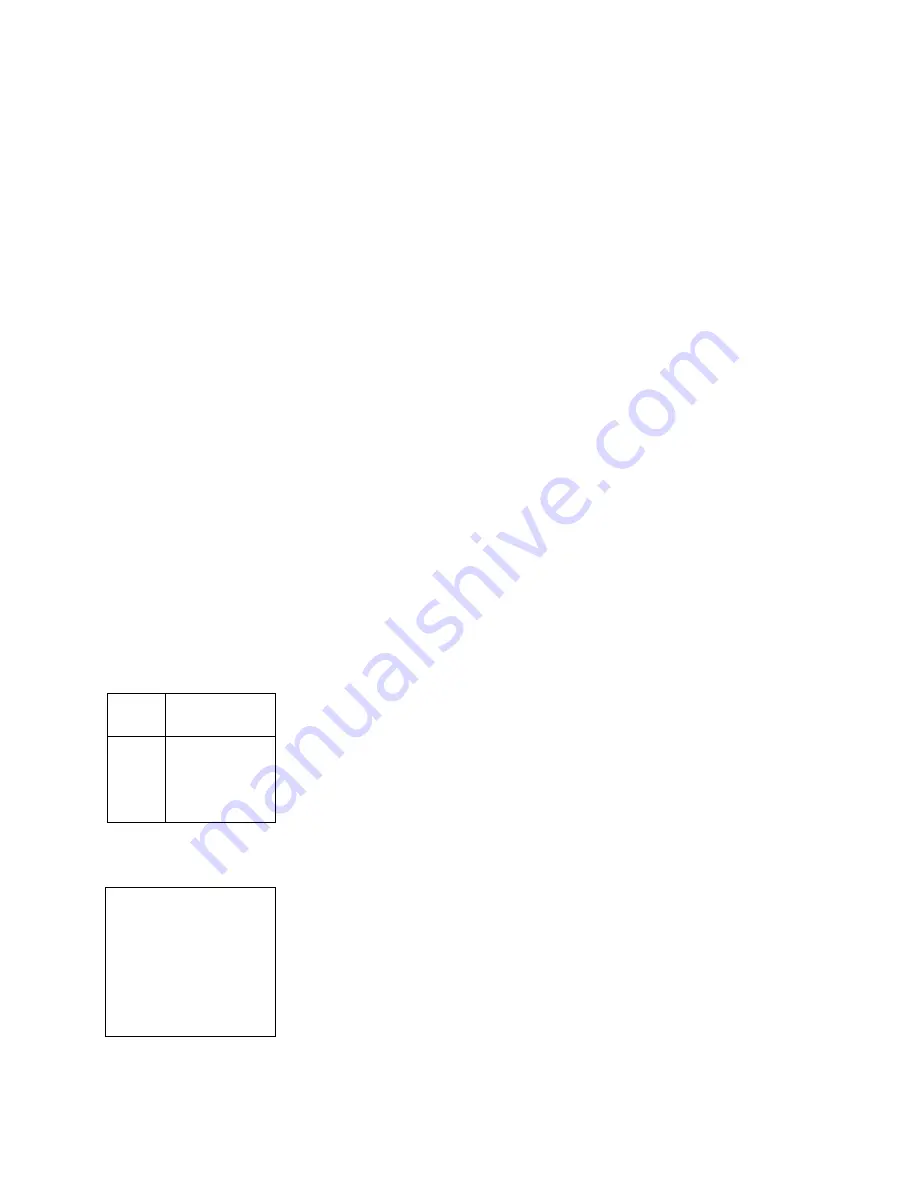
5
INSTALLATION
Installation of filter should only be done by qualified, licensed personnel.
Filter mount must:
• Provide weather and freezing protection.
• Provide space and lighting for easy access for routine maintenance. (See
Figure 1 and Table II, Page 6, for space requirements.)
• Be on a reasonably level surface and provide adequate drainage.
• Be as close to pool as possible to reduce line loss from pipe friction.
Piping:
• Piping must conform to local/state plumbing and sanitary codes.
• Use Teflon tape or Plasto-Joint Stik' on all male connections of plastic pipe
and fittings.
DO NOT use pipe compounds on plastic pipe; it will cause the
pipe to crack. Do not use sealant on unions—assemble them dry and hand
tight.
• Support pipe independently to prevent strains on filter or valve.
• Use 2” (51mm) pipe to reduce pressure losses as much as possible.
NOTICE:
Filter may be located away from pool, but for adequate flow larger
pipe may be needed. Check local codes for remote installation.
• Fittings restrict flow; for best efficiency use fewest possible fittings.
• Keep piping tight and free of leaks: pump suction line leaks may cause
trapped air in filter tank or loss of prime at pump; pump discharge line leaks
may show up as dampness or jets of water.
•
NOTICE:
Overtightening can crack filter ports.
Valves:
• A check valve installed ahead of filter inlet will prevent contaminants from
draining back into pool.
• A check valve installed between filter and heater will prevent hot water
from backing up into filter and deforming internal components.
• Install Sta-Rite Two Position Slide Valve or Multiport Selector Valve with fil-
ter. See Table I.
• Filter ports and valve ports are furnished with union connections.
DO NOT use pipe sealants on union collar (nut).
• Use care before assembly not to damage union sealing surfaces or O Ring.
• To allow recirculation during precoat (if precoat pot is used), install a recir-
culation line with shut-off between pad return line and pump suction.
Electrical
• All wiring, grounding and bonding of associated equipment must meet local
and/or National Electrical Code standards.
1
Lake Chemical Co., Chicago, IL
Port
Part
Size
Number
Multi-port
2"
18201-0200*
Plastic Slide
2"
WC212-134P*
TABLE I - Sta-Rite valves for
use with DE filters
NOTICE:
Use of valves
other than those listed
above could cause
reversed water flow
through filters and
damage to internal fil-
ter components.
* Recommended for best energy
conservation.