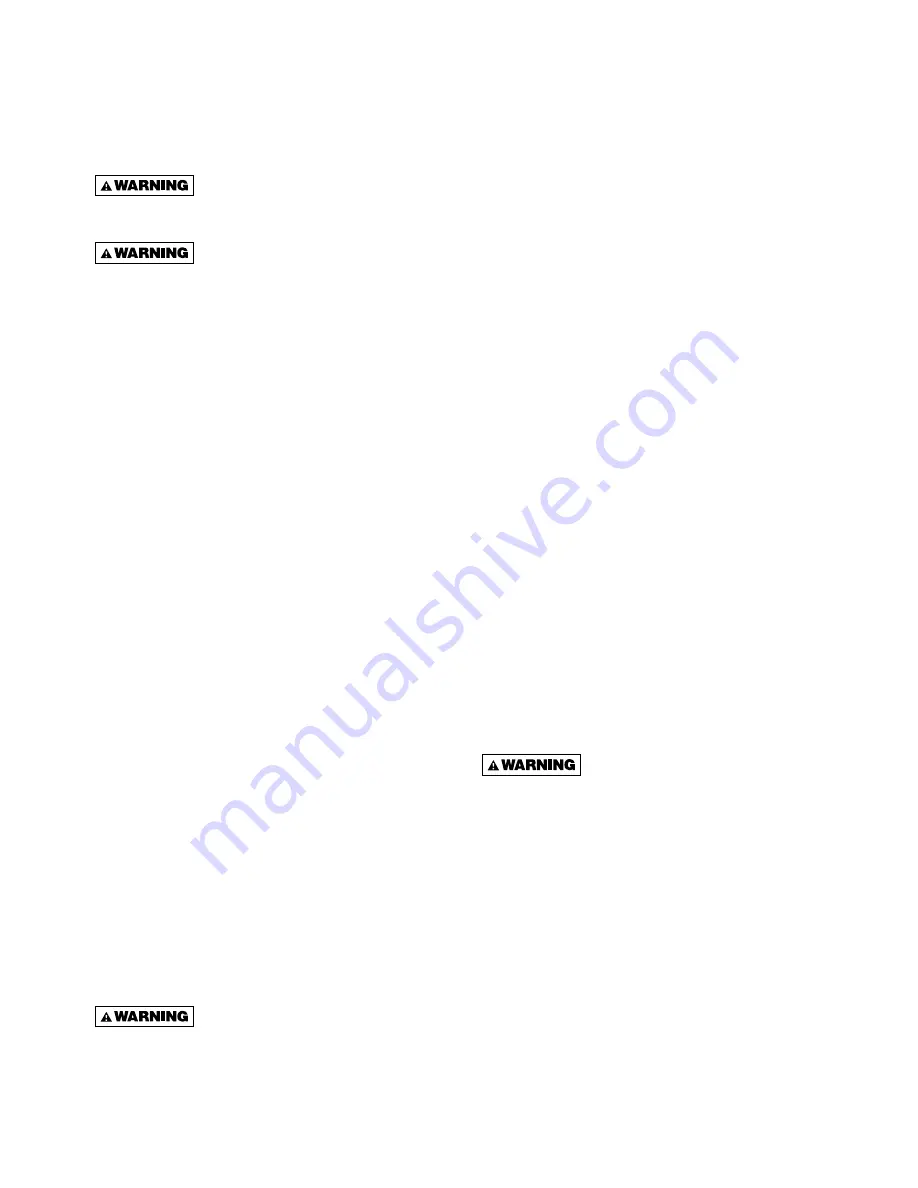
26
INSTALLATION - VENTING – CATEGORY III
COMBUSTION AIR VENTING AND PIPING
Never operate unit heaters without
combustion air and flue gas piping in place or
severe personal injury or death may occur!
CARBON MONOXIDE!
Your venting system must not be blocked by
any snow, snow drifts, or any foreign matter.
Inspect your venting system to ensure adequate
ventilation exists at all times! Failure to heed
these warnings could result in Carbon Monoxide
Poisoning (symptoms include grogginess, lethargy,
inappropriate tiredness, or fl u-like symptoms).
1. The combustion air system installation must be in
accordance with the current edition of the National
Fuel Gas Code-NFPA 54 or ANSI Z223.1 National
Fuel Gas Code. In Canada, installation must be
in accordance with CAN/CGA-B149.1 “Installation
Code for Natural Gas Burning Appliances and
Equipment” and CAN/CGA-B149.2 “Installation Code
for Propane Burning Appliances and Equipment”.
2. The concentric vent box, inlet air screen, defl ector
disk, and vent terminal provided with the unit heater
must be installed at the termination point of the
combustion air/vent system. See Figures 20, 21, 22,
23 and 24 and Table 6.
3. Each unit heater MUST have its own combustion
air system. It MUST NOT be connected to other air
intake systems.
4. Use single wall pipe constructed of 26 GA galvanized
steel or a material of equivalent durability and
corrosion resistance for the vent system. For
installations in Canada, use corrosion resistant
and gas-tight, listed vent pipe conforming with local
building codes, or in the absence of local building
codes, with current CAN/CGA-B149.1, Installation
Codes for Natural Gas Burning Appliances and
Equipment or CAN/CGA-B149.2, Installation Codes
for Propane Gas Burning Appliances and Equipment.
For residential installations in the United States, vent
pipe approved for Category III appliances must be
used between the appliance and the concentric
vent box unless 33% of the vent run is vertical, then
single wall galvanized vent pipe or double wall Type
B vent pipe may be used between the appliance and
the concentric vent box. A single length of double
wall Type B vent pipe must be used to go through
the concentric vent box and outside wall to the vent
terminal.
Never use pipe other than diameter
stated in Table 1. Never use PVC, ABS or any other
non-metallic pipe for venting! To do so may result
in serious damage to the unit and or severe
personal injury or death!
5. Long runs of single wall combustion air piping
passing through an unheated space may require
insulating if condensation becomes noticeable.
6. The combustion air system must be installed to
prevent collection of condensate. Pitch horizontal
pipes downward 1/4 inch per foot toward the inlet
cap to facilitate drainage. Vertical combustion air
pipes should be piped as depicted in Figure 22.
7. The equivalent length of the combustion air system
must not be less than 5 feet (1.5m) and must not
exceed 30 feet (9m). Equivalent length equals the
total length of straight pipe plus 5 feet (1.5m) for each
90° elbow and 2.5 feet (0.76m) for each 45° elbow.
NOTICE: For optimum performance keep the
combustion air system as straight as possible.
8. Each slip joint must be secured with at least three
corrosion resistant screws. Two full turns of 3M #425
Aluminum Foil Tape or its equivalent must then be
used to seal each joint. General Electric RTV-108,
Dow-Corning RTV-732 or an equivalent silicone
sealant with a temperature rating of 500°F may be
used instead of the tape.
9. For horizontal combustion air systems longer than
5 feet (1.5m), the system must be supported from
overhead building structures at 4 foot (1.2m) intervals
in the U.S. and at 3 foot (0.91m) intervals in Canada.
EXHAUST VENTING
NOTICE: Every Separated Combustion unit to
be installed MUST use the Factory supplied
Concentric Vent Kit. If you do not have this kit,
contact the manufacturer ASAP to obtain one prior
to installation.
Never operate unit heaters without
combustion air and fl ue gas piping in place or
severe personal injury or death may occur!
1. Vent system installation must be in accordance with the
current National Fuel Gas Code-NFPA 54 or ANSI Z223.1
National Fuel Gas Code. In Canada installation must be
in accordance with CAN/CGA-B149.1 “Installation Code
for Natural Gas Burning Appliances and Equipment”
and CAN/CGA-B149.2. “Installation Code for Propane
Burning Appliances and Equipment”.
2.
The Concentric Vent Kit (which includes a
concentric vent box, air inlet screen, deflector
collar, vent terminal and inlet air collar) provided
with the heater by the manufacturer MUST
be installed at the termination point of the
combustion air/vent system.
See Figures 20, 21,
22, 23 and 24 and Table 6.
3. Each unit heater MUST have it’s own vent system. It
MUST NOT be connected to other vent systems or
to a chimney.
SEPARARTED COMBUSTION
Содержание GG-30
Страница 11: ...11 ELECTRICAL CONNECTIONS continued Figure 11A Honeywell Control Board Figure 10A UT Control Board ...
Страница 20: ...20 Figure 14 Vent Support D 06839A ...
Страница 24: ...24 Figure 16 Figure 17 VENTING continued ...
Страница 25: ...25 VENTING continued Figure 18 Figure 19 ...
Страница 28: ...28 Figure 22 Vertical Intake Vent Installation Figure 21 Concentric Vent Installation ...
Страница 44: ...www sterlinghvac com HVAC PRODUCTS 260 NORTH ELM ST WESTFIELD MA 01085 TEL 413 564 5540 FAX 413 562 5311 ...