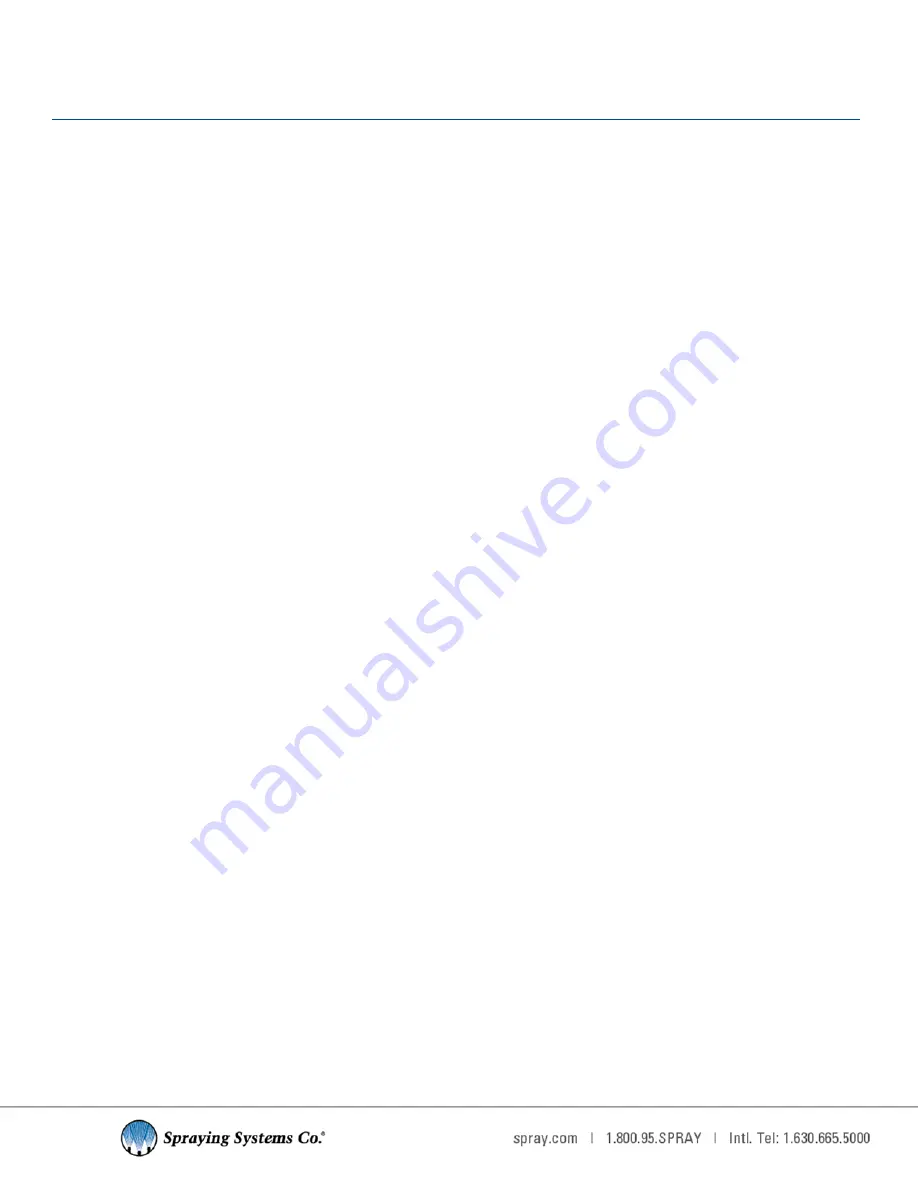
5
5
3.1 ELECTROSTATICS SPRAYING OVERVIEW
In electrostatic spraying, a negative charge is introduced into a fluid in the nozzle body through a central charging elec-
trode, which causes the fluid to acquire a negative charge. When this negative charge is applied to the fluid, this causes
the fluid molecules to repel each other, following the principle that molecules with opposite charges will attract and
molecules with like charges will repel. Electrostatic spraying relies on the repulsion of these like
-
charged small fluid
droplets.
After leaving the nozzle orifice, the fluid molecules continue to repel each other as they travel, causing the already
small droplets to break up into even smaller droplets. This process will continue until the repulsive force between the
molecules is no longer strong enough to break the surface tension and split the droplet again.
These tiny and uniformly sized droplets retain their negative charges and will be attracted to any neutral, grounded
target nearby with an attractive force stronger than gravity. Electrostatic forces pull the liquid molecules towards this
target, thinly and evenly coating the target surface and providing a very high fluid transfer efficiency
Some benefits of electrostatic spraying include:
•
Low flow rates that allow for less fluid usage
•
Reduced product and workspace contamination due to overspray
•
Shorter workspace cleanup times
•
Longer intervals between system maintenance
•
More uniform target coatings, typically achieving over 90% transfer efficiency
3.2 SYSTEM COMPONENTS AND INSTALLATION REQUIREMENTS
This electrostatic system includes the following main components:
•
AutoJet
®
ES250 Electrostatic Spray Control Panel
•
Fluid Reservoir Assembly
•
Electrostatic Chain Oiler Spray Nozzle
CUSTOMER REQUIREMENTS FOR INSTALLATION
•
Mounting locations for all components that meet any and all national or local safety standards
•
40 psi (minimum) shop air connection
•
24 VDC power supply to provide power to the control panel
’
s circuit board, the solenoid valve connection, and the
high voltage power supply (HVPS) —
2.5
amp minimum
REQUIRED TOOLS FOR INSTALLATION
•
15 mm open ended wrench and 27 mm open ended wrench.
•
Slotted screwdriver
3/8” (9.5
mm) or larger for accessing the panel)
•
#2 Phillips head screwdriver (for removing the high voltage terminal block enclosure cover)
•
#2 Square bit screwdriver or
3/8” (9.5
mm) slotted screwdriver (for tightening high voltage terminals)
•
1/8” (0.125
mm) slotted screwdriver (for terminals)
•
Wire strippers
SECTION 3
ES250 OVERVIEW