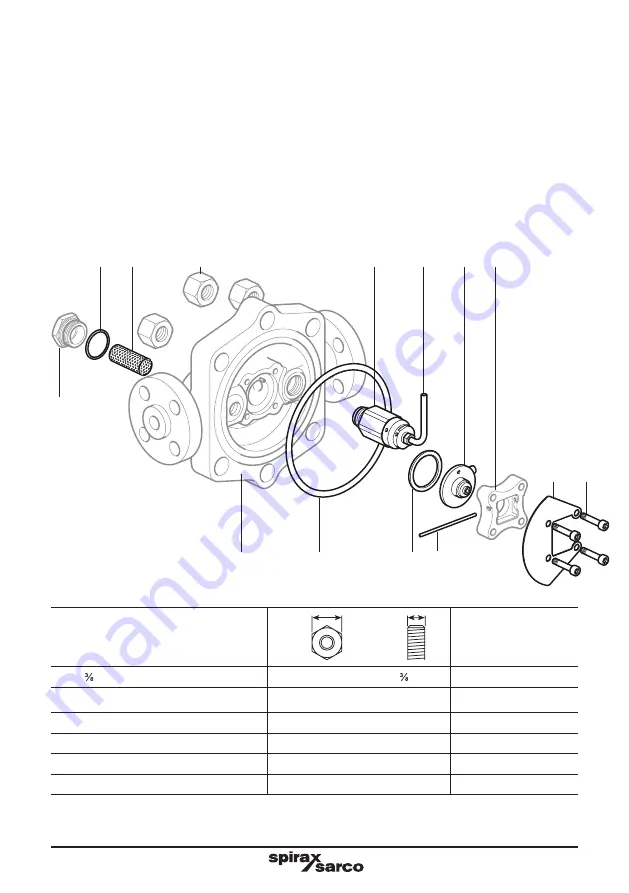
IM-P179-15
CMGT Issue 3
22
start of text under grey section header box
start of text continuing from previous page
TRANSLATION RUN OVER
6.2.3 Replacing the Air vent assembly
-
Gain access to the internals by removal of the cover (
2
) by undoing the six ¾" UNF (
4
) nuts holding the
cover in place.
-
Then remove the air vent assembly (
9
) and the air vent tube (
10
).
-
Put a little anti-seize on the thread of the new air vent assembly (
9
) together with the tube (
10
)
preassembled, tighten following the guidance of the torque setting in the table.
Note 1:
The air vent tube must be aligned and pointing in the same direction as the directional arrow upon
the seat clamp (
11
).
Note 2:
when the internals have been assembled, with the pin (
13
) fully inserted so that it touches the air
vent assembly it may appear long, do not cut it, it is purposely long to inhibit that with vibration its movement
is limited, therefore, it is impossible for it to become free.
Parts drawn in a grey line are
not supplied as spares.
Recommended tightening torques
Item Part
Inch
or
mm
N m
lbf ft
3
" NPT Square head plug
11 mm A/F
" NPT
As required
4
¾" UNF Hex. Nut
1.125" A/F
¾" UNF
252-260
186-192
6
Strainer cap
32 mm A/F
M28 x 1.5
170-190
125-140
9
Air vent assembly
32 mm A/F
M22 x 1.5
80-88
59-65
10
Air vent tube assembly
11 mm A/F
M10 x 1.5
10-12
7-9
12
M6 x 30 Socket head cap screw
5 mm A/F (Hex Key)
M6
14-16
10-12
8
6
1
7
9
10
17
11
22
12
18
19 13
4
Содержание FTC62
Страница 26: ...IM P179 15 CMGT Issue 3 26...