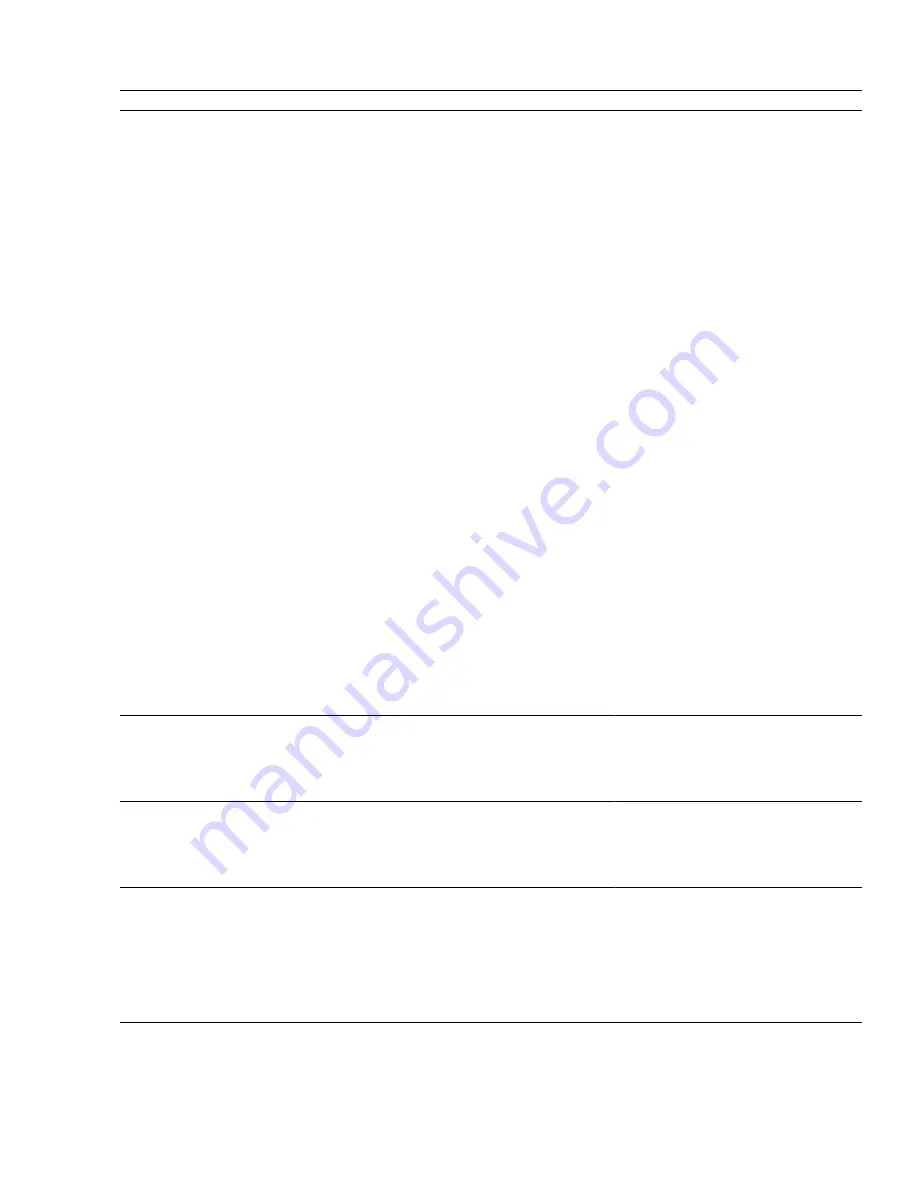
15
MS 311, MS 391
Condition
Cause
Remedy
Engine speed drops quickly under
load – low power
Air filter dirty
Clean air filter or replace if
necessary
Throttle shutter not opened fully
Check throttle cable and rod
Tank vent faulty
Replace tank vent
Fuel pickup body dirty
Install new pickup body
Fuel strainer dirty
Clean fuel strainer in carburetor,
replace if necessary
Leak on fuel hose from tank to
carburetor
Seal connections or install new fuel
hose
Setting of high speed screw
H
too
rich
Check basic carburetor setting,
correct if necessary
Main jet bores or ports blocked
Clean the carburetor
Pump diaphragm damaged or
fatigued
Fit new pump diaphragm
Ignition timing wrong, flywheel out
of adjustment, key in flywheel has
sheared off
Fit key if necessary and secure
flywheel properly or install new
flywheel
Engine running extremely rich, has
no power and a very low maximum
speed
Air valve does not open
Check the carburetor and service
or replace if necessary.
Engine running too rich, loss of
power and maximum speed too low
Air valve does not open fully in full
throttle position
Check the carburetor and service
or replace if necessary.
Erratic idle – too lean
Air valve does not close completely Check the end cover with air valve
and replace if necessary
Intake manifold faulty
Install new intake manifold