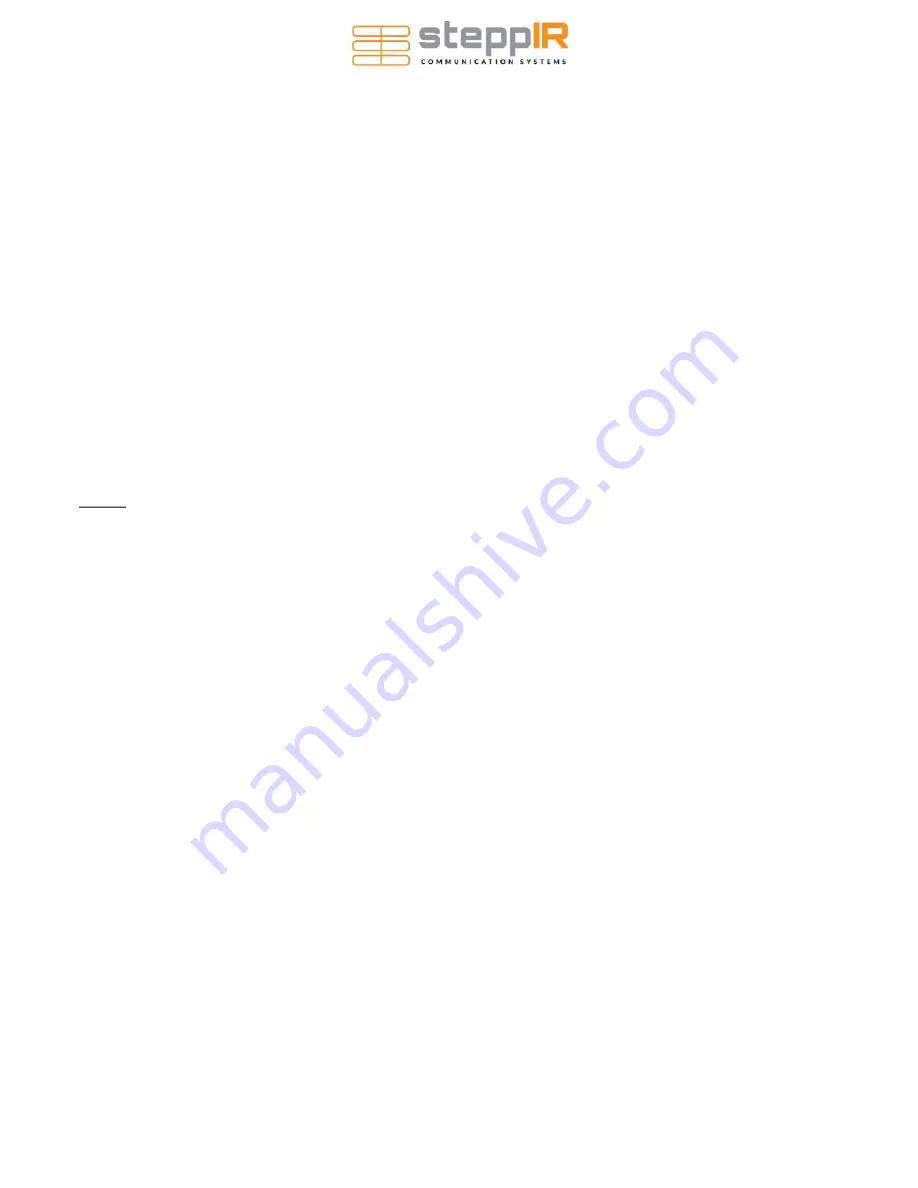
Tech Support:
www.steppir.com/support
⚫
Tel: 425.453.1910
⚫
Page 76
CHAPTER TWELVE
SECTION 12.0
TROUBLESHOOTING THE DB18E YAGI
TROUBLESHOOTING TIPS
SteppIR antennas are all powered by stepper motors, hence the name. Stepper motors function by rotating
the shaft a specific number of
“
steps
”
per revolution. The SDA 100 is simply counting the steps, of which
for each step sequence there is a known length that the antenna is adjusting. If for some reason the an-
tenna gets out of calibration, the method for recalibrating is pretty simple. When you press the calibrate
button, the controller retracts each element until it assumes it is
“
home
”,
and then keeps retracting the
stepper motors for a period of time to ensure that there is no question that the elements have indeed been
homed. At that point, the controller sends the elements back out to the exact frequency they were at when
the calibration function started. That is why in calibration mode you will hear the antennas make a loud
growling sound towards the end of the retracting—the elements are homed but the stepper motors keep
right on going for a while longer before sending the elements back out.
It is important to note that if a problem arises with the elements, such as an obstruction that is impeding
the path of the copper strip, the SDA 100 controller will not recognize this, so just because the controller is
showing the proper length for any given band, there may still be an issue. Even though the controller may
indicate that the copper strip is moving, in a troubleshooting situation it very well may not be. The control-
ler does not have much say in the indicating of a problem—it
’
s job is to simply get the elements to the right
length. This is why we have come up with the following information for you to review when having issues:
The antenna is out of calibration
—this is something that happens from time to time and is not a prob-
lem at all. Whenever you suspect a problem the very first thing that should be done is a calibrate. It is
always a good idea to calibrate the antenna if you are having trouble. It is best to set the DB18E to 20M
before doing the calibrate function. You only need to calibrate once. To be certain that the antenna was
indeed out of calibration, check the SWR before you calibrate and check it again after you calibrate to see if
there are any improvements. If the SWR is unchanged, the antenna was in calibration and is not the issue.
The lengths of the antenna are incorrect
—
Using the
“
Cause/Effect
”
theory, generally the first place to
look for trouble is the last place you have been. Using this line of thinking, if there is a problem with your
antenna, we need to be sure you are using the factory default lengths for your controller. Regardless of
whether you think you have done anything that could change the lengths, as a second step in troubleshoot-
ing (the first being the simple calibration of the antenna), be sure to reset the factory default lengths.
The SDA 100 electronic controller has a defective or intermittent driver chip
—
It only takes a mo-
mentary short to damage a driver chip
. The problem with driver chips, is that a blown driver chip or a
damaged driver chip that has not failed outright can act a lot like a damaged EHU. What we don
’
t want
you to do, is jump to conclusion on an EHU issue, only to spend time and money taking your antenna down
and find out that it was a driver chip problem, or some other issue with the controller in the first place.
Taking the time to troubleshoot and repair a controller is
MUCH
easier than taking down an antenna to re-
pair an EHU.
With that in mind, the following are steps for checking the voltage between the pin pairs that feed the mo-
tor windings. This information is critical to our technical support staff and you can save a lot of time by hav-
ing this data available before contacting us. Instructions as follows:
With the DB
-
25 connector removed from the back of the controller, measure the voltage between the pin
pairs that feed the motor windings. For example, pins 1 & 2 and 3 & 4 when referring to the driven ele-
ment. The other elements pin pairs are listed in the troubleshooting guide These are the same pairs you use
to check the resistance of the motor windings
.
Be very careful not to short the pairs together or
touch any other pins in the process, or you can potentially damage the controller driver chips.
With the controller power plugged in, you should read approximately 3.5 VDC across each pin pair. At this
point, change bands using the controllers band change button. As an example, switching from 20m to 10m
generally gives a long enough run to get a good reading. You should be reading on your volt
-
ohm meter
approximately 20 to 25 VAC using a 24 volt power supply. To check the next pin pair, you can then change
bands back to 20m and so on through the wire pairs. If you have significantly different values at any point
in the test process, you can be reasonably certain that you have a damaged driver chip for that element.
(Instructions continued on next page)