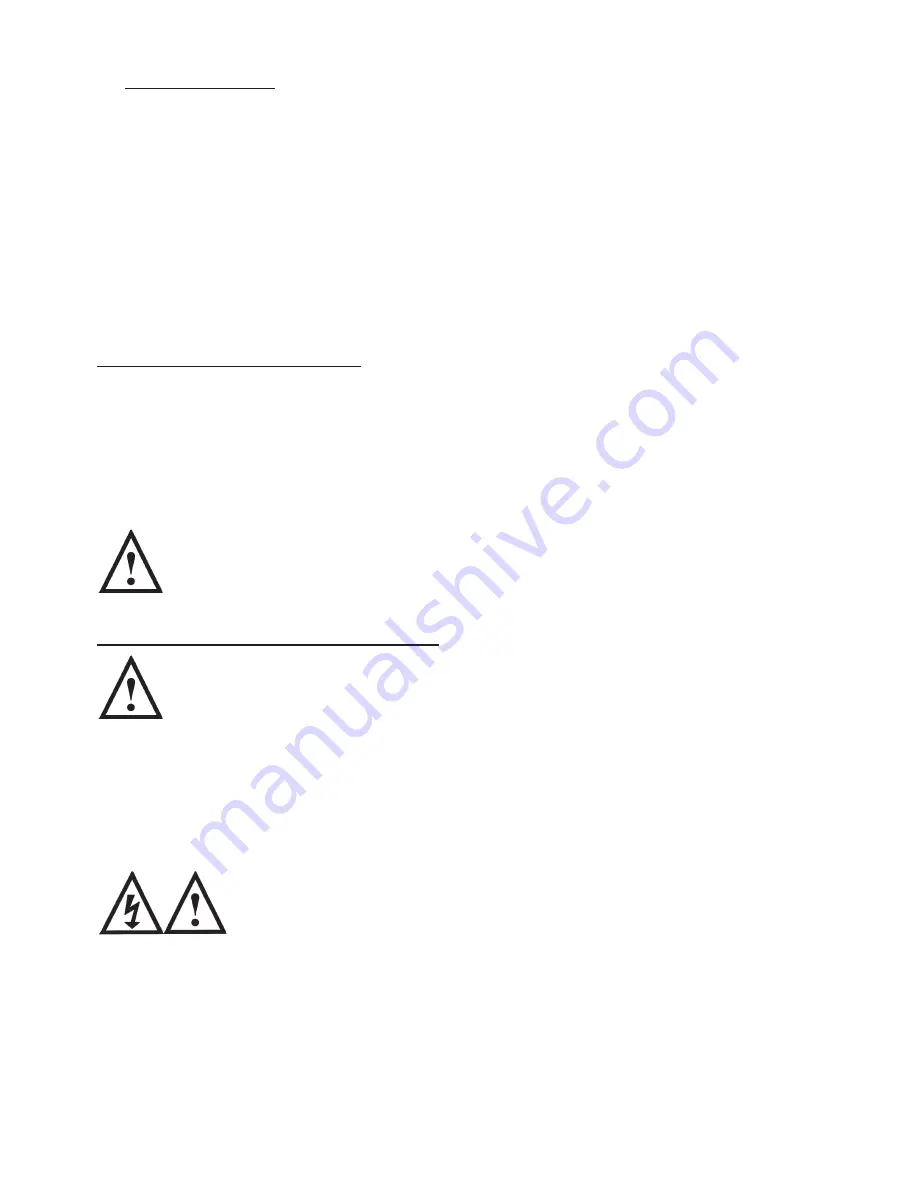
- 15 -
Cont ...
5. Starting
The
Pump
a) Ensure all outlets are closed, turn power supply ‘on’ - pump will start, pressurise
the system then stop.
b) Open and close all outlets in turn associated with the pump, allowing liquid to
flow from each outlet until all air is purged. As each outlet is opened and closed,
the pump will start and stop respectively.
Note: After closing the outlet there will be a small delay time before the pump
stops, which is normal.
Any tap or control valve within the system when opened and closed will now turn
the pump on/off. Providing this is the case the system is now operating correctly.
c) Carefully check pump and pipework for leaks whilst pump running and stationary
before leaving the installation unattended.
For Further Technical Support
Phone the Stuart Turner Pump Assist team on 0844 98 000 97. Our staff are trained to
help and advise you over the phone or arrange for a service engineer to call.
Note: When pumps are installed in another manufacturers original equipment, please
contact the manufacturer for advice.
MAINTENANCE
WARNINGS:
Care should be taken to protect pump from frost and freezing.
If possible site the pump in a location where in the unlikely event of a
liquid leak, any spillage is contained or routed to avoid electrics or
areas sensitive to liquid damage.
Cleaners, disinfectants and descalents
On installations where chemical disinfectants or descalents are periodically
used, the compatibility of the chemical solution regarding the pump must be
considered.
Acid based descalents and aggressive cleaning agents must not come into
contact with the pump. The pump must be removed from the system prior to the
use of these products. The system should be flushed to remove all chemicals
before the pump is re-connected.
If in any doubt as to the suitability of the chemical solutions refer to Stuart
Turner Ltd.
1. No routine maintenance is required, but provision should be made
for easy access to the pump to allow repairs due to normal wear
and
tear.
2. Disconnect electrical supply before working on pump.
3. Turn off liquid supplies to the pump and release pressure by opening liquid outlets
before attempting maintenance.
4. Inlet strainers and footvalve strainers when fitted may require periodical cleaning.
The frequency of this operation is dependent upon installation conditions.