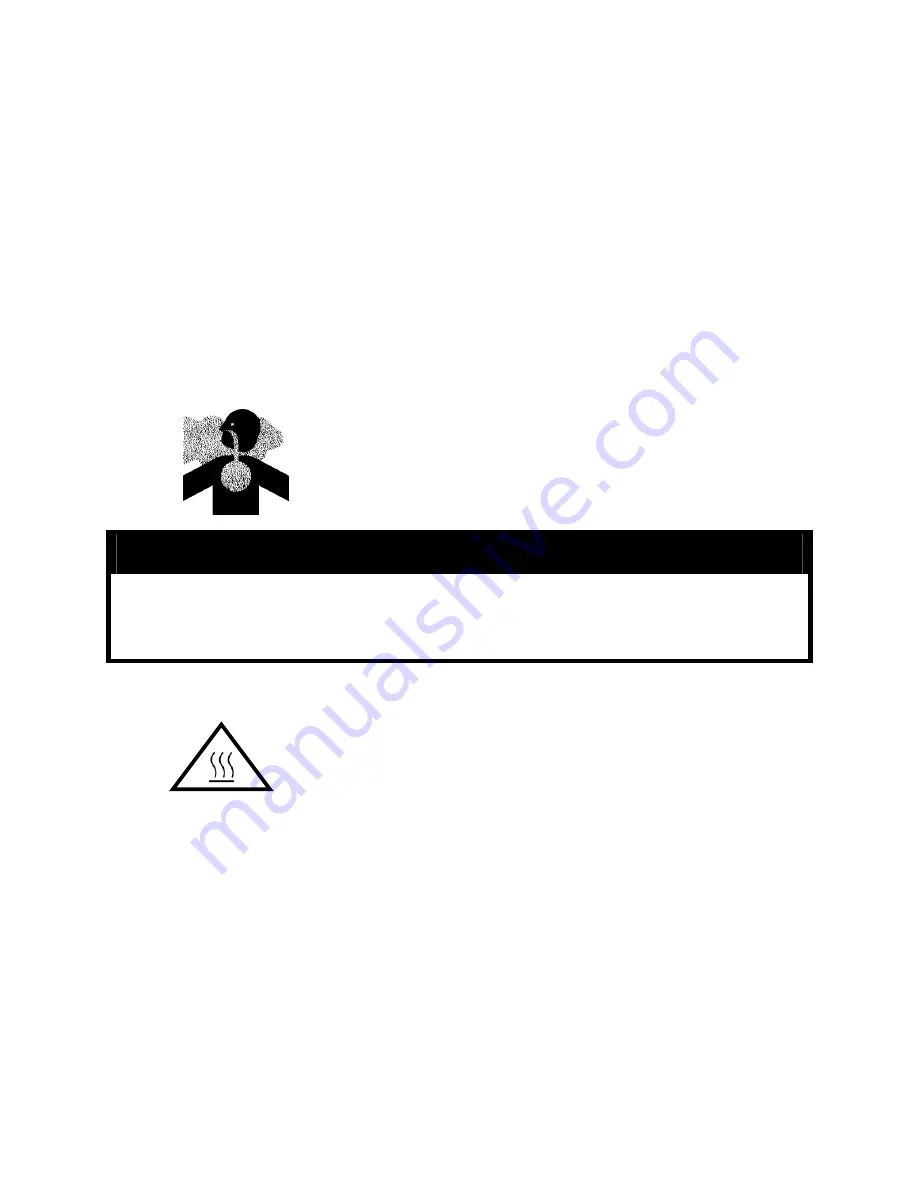
5-3 Corrective
Maintenance
This section provides you with the information necessary to correct or repair any issues
which might appear during the normal operation of your dehumidifying dryer. Although we
have listed how to perform these procedures, it is recommended that you call the Service
Department to have any in-depth maintenance performed.
Symptoms of Worn Desiccant
The moisture absorption capacity of the desiccant used in your dehumidifying dryer degrades
after an indefinite period of time. Useful life depends on variables such as the condition of the
process filter, how much dust and fines have been passed through the filter and got into the
desiccant chamber, and plasticizer vapors in the return air.
WARNING!
Handling desiccant material is HAZARDOUS.
Wear an N-100 type safety filter mask or equivalent to avoid prolonged
breathing of desiccant dust. Wear safety goggles and gloves to avoid
contact with eyes and skin.
•
Handle with adequate ventilation.
•
Wash hands thoroughly after handling.
+ FIRST AID +
In case of eye contact, immediately flush eyes
with plenty of water for at least 15 minutes.
SEE A PHYSICIAN IMMEDIATELY IF IRRITATION PERSISTS.
Replacing Worn Desiccant
Caution!
DESICCANT BEDS ARE HOT DURING OPERATION.
To avoid burn hazard, make sure desiccant beds are sufficiently cool
before replacing worn desiccant.
To access the Desiccant Bed:
1.
Disconnect electrical power to the dryer.
2.
Using a 1/8” Allen wrench, remove the four (4) 10-32 button head screws holding the
Desiccant Cap to the Regeneration Heater.
3.
Remove the Desiccant Cap.
4.
With a shop vacuum, carefully remove all desiccant from each tower.
Portable Drying/Conveying Systems
Chapter 5: Maintenance
43 of 63