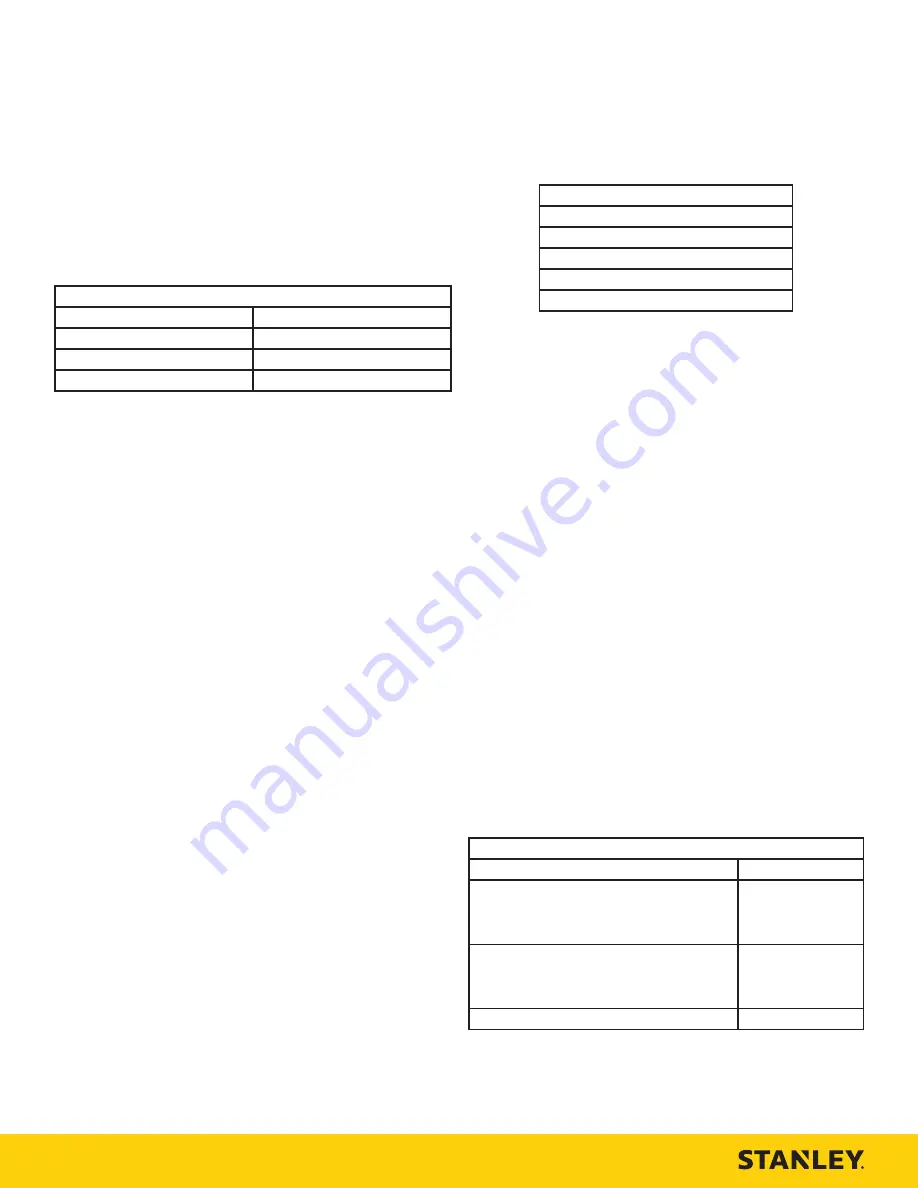
10 | IW24 User Manual
Connect to a Hydraulic Power Source
1. Using a calibrated flow and pressure gauge, check the output of the
hydraulic power source. Ensure it matches the flow and pressure in
“Specifications” on page 9. Hydraulic fluid must be 50°F or above.
Preheat if necessary.
2. Ensure that the hydraulic power source is equipped with a relief valve
set to open at the maximum relief pressure. See “Specifications” on
page 9.
3. Wipe hose couplers with a clean, lint free cloth.
4. Connect the return hose to the tool port marked “Out”.
5. Connect the pressure hose to the tool port marked “In”.
6. Ensure couplers are undamaged, properly connected and are tight.
7. Power up the hydraulic power source.
Using the Tool
Bolt Types for Use with IW24
Bolt Grade
Thread Sizes
SAE Grade 2
1 1/2 - 2 1/4 Inch
SAE Grade 5
1 1/8 - 1 3/4 Inch
SAE Grade 8
7/8 - 1 1/2 Inch
Note: Only use the sizes and types of accessories and consumables that are
recommended by STANLEY for threaded fasteners. Do not use other types or
sizes of accessories and consumables.
8. Hold the main tool handle with your dominant hand.
9. Hold the assist handle with your non-dominant hand.
10. Place the socket or accessory on the fastener being driven.
11. Squeeze the trigger.
Note: Hold the tool correctly and be ready to counteract normal or sudden
movements. Have both hands available. High reaction torque can develop if
the tool stalls, which can be caused by excessive loads being applied to the
tool.
12. Release the trigger to stop the tool.
Note: If you encounter a breakdown or the tool stops for any reason, release
the trigger and power down the hydraulic power source.
Tool Use Tips
•
To more accurately tighten bolts, lubricate threads and check bolts with
a torque wrench. Duplicate time of impacting for bolts of the same
length and thread.
•
Heavy, loose or multiple adapters can dissipate the intensity of impact.
Use as few adapters as possible and ensure they fit tightly. Loose fitting
accessories will increase vibration.
•
Hold the tool with a light, but safe grip. Risk from vibration is greater
with higher grip force.
•
Maximum torque can be obtained by continuously impacting for 10
seconds.
•
Hydraulic flow and pressure from the hydraulic power source will
dramatically influence the tool impact force and speed. Regularly check
the hydraulic power source. See “Specifications” on page 9.
Tool Maintenance
Daily Maintenance
1. Remove hydraulic power from the tool
2. Check all hydraulic connections and hoses for damage. Replace
damaged parts before operating the tool.
3. Remove the hammer case and inspect the impact mechanism. If
the mechanism is not well lubricated, or if the grease is burned, see
“Grease the Impact Mechanism” on page 10.
4. Inspect tool to ensure all decals are legible. Contact STANLEY if
replacements are needed.
5. Using a calibrated flow and pressure gauge, check the output of the
hydraulic power source. Ensure it matches the flow and pressure in
“Specifications” on page 9. Proper flow and pressure maintain
proper tool speed.
Underwater Tool Maintenance
Perform maintenance on underwater models after each use.
1. Remove hydraulic power from the tool.
2. Clean and grease the impact mechanism with a waterproof grease. See
“Grease the Impact Mechanism” on page 10.
3. Using a water displacing oil, spray into the trigger.
4. Spray or dip the entire tool.
Grease the Impact Mechanism
STANLEY Recommended Grease
Energy Release G-200
Kendall Super-Blu L-427
Texaco Starplex 2
Lubrication Engineers Almagard 3752
Mobil Delvac Xreme Service
1. Remove and clean the impact mechanism.
2. Inspect all parts for damage. Replace damaged parts before using the
tool.
3. Lubricate the inside of the hammer frame, the thrust bearing and thrust
races with a STANLEY recommended grease.
4. Reassemble the impact mechanism and reattach it to the tool.
5. Torque the four cap screws that hold the impact mechanism to the tool
to 30 Ft. Lbs. (41 Nm).
Tool Storage & Transport
Drain the tool of hydraulic fluid and plug open hydraulic ports. Collect all
hydraulic fluid for recycling (See “Tool Disposal” on page 10). Clean the
tool and store in a clean, dry space that is safe from damage. Ensure the tool
is secured and will not move during transport. An unsecured tool could cause
personal injury or damage to the tool.
Tool Disposal
Hydraulic Oil
Hydraulic oil can contaminate the air, ground and water if not properly
recycled. Recycle hydraulic oil in accordance with all State, Federal and local
laws, at your local oil recycling facility.
Hydraulic Hoses
Hang hydraulic hoses to drain. Collect the oil for recycling. Contact your local
municipal recycling authorities for an approved hydraulic hose recycling site.
Tool Body
Drain hydraulic oil from the tool, making sure to collect the oil for recycling.
Disassemble the tool and dispose of all non-metal parts. Recycle the metal
components. Contact your local municipal recycling authorities for recycling
instructions.
Accessories
IW24 Accessories
Description
Part Number
Hydrant Saver, Northern Kit
(Includes 8 Ft power tube, 1 1/2 Ft extension, Seat
Alignment Starter Wrench, Mueller 5 1/4 Inch
Socket and Pins)
31043
Hydrant Saver, Southern Kit
(Includes 6 1/2 Ft power tube, 1 1/2 Ft extension,
Seat Alignment Starter Wrench, Mueller 5 1/4
Inch Socket and Pins)
31044
Socket, 7 Inch
73435
Содержание IW2416001
Страница 3: ...IW24 User Manual 3 1 2 3 4 6 7 8 9 10 11 12 13 14 15 16 17 18 19 A 1 2 B C D 5...
Страница 4: ...4 IW24 User Manual 4 5 8 9 11 E 1 2 3 4 5 6 7 8 10 9 11 12 13 14 16 15 18 19 20 21 22 F 17...
Страница 12: ......
Страница 13: ......