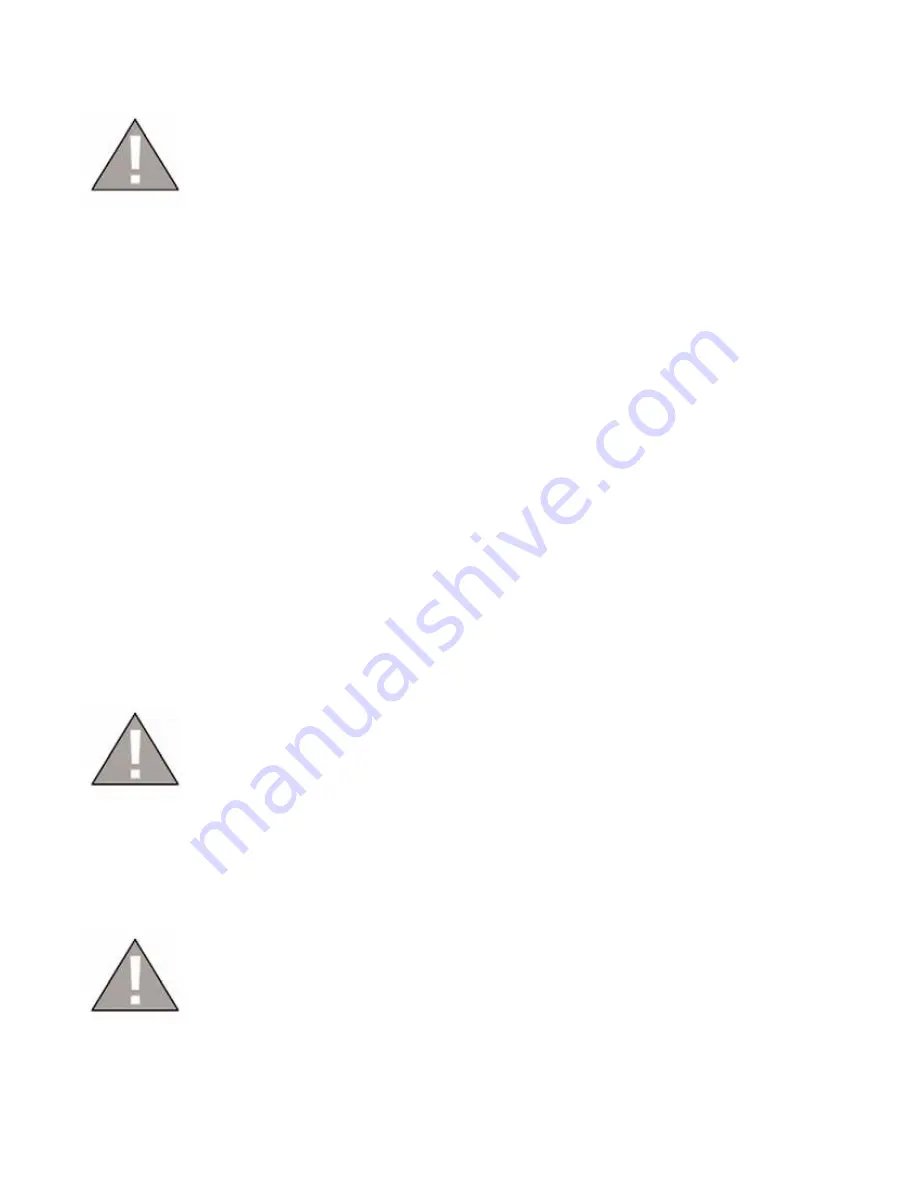
e)
Torque spindle nut to 12 ft/lbs. While turning rotor, loosen nut one flat and insert cotter
pin.
IF SLOT AND PIN HOLES DO NOT LINE UP, TURN NUT BACK ENOUGH TO
INSERT COTTER PIN. MAKE SUE THAT ROTOR SPINS FREELY!
f)
Install grease cap, do not tap on the center, it will crush easily
5)
Preparation and Installation of calipers
a)
Prior to installing calipers, connect flex lines to calipers with hollow bolt and (2) copper
washers, one on top and one on the bottom. Don’t tighten bolt until after caliper is
mounted.
b)
Install new sleeves and bushings, provided, into all four ears of each caliper using
silicone grease or non-petroleum type grease for ease of installation.
c)
Install inboard brake pad with supplied support spring. Inboard pads must lay flat
against piston.
d)
Install outboard brake pad in the caliper with the ears of the pad over the ears of the
caliper and the bottom of the pads engaged in the recess of the caliper.
e)
Lubricate supplied caliper mounting bolts with silicone grease or other non-petroleum
lubricant.
f)
Position the caliper assembly over the rotor and line up the holes in the caliper ears with
the holes in the mounting bracket. (Bleeder screws must point up)
g)
Install mounting bolts, making sure that the ends of the bolts pass under the retaining
ears on the inboard pad. Push bolts through to engage the bushings of the outboard
caliper ears while at the same time threading the bolts into the mounting bracket.
Torque bolts to 25-30 ft/lbs.
h)
Clinch outboard pad to caliper casting so that the pad remains flush against the casting
without clearance or movement. (This will minimize brake squeak).
IF THE PAD DRAGS ON THE HUB OF THE ROTOR, YOU MAY NEED TO CLOSE
THE TABS ON THE PADS THAT GO OVER THE OUTBOARD SIDE OF THE
CALIPER
i)
Temporarily connect free end of flex lines to the 12 point retainer brackets on the frame
and temporarily secure with "horseshoe clip”. Turn steering assembly through a full left to
right turn, while noting flex lines, to assure that they do not twist or take a double bend.
If incorrect, remove them from the 12 point bracket and re-orient the hose with minimum
distortion. Complete permanent connection using a tube wrench.
FAILURE TO COMPLETE THIS PART OF THE INSTALLATION MAY CAUSE
BRAKE LOCK-UP IN SERVICE. THE THIN WALL INTERIOR HOSE OF THE FLEX
LINE CAN COLLAPSE DURING TURNS AND RESTRICT THE FLUID FROM
RELIEVING THE CALIPER BRAKE LINE PRESSURE WHEN THE BRAKE PEDAL
IS RELEASED. MAKE SURE ROTOR SPINS FREELY AND THERE ARE NO
INTERFERENCES.
6)
Power booster (A123-1, A123-4)
A123, A123-1, -1C, A123-3, A123-4, A123-5, A123-58, A123-59
Revision 7
2