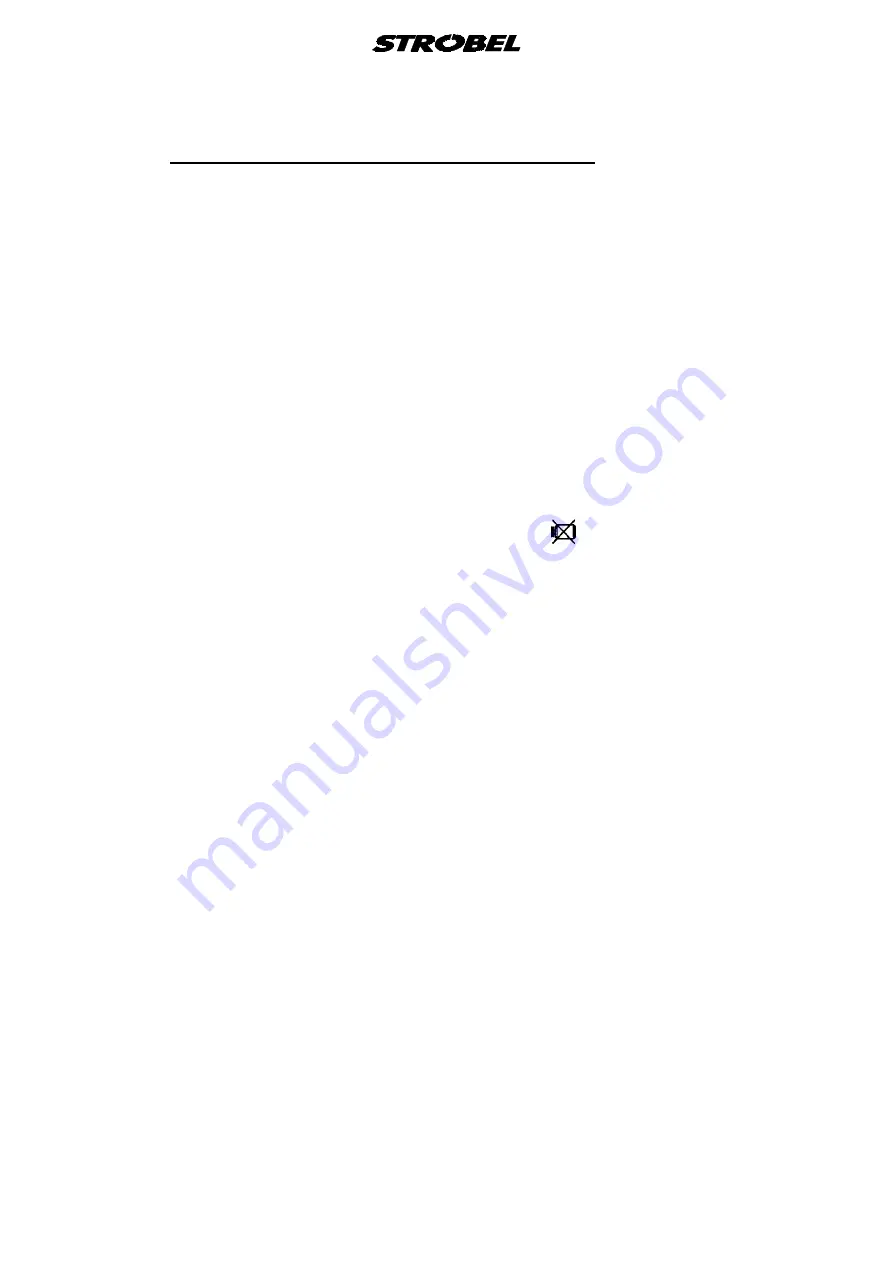
33
BA_KA-ED_A22_190313_en.doc
5.2
Setting the light barriers (Fig. 16a + Fig. 17)
Inspect (check) first whether the holder ((4), (5)) is not twisted, the light barrier is
aligned at a right angle to the mittor/reflex foil, no dust is on the mirror/reflex foil and
the mirror/reflex foil is not damaged. (Fig. 16a)
The light barriers are already pre-adjusted according to Fig. 16a.
The settings of the light barriers are performed without material.
The switching operation of the light barriers is indicated by a red LED
as follows:
LED is lit
-
light ray is reflected by the reflex foil.
LED is not lit
-
light ray is interrupted or maladjusted
Adjusting the light barrier is done as follows:
-
Move carriage to basic position.
-
Switch on “Sewing stop” with button 1 on the operating control V810.
-
Switch toggle switch S6 on the switch box to “
” position
(“0” position).
-
Switch on sewing lamp.
-
Switch on solenoid 1V2 with the manual switch
(clamping device closes).
-
Check mirror (1) and reflex foil (2), grid foils and light barriers for dirt or damage.
-
Compl. Align light barriers (S8-1, S10 and S8-2) at a right angle to the
mirror/reflex foil.
(4) and (5) need to be aligned horizontal and parallel to the
mirror/reflex foil and lifter lever. (Fig. 16a)
-
Adjust the light barrier at a right angle to the mirror/reflex foil in such a way that
the infrared ray from S8-1 is reflected at about the middle of the upper third of
the mirror at a right angle and that the red LED lights up. (In case the LED does
not light up, the adjustment knurl needs to be tuned to the right.) (Fig. 17)
-
Turn the adjustment knurl to the left until the LED goes out, then to the right
until it just lights up again and then turn it finally 15 degrees to the right. (If you
then want to turn the adjustment knurl to the left (setting correction), you
should turn the adjustment knurl all the way back and perform the setting
again).
Содержание KA-ED
Страница 8: ...4 BA_KA ED_A22_190313_en doc Fig 1 ...
Страница 36: ...32 BA_KA ED_A22_190313_en doc Fig 16 a Light barriers for right machine Left machine is mirrored b ...
Страница 40: ...36 BA_KA ED_A22_190313_en doc Fig 18 Fig 19 ...
Страница 46: ...42 BA_KA ED_A22_190313_en doc Fig 24 ...
Страница 49: ...45 BA_KA ED_A22_190313_en doc Fig 26 ...
Страница 56: ...52 BA_KA ED_A22_190313_en doc Fig 34 ...
Страница 64: ......