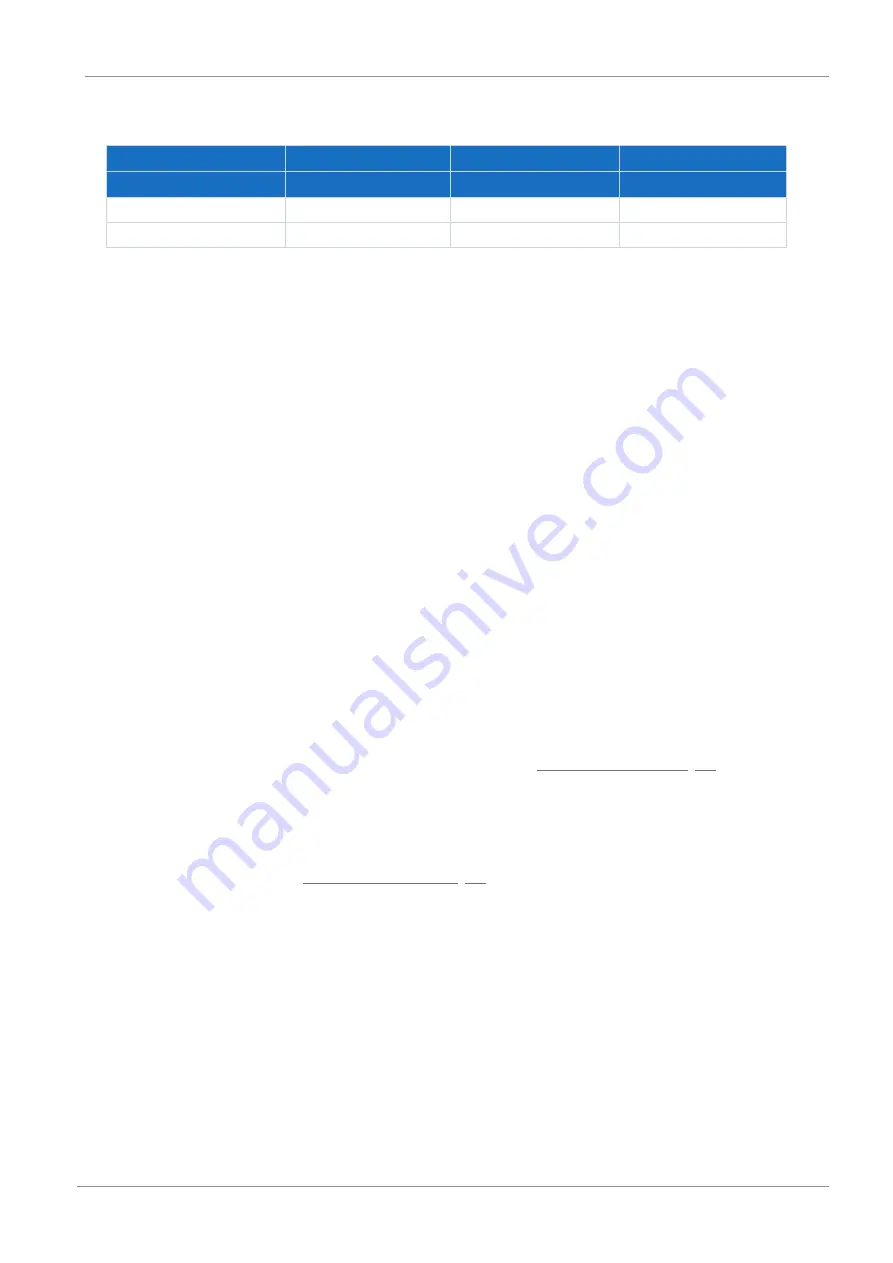
5 | Installation
10/2019 | ID 443150_en.00
31
Tightening torques for the locking screw (11)
Type
KS
s
M
A
[mm]
[Nm]
KL102
M4
3
2.9
KL202
M6
5
10
Abbreviations used:
§
KS = Nominal diameter of the locking screw (11)
§
M
A
= Tightening torque for the locking screw (11)
§
s = Size of the hexagon insert (3)
5.3
Mounting the output shaft
This chapter contains information on how to correctly connect the different designs of the gear unit output shaft with the
machine so that the torque can be transmitted properly.
5.3.1
Mounting drive elements on a solid shaft
This chapter describes the assembly of drive elements, such as hubs, belt drives, couplings, pinions or sprockets, on the
output of a gear unit with a solid shaft and feather key.
When mounting drive elements on a solid shaft without a feather key, observe the technical documentation of the drive
element in question.
ATTENTION! Damage to encoders, bearings and shafts due to improper assembly!
Never use force when
mounting drive elements with fittings, e.g. hitting drive elements, shafts or the motor or gear unit housing with a hammer,
and instead install them in accordance with the instructions in the documentation.
Prerequisites
§
The drive element does not cause any impermissible shaft loads (e.g. tensioning the belt on a belt drive). Information
on permissible shaft loads can be found in the corresponding catalog (see
).
§
The drive element is balanced.
§
The tolerance of the inner hole of the drive element corresponds to ISO H7.
§
The keyway of the drive element corresponds to DIN 6885-1 (if not otherwise specified).
§
The information in the chapter
§
A mounting device suitable for the drive element is available (not included in the scope of delivery).
Procedure
1.
Remove the corrosion protection from the solid shaft.
2.
Degrease the inner hole of the drive element.
3.
Mount the drive element on the solid shaft with the aid of a mounting device positioned on the centering hole of the
solid shaft. Details can be found in the following figure and table.
4.
If the drive element is difficult to hoist, do not use force and instead heat it to about 80 °C beforehand.
5.
If the length of the solid shaft is greater than the length of the drive element, use an appropriate spacer bushing that
you position between the plate (1) and drive element (5).