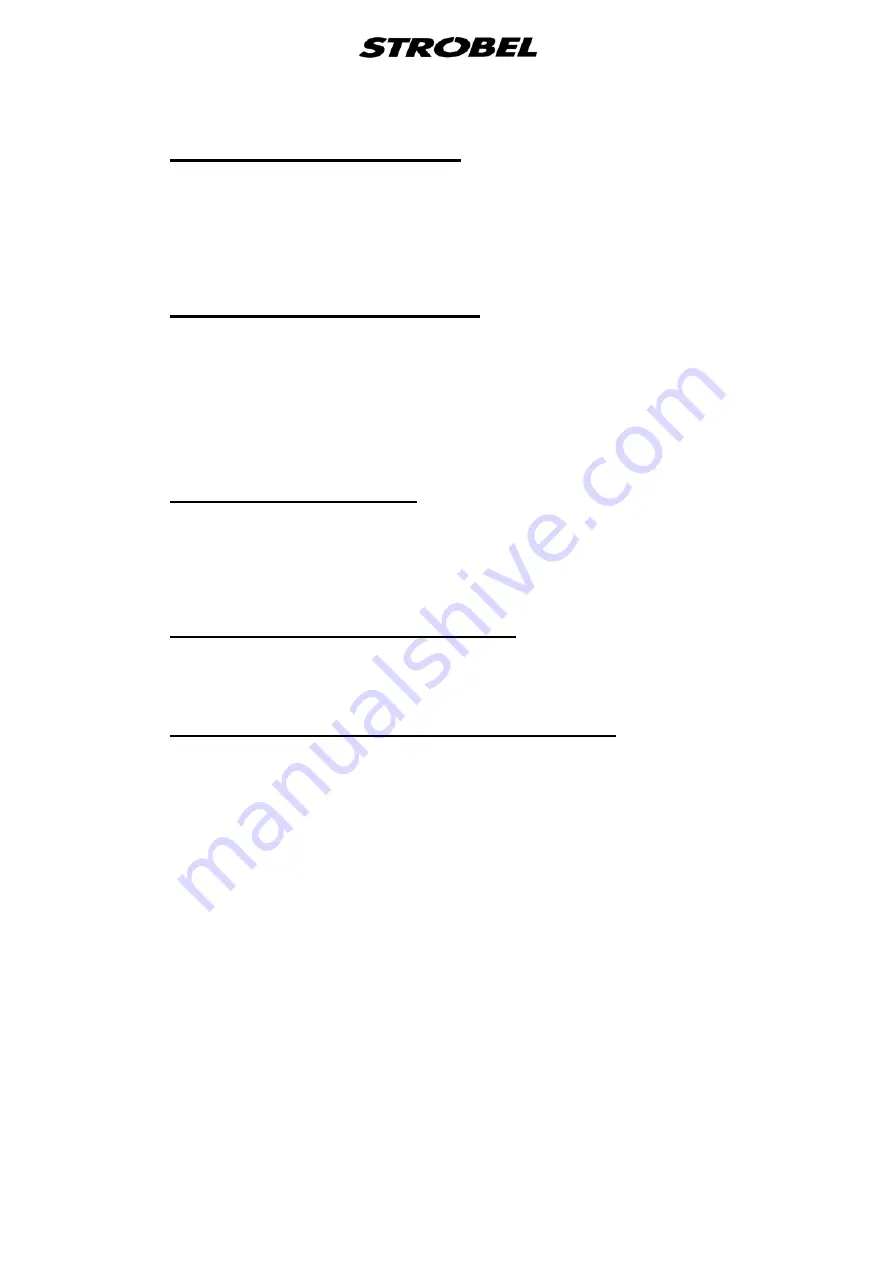
20
MA_141_142_A10-6-7-3-6-5_130617_en
4.5.8
Adjust the rear bearing block
The looper movement may be altered in the final positions by shifting the rear
bearing block (N) (Fig. 1 and Fig. 6). On its return movement, the looper gets
close to the needle in its vertical- and front position, without essentially
changing its height in the rear position. (Ratio approx. 10:1). When moving
forth, the distance between looper and needle increases.
4.6
Adjust height of rear feed cups
Fit bushings 150.0170 and 150.0281 so that the lower bushing is on a level with
the surface on which the free wheeling is screwed, that the bottom socket is
4 mm within the bolting surface for the free wheel; the top socket needs to
provide the distance for the transport plate. In the mounted state with the
transport shaft head the distance between needle shaft middle and transport
plate top edge is the measurement “a” from Fig. 6.
4.7
Mount the front feed cup
When mounting the front feed cup onto the machine, make sure to fix it
horizontally and 0.1 mm lower than the rear feed cup. If the machine is
equipped with a needle guard, the needle groove must be another 0.1 mm
below the upper edge of the front feed cup.
4.8
Length adjustment of bar 133.0851
between stitch regulation rod and free wheeling
The distance between the two drill holes
∅
6 must be 111 mm. (Fig. 5)
4.9
Thread lifting mechanism at needle bar head
Class 141: Adjust lifting bar 124.0053 so that the thread is lifted – on the
needle’s backwards movement – when the looper is placed vertically above the
needle and has taken up the loop. Then – while the needle moves forth – until
the looper’s point reaches the center of the needle. (Fig. 1)
The same applies to class 142. In other words, the thread must be loose
(without tension) from the moment the looper takes it up until the looper’s right
hand turning point. Make sure that thread clamping bolt 138.0081 at the needle
bar head releases the thread just about 0.3 mm. You should also consider that
threads vary according to machine class and application.
(Fig. 9)
The thread drag on the needle bar is 0.35 - 0.4 N.
Содержание 141-23EV
Страница 4: ......
Страница 8: ...4 MA_141_142_A10 6 7 3 6 5_130617_en...
Страница 16: ...12 MA_141_142_A10 6 7 3 6 5_130617_en Fig 1 Fig 2...
Страница 33: ...29 MA_141_142_A10 6 7 3 6 5_130617_en Fig 14...
Страница 37: ......
Страница 38: ......