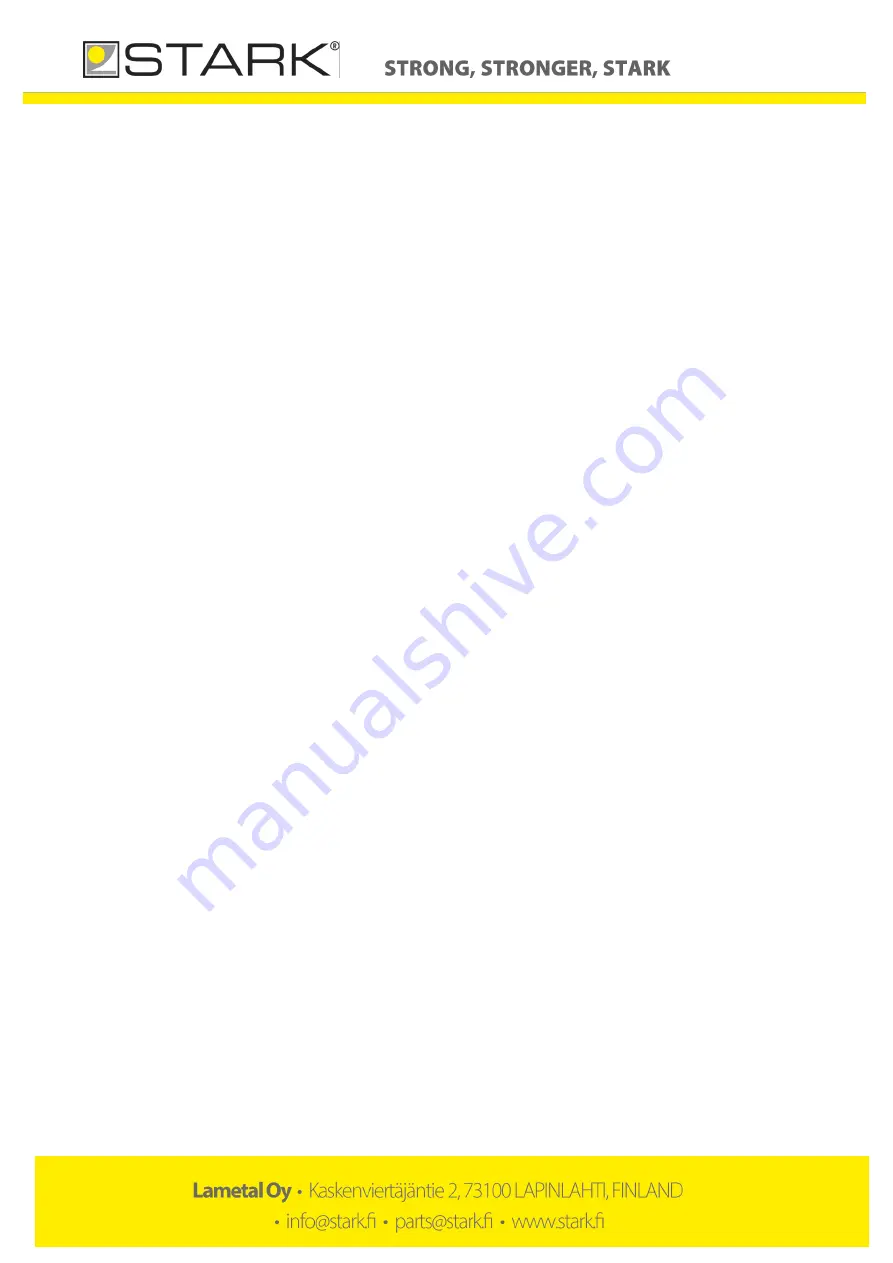
Sivu 30 / 30
10.
WARRANTY POLICY
1.
Warranty coverage
Lametal Oy, the manufacturer of STARK attachments, offers new devices a guarantee which covers material
and manufacturing defects in accordance with the terms in this warranty policy. Limitations to the warranty are
specified in point 7.
2.
Warranty starting date
The warranty starts on the agreed date of product delivery to the client, or on the date of approved instalment or
on the date the equipment has been taken into operation. The equipment is taken into operation when it has
been delivered to the client in accordance with the agreement and the client has acknowledged receipt of the
equipment. The client is to check the equipment before use as instructed in this manual and to notify the
manufacturer or the reseller of the equipment of any defects or flaws that are noticed during initial inspection.
This notification is to be done in writing within eight (8) days after delivery. Hidden defects and defects that are
otherwise difficult to detect must be reported immediately after detecting them, within one (1) year after receipt
of the equipment at the latest.
3.
Warranty period
STARK warranty covers a period of one (1) year. If need be, the client and the manufacturer make separate
agreements on warranty concerning repairs and spare parts used in repairs.
4.
Repairs during the warranty period
Repairs during the warranty period are carried out free of charge within the normal working hours by the
manufacturer repair and maintenance services or by a repair service provider accredited by the manufacturer. If
repairs are carried out by a repair service provider which has not been accredited by the manufacturer, the
manufacturer does not compensate for costs that are not covered by the warranty, such as travel and waiting
hours, daily allowances, travel expenses or costs arising from detaching and reinstalling the equipment. The
manufacturer does not compensate for indirect costs caused by repairs during the warranty period, such as lost
working hours. Original parts replaced during the warranty period shall remain with the manufacturer. The client
must keep the damaged parts for six (6) months unless otherwise agreed, and have them delivered to the
manufacturer without delay upon request.
5.
Conditions for repair under warranty
Manufacturer’s instructions for operat
ion, instalment and maintenance have been followed.
The equipment was damaged when operated in conditions for which it has been engineered.
In maintenance and repairs, only original, manufacturer parts have been used.
The form for the notification of defects provided by the manufacturer or the retailer has been filled in according
to the instructions and submitted for processing.
6.
Warranty after repair
Warranty holds until the end of the original warranty period. Repair under warranty does not prolong the
warranty period.
7.
Limitation to the warranty
The warranty does not cover:
o
consequential expenses resulting from the damaged equipment
o
indirect costs, such as loss of working hours
o
damages caused to a third party
o
equipment or components that have been modified or repaired by the client themselves
o
damages caused by normal wear and tear, inappropriate maintenance operations, neglect, accident,
connecting error, equipment overloading, user’s inexperience or use of othe
r than original parts
The warranty offered by the manufacturer does not exceed the purchase price of the equipment.
8.
Warranty claim procedure
For a warranty claim to be processed, the form for the notification of defects provided by the manufacturer or
the retailer must be filled in according to the instructions and submitted for processor. The warranty claim
procedure is carried out either in Finnish or English.