Страница 22: ...Page 22 of 30 SECTION A5 FAULT FINDING GUIDE ...
Страница 25: ...6 1 PIPING SCHEMATIC SAR 003 TO SAR 013 Page 25 of 30 ...
Страница 26: ...6 2 PIPING SCHEMATIC SAR 024 TO SAR 088 Page 26 of 30 ...
Страница 27: ...6 3 PIPING SCHEMATIC SAR 106 TO SAR 175 Page 27 of 30 ...
Страница 28: ...6 4 PIPING SCHEMATIC PNEUMATIC SAR 024 TO SAR 088 Page 28 of 30 ...