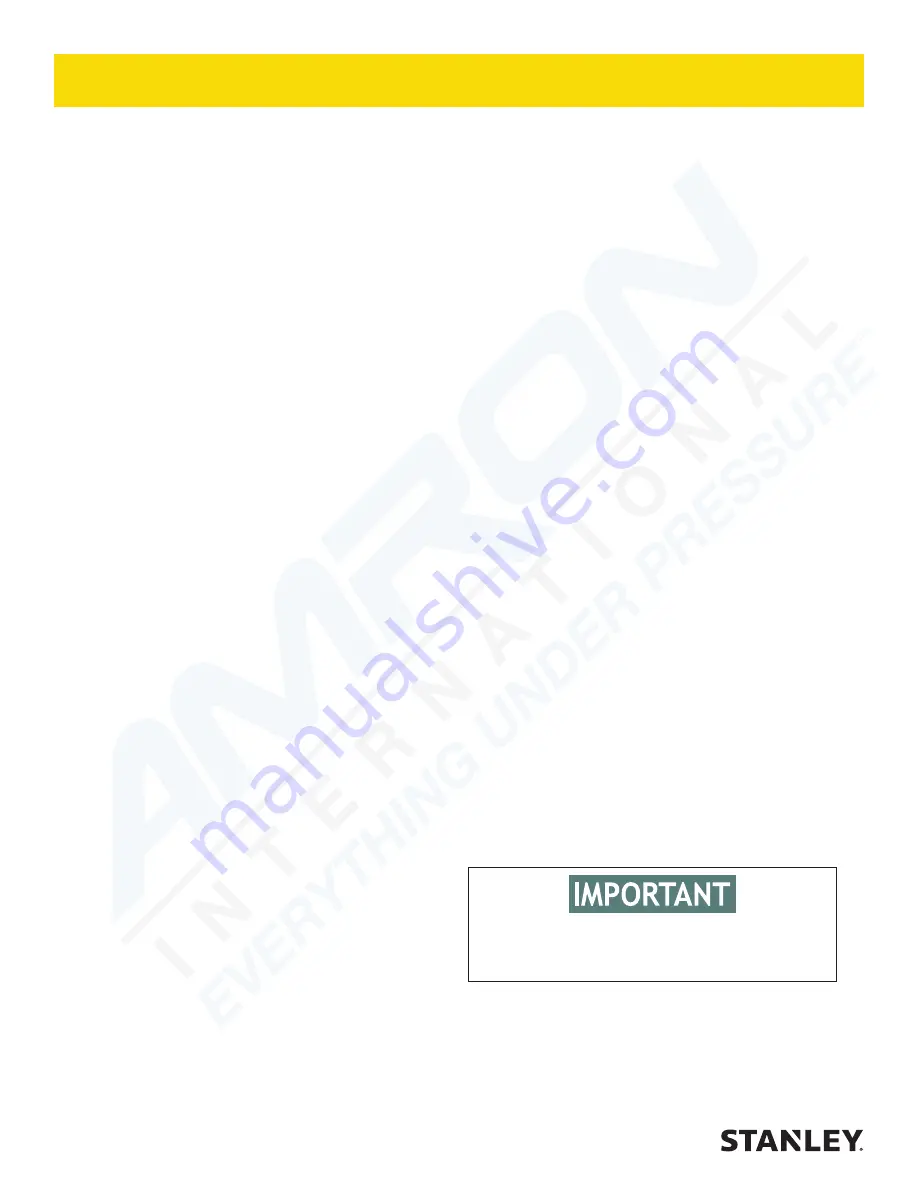
24 ► CS11
Service Manual
the front bearing retainer and blow air through the
small diameter motor shaft bearing. Use a shop air
nozzle to force the seal liner onto the motor shaft for
removal.
12.
To remove the seal from former two-piece motor
assemblies, use appropriate O-ring service tools to
pry it out of its bore. Take care to avoid damaging
the seal surfaces. Note seal orientation.
13. To remove the needle bearings on three-piece
motors, use Collet P/N 05871, and Ac tuator Pin P/N
05872, along with Slide Hammer P/N 11931. These
tools are available in Bearing Puller Kit P/N 05064.
To remove the bushings on two-piece motors, use
Collet P/N 11930 and Actuator Pin P/N 05067, along
with Slide Hammer P/N 11931.
MOTOR INSPECTION AND
CLEANING
Inspect and clean all parts as follows:
CLEANING
Clean all parts with a degreasing solvent. Blow dry with
compressed air and wipe clean. Use only lint free cloths.
SMALL DIAMETER BEARINGS/BUSHINGS
On three-piece motors equipped with needle bear ings,
check to make sure all rollers are in place and not nicked
or seized. If shaft wear is present, the bearing and shaft
must be replaced.
On two- or three-piece motors equipped with bushings,
the inside of the bushing should be gray with some
bronze showing through. If a significant amount of
yellow-bronze shows, bushing replace ment is required.
Inspect motor shaft for corre sponding wear and replace
as required.
GEAR CHAMBER
The chamber bores and end faces around the bearing
bores should be polished but not rough or grooved.
The flat surfaces around the chamber and bolt holes
should be flat and free of nicks or burrs that could cause
misalignment or leaks.
GEARS
Both gears should have straight tips without nicks;
square tooth ends and a smooth even polish on the
teeth and end faces. Check for cracks between the drive
gear keyway and gear tooth root. Discard the gear if
cracks are present.
MOTOR END HOUSINGS/RETAINERS
The gear face running surface should show two
interconnecting polished circles without a step and
should not be rough or grooved.
The shaft seal bore should be smooth and free from
nicks or scratches.
SHAFTS
The shaft diameter at the bearing and seal locations must
be smooth. Grooves, roughness or a reduced diameter
indicate fluid contamination or damaged needle bearings.
Grit particles may have been imbedded in the bushings
grinding into the hardened shaft. If abnormal shaft wear
as above occurs (in excess of normal polishing), both
the shaft and associated bearings/bushings must be
replaced.
REASSEMBLY
1.
On current two and three-piece motors, as semble
the seal liner assembly by installing the outside
diameter O-ring, quad ring and (seal liner washer
on three-piece motors only) as shown on the parts
location diagram. Place idler shaft through the seal
liner then loosely position the assembly in the seal
bore of the front bearing retainer (quad ring side
down). Place the seal liner washer over the shaft
then carefully push the seal liner into place. Install
the retaining ring. Remove the idler shaft.
2.
On former two-piece motors, carefully install the
shaft seal with the lips facing the gear side. Replace
the back-up washer and retaining ring.
3. To install the ball bearing(s) on the motor shaft,
support the ball bearing inner race and press the
motor shaft through the bearing inner race.
4.
To install the needle bearings in three-piece motors,
use Bearing Pusher P/N 11916.
To install the bushings on two-piece motors, use
Bearing Pusher P/N 11918.
5. Place the front bearing retainer/front bearing
housing assembly on a smooth clean arbor press
surface (protected from damage) with the large
bearing bore facing up. Position the piece so that a
clearance hole exists for the insertion of the motor
shaft.
The graphite seal liner must not be forced, pried
or pushed on directly because it can be easily
damaged.
6. Apply grease to the motor shaft and keyway, then
insert it through the shaft seal. Using Bearing Pusher
P/N 00850, or a sleeve/socket with a diameter
slightly smaller than the outside diameter of the
ball bearing, press the bearing assembly into place.
SERVICE