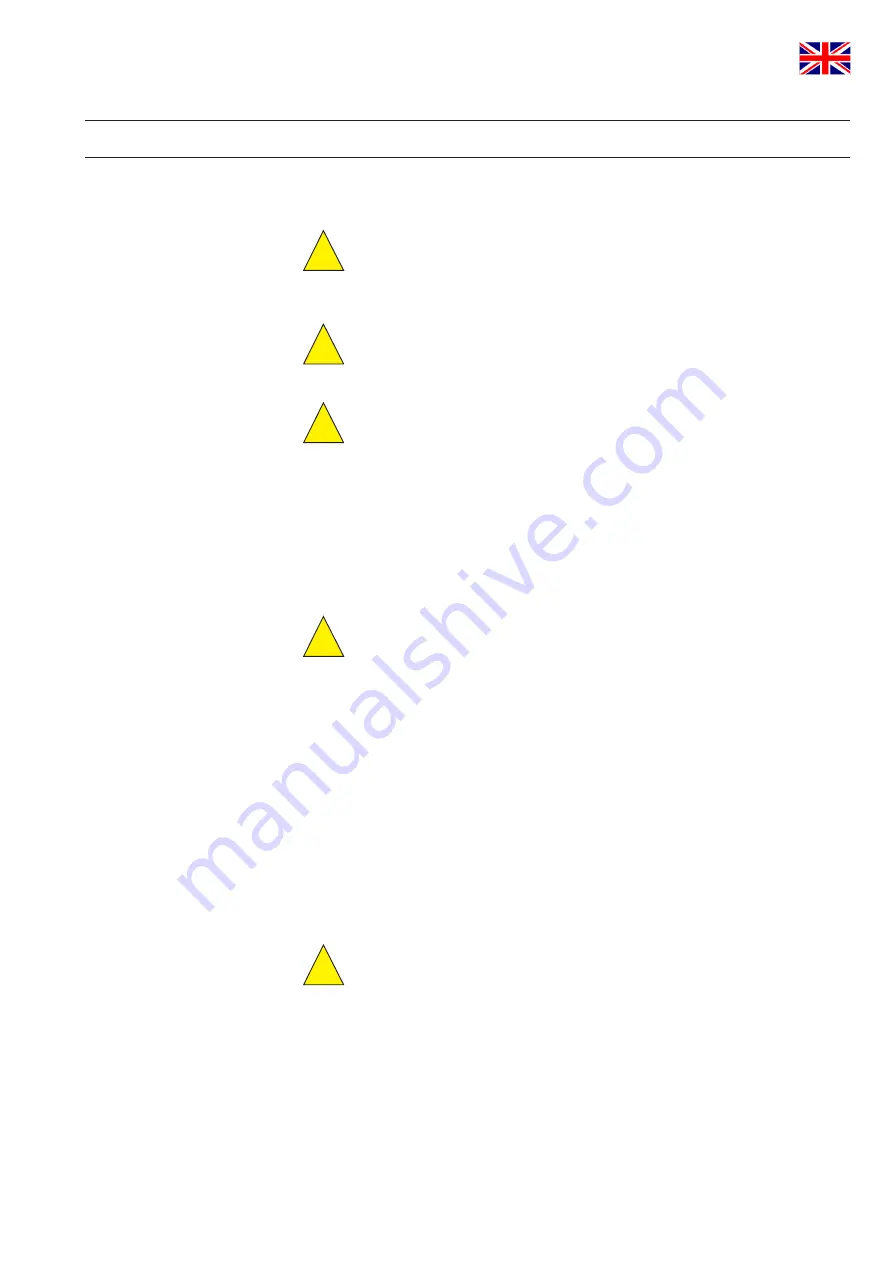
13
APV_DA4_UK-1_102018.indd
UK
Double Seat Mix Proof Valve
APV DELTA DA4
Instruction Manual: UK - rev. 1
APV
7. Installation and Commissioning
- The valve must be installed in vertical position to ensure that
fluids can drain off freely from the valve housing and the leakage
chamber.
Caution!
Leakages and fluid losses from seat lifting and CIP
spraying must be safely collected and drained!
- The valve housing can be welded directly into the pipeline
(completely removable valve insert).
Note!
Observe welding instructions.
- Observe heights of installation and dismantling!
Caution!
Before first startup:
- Actuate the valve by applying compressed air. The opening, closing
and seat lifting processes must run smoothly.
- Check the function of the control unit or valve position indication.
- Check for possible leakages during commissioning. Replace
defective seals.
7.1.
Welding Instructions
- Before welding the valve, remove the valve insert from the housing.
Caution!
Handle and store the valve insert carefully to avoid
damaging the part.
- It is not necessary to remove the lower shaft seal as it can be
destroyed during removal.
-
Welding should only be carried out by certified welders (DIN EN ISO
9606-1) (seam quality DIN EN ISO 5817).
- The welding of the valve housings must be undertaken in such a
way that the valve body is not deformed.
- The preparation of the weld seam up to 3 mm thickness must be
carried out as a square butt joint without air. Consider shrinkage!
- TIG orbital welding is recommended.
Caution!
After welding the valve housing or mating flanges, and
after performing any work on the piping, do not operate the valves
until the corresponding areas of the installation and piping have
been cleaned and welding residue has been removed. If the piping
is not cleaned before operation, welding residue and dirt particles
can settle in the valves and cause damage to the valves and seals.
- If these welding instructions are not followed, any resulting damage
will not be covered by the warranty.
- Welding directives for aseptic applications shall be drawn from the
AWS/ANSI Directives and EHEDG Guidelines.
!
!
!
!
!