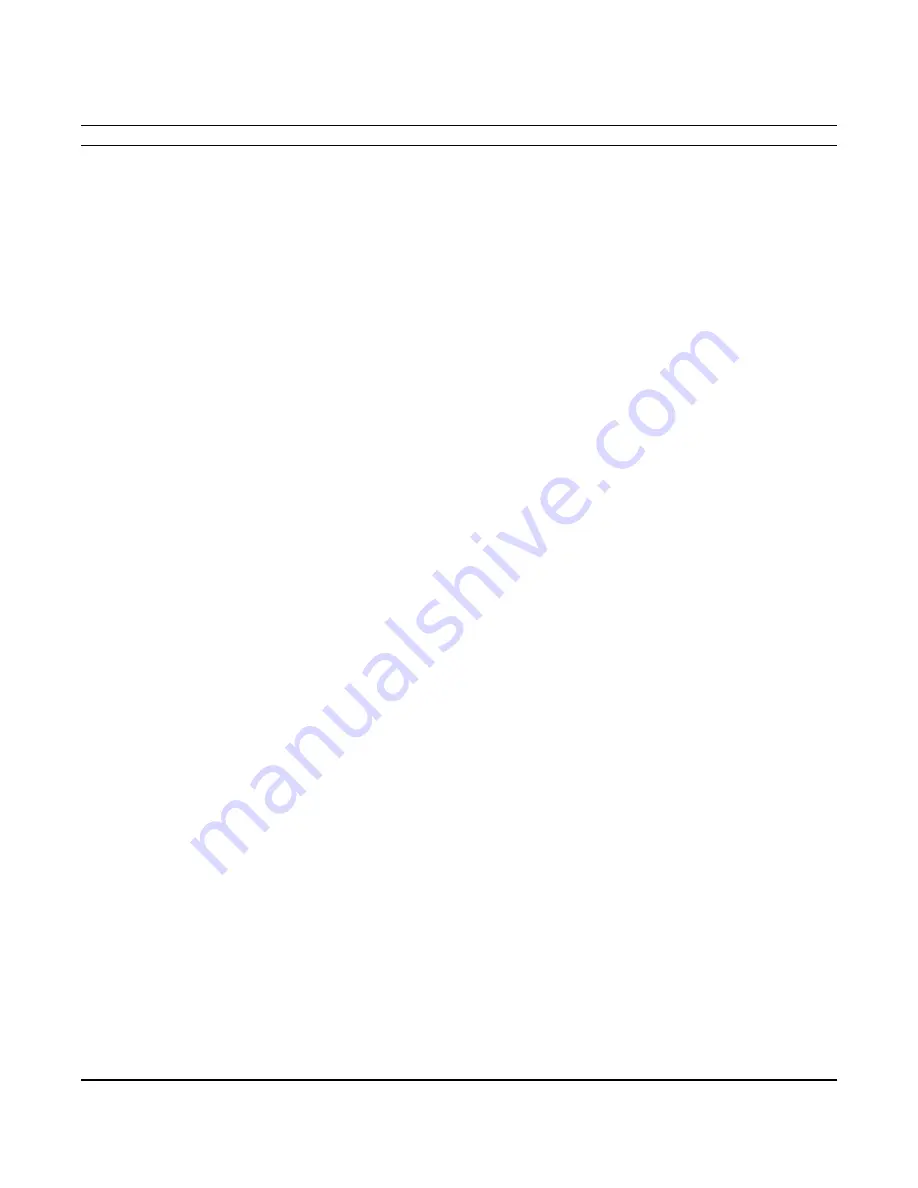
Section 5
OPERATION
32
5.2 PURPOSE OF CONTROLS- ELECTRO-MECHANICAL (CONTINUED)
CONTROL OR INDICATOR
PURPOSE
-BLINKING RED LED (CONT.)
“RUN STATUS” RED LED
FLUID LEVEL SIGHT GLASS
SEPARATOR RETURN LINE SIGHT GLASS
FLUID STOP VALVE
DISCHARGE CHECK VALVE
THERMAL VALVE
MINIMUM PRESSURE/CHECK VALVE
COMPRESSOR DISCHARGE
TEMPERATURE SWITCH
HIGH PRESSURE SHUTDOWN SWITCH
WATER PRESSURE SWITCH
(water-cooled compressors only)
PRESSURE RELIEF VALVE
SULLICON CONTROL
at any moment without any more user intervention.
Indicates when controls are in “AUTO” mode.
Monitors fluid level in the sump. Proper level should show
half-full in the sight glass. Check the level when the com-
pressor is shut down. DO NOT OVERFILL.
Used to indicate fluid flow in the return lines. When the com-
pressor is running at full load, fluid flow should be visible in
the primary sight glass with a very slight film in the second-
ary sight glass. There may be little or no flow when the com-
pressor is running unloaded, but a sluggish flow at full load
indicates a need to clean the return line strainer.
Cuts off flow of fluid to compressor unit at compressor shut-
down and allows flow of fluid to the unit on start-up.
Cuts off the reverse flow of air/fluid mixture through com-
pressor discharge system at compressor shutdown.
Regulates flow of fluid to and around the cooler. Designed to
maintain a minimum operating temperature of 180°F (82°C)
(195°F [91°C] for 24KT water-cooled models); used for fast
warm-up on start-up.
Maintains minimum of 50 psig (3.4 bar) in the compressor
sump. Valve piston restricts receiver air discharge from re-
ceiver/sump when pressure falls to 40 psi (2.8 bar). Prevents
line pressure backflow into the sump during unload condi-
tions and after shutdown.
Designed to shut the compressor down when the discharge
temperature reaches 240°F (115°C).
An added protective device designed to shut down the com-
pressor when the pressure becomes too high. This switch is
set for shutdown at approximately 135 psig (9.3 bar). When
resetting, pressure is 100 psig (6.9 bar) or 25 psi (1.7 bar)
above operating pressure.
Prevents compressor operation if water pressure is too low.
Standard setting is 15 psig (1.03 bar).
Opens sump pressure to the atmosphere should pressure in-
side the sump become too high (200 psig [13.8 bar]).
Operation of this valve indicates that the high pressure
switch is either faulty or out of adjustment.
Regulates the amount of air allowed to enter the air inlet
valve. This regulation is determined by the amount of air
Содержание LS-25
Страница 13: ...Section 2 DESCRIPTION 7 Figure 2 2 Cooling and Lubrication System...
Страница 14: ...Section 2 DESCRIPTION 8 Figure 2 3A Compressor Piping and Instrumentation Diagram Electro mechanical...
Страница 15: ...Section 2 DESCRIPTION 9 Figure 2 3B Compressor Piping and Instrumentation Diagram Supervisor...
Страница 17: ...Section 2 DESCRIPTION 11 Figure 2 4 Compressor Discharge System...
Страница 18: ...Section 2 DESCRIPTION 12 Figure 2 5A Compressor System Start Electro mechanical...
Страница 19: ...Section 2 DESCRIPTION 13 Figure 2 5B Compressor System Full Load Electro mechanical...
Страница 20: ...Section 2 DESCRIPTION 14 Figure 2 5C Compressor System Modulation Electro mechanical...
Страница 21: ...Section 2 DESCRIPTION 15 Figure 2 5D Compressor System Unload Electro mechanical...
Страница 22: ...Section 2 DESCRIPTION 16 Figure 2 6A Control System Start Supervisor with Spiral Valve...
Страница 23: ...Section 2 DESCRIPTION 17 Figure 2 6B Control System Full Load Supervisor with Spiral Valve...
Страница 24: ...Section 2 DESCRIPTION 18 Figure 2 6C Control System Modulation Supervisor with Spiral Valve...
Страница 25: ...Section 2 DESCRIPTION 19 Figure 2 6D Control System Unload Supervisor with Spiral Valve...
Страница 28: ...Section 2 DESCRIPTION 22 Figure 2 8 Typical Machine Connection Electro mechanical...
Страница 30: ...NOTES 24...
Страница 33: ...Section 3 SPECIFICATIONS 27 Figure 3 1A Compressor Identification Air cooled...
Страница 34: ...Section 3 SPECIFICATIONS 28 Figure 3 1B Compressor Identification Water cooled...
Страница 40: ...Section 6 SUPERVISOR 34 Figure 6 1 Supervisor Panel...
Страница 60: ...Section 8 ILLUSTRATIONS AND PARTS LIST 54 8 3 MOTOR COMPRESSOR FRAME AND PARTS...
Страница 62: ...Section 8 ILLUSTRATIONS AND PARTS LIST 56 8 4 AIR INLET SYSTEM...
Страница 64: ...Section 8 ILLUSTRATIONS AND PARTS LIST 58 8 5 COOLING LUBRICATION AIR COOLED...
Страница 66: ...Section 8 ILLUSTRATIONS AND PARTS LIST 60 8 6 COOLING AND LUBRICATION SYSTEM WATER COOLED...
Страница 68: ...Section 8 ILLUSTRATIONS AND PARTS LIST 62 8 7 COOLER ASSEMBLY L MODEL...
Страница 70: ...Section 8 ILLUSTRATIONS AND PARTS LIST 64 8 8 COOLER ASSEMBLY XH MODEL...
Страница 72: ...Section 8 ILLUSTRATIONS AND PARTS LIST 66 8 9 WATER PIPING WATER COOLED...
Страница 74: ...Section 8 ILLUSTRATIONS AND PARTS LIST 68 8 10 DISCHARGE SYSTEM AIR COOLED...
Страница 76: ...Section 8 ILLUSTRATIONS AND PARTS LIST 70 8 10 DISCHARGE SYSTEM AIR COOLED...
Страница 78: ...Section 8 ILLUSTRATIONS AND PARTS LIST 72 8 11 DISCHARGE SYSTEM WATER COOLED...
Страница 80: ...Section 8 ILLUSTRATIONS AND PARTS LIST 74 8 11 DISCHARGE SYSTEM WATER COOLED...
Страница 82: ...Section 8 ILLUSTRATIONS AND PARTS LIST 76 8 12 SULLICON CONTROL...
Страница 84: ...Section 8 ILLUSTRATIONS AND PARTS LIST 78 8 12 SULLICON CONTROL...
Страница 86: ...Section 8 ILLUSTRATIONS AND PARTS LIST 80 8 13 ACTUATOR VALVE...
Страница 88: ...Section 8 ILLUSTRATIONS AND PARTS LIST 82 8 14 CONTROL SYSTEM ELECTRO MECHANICAL...
Страница 90: ...Section 8 ILLUSTRATIONS AND PARTS LIST 84 8 15 CONTROL SYSTEM SUPERVISOR...
Страница 92: ...Section 8 ILLUSTRATIONS AND PARTS LIST 86 8 16 UNIT TUBING...
Страница 94: ...Section 8 ILLUSTRATIONS AND PARTS LIST 88 8 17 INSTRUMENT PANEL ELECTRO MECHANICAL...
Страница 96: ...Section 8 ILLUSTRATIONS AND PARTS LIST 90 8 18 INSTRUMENT PANEL SUPERVISOR...
Страница 98: ...Section 8 ILLUSTRATIONS AND PARTS LIST 92 8 19 ELECTRICAL BOX...
Страница 100: ...Section 8 ILLUSTRATIONS AND PARTS LIST 94 8 20 ENCLOSURE...
Страница 102: ...Section 8 ILLUSTRATIONS AND PARTS LIST 96 8 20 ENCLOSURE...
Страница 104: ...Section 8 ILLUSTRATIONS AND PARTS LIST 98 8 21 DECAL GROUP...
Страница 106: ...Section 8 ILLUSTRATIONS AND PARTS LIST 100 8 21 DECAL GROUP...
Страница 108: ...Section 8 ILLUSTRATIONS AND PARTS LIST 102 8 22 DECAL LOCATION REFERENCE AIR COOLED LESS ENCLOSURE...
Страница 110: ...Section 8 ILLUSTRATIONS AND PARTS LIST 104 8 23 DECAL LOCATION REFERENCE WATER COOLED LESS ENCLOSURE...
Страница 112: ...Section 8 ILLUSTRATIONS AND PARTS LIST 106 8 24 DECAL LOCATION REFERENCE TYPICAL ENCLOSURE...
Страница 114: ...Section 8 ILLUSTRATIONS AND PARTS LIST 108 8 25 WIRING DIAGRAM STANDARD FULL VOLTAGE ELECTRO MECHANICAL 02250125 969R1...
Страница 115: ...Section 8 ILLUSTRATIONS AND PARTS LIST 109 8 26 WIRING DIAGRAM WYE DELTA ELECTRO MECHANICAL 02250125 970R1...
Страница 116: ...Section 8 ILLUSTRATIONS AND PARTS LIST 110 8 27 WIRING DIAGRAM STANDARD FULL VOLTAGE SUPERVISOR 02250113 462R5...
Страница 117: ...Section 8 ILLUSTRATIONS AND PARTS LIST 111 8 28 WIRING DIAGRAM WYE DELTA SUPERVISOR 02250113 463R6...
Страница 118: ...Section 8 ILLUSTRATIONS AND PARTS LIST 112 8 29 WIRING DIAGRAM SOLID STATE STARTER SUPERVISOR 02250113 467R0...
Страница 119: ......