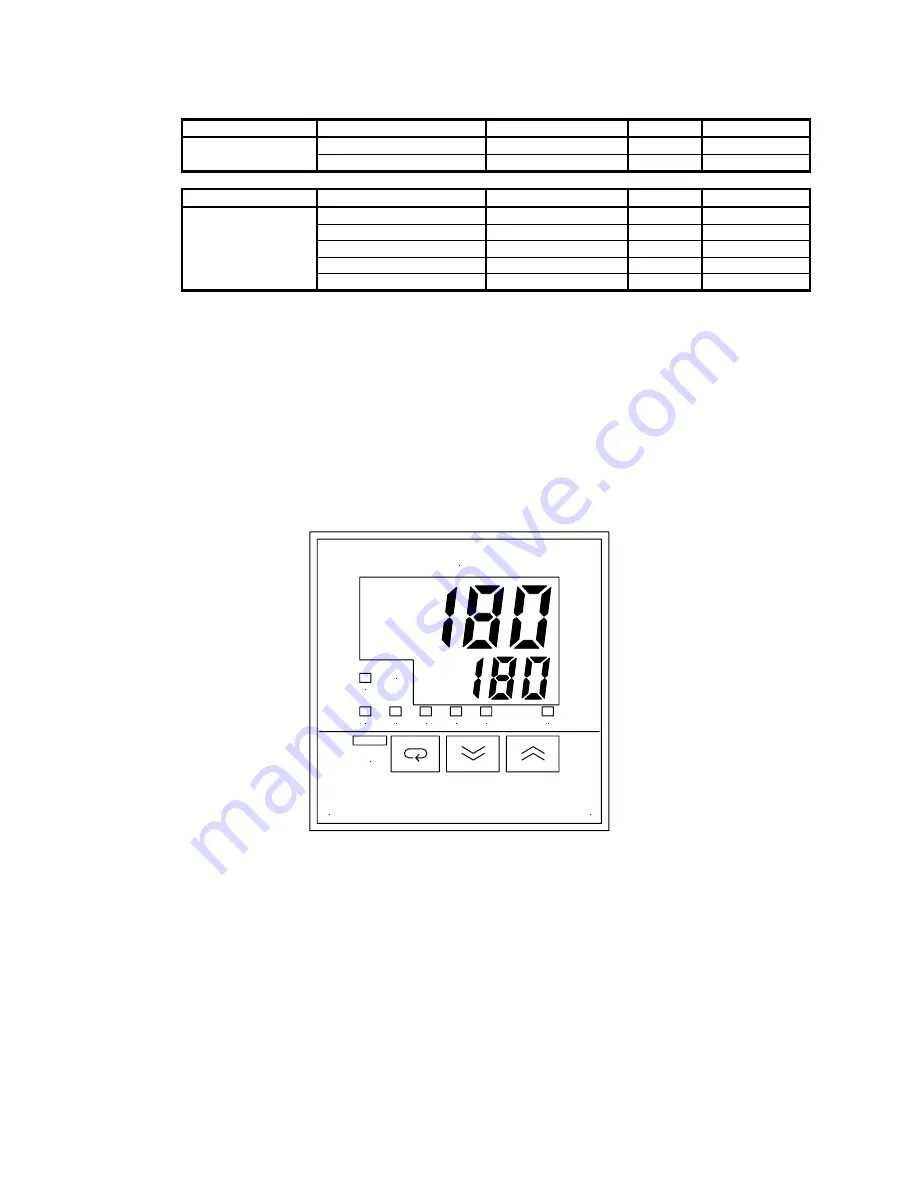
15, 30, & 60 cfm Compact Dryers
25
Figure 7: Settings for Process Temperature Controller (E5CN), Part No. A0567917
Mode
Parameter
Setting range
Default
Manuf. setting
Run/Stop Run/Stop Run
-
Operation
Alarm value 1
-1999 to 9999
0
25
Mode
Parameter
Setting range
Default
Manuf. setting
AT execute/cancel
ON, OFF
OFF
Various
Temperature input shift
-199.9 to 999.9
0.0
-
Proportional Band
0.1 to 999.9
8.0
Various
Integral Time
0 to 3999
233
Various
Adjustment
Derivative Time
0 to 3999
40
Various
Process Air Dew Point Display
Optional
The Process Air Dew Point meter indicates the current process air delivery moisture content.
Standard dryers use a microprocessor-based controller for displaying dew point air
temperature. The controller is a modular, self-contained unit removable from the mounting
housing. All parameters are factory set and adjusted; normally, no field adjustment to the
internal controls are necessary.
Figure 8: Typical Dew Point Display Monitor – Part No. A0555757
PV
SV
OUT1
OUT2 MANU STOP RMT
AT
SUB1
AT
E5CK
OMRON
Note:
No field adjustment is required. The dew point meter is meant for
moisture indication only!
Setting the High Dew Point Alarm
The high dew point alarm setting is changed by pressing the up and down keys to input the
alarm value. The factory setting for Alarm Value 1
(AL-1 )
is -10
°
F (-23
°
C).
Restoring the Process Air Dew Point Meter (E5CK) to Factory Setup
If the preset parameters on the controller have been tampered with and it no longer functions
properly, call the Service Department.
This controller is not meant to be modified.