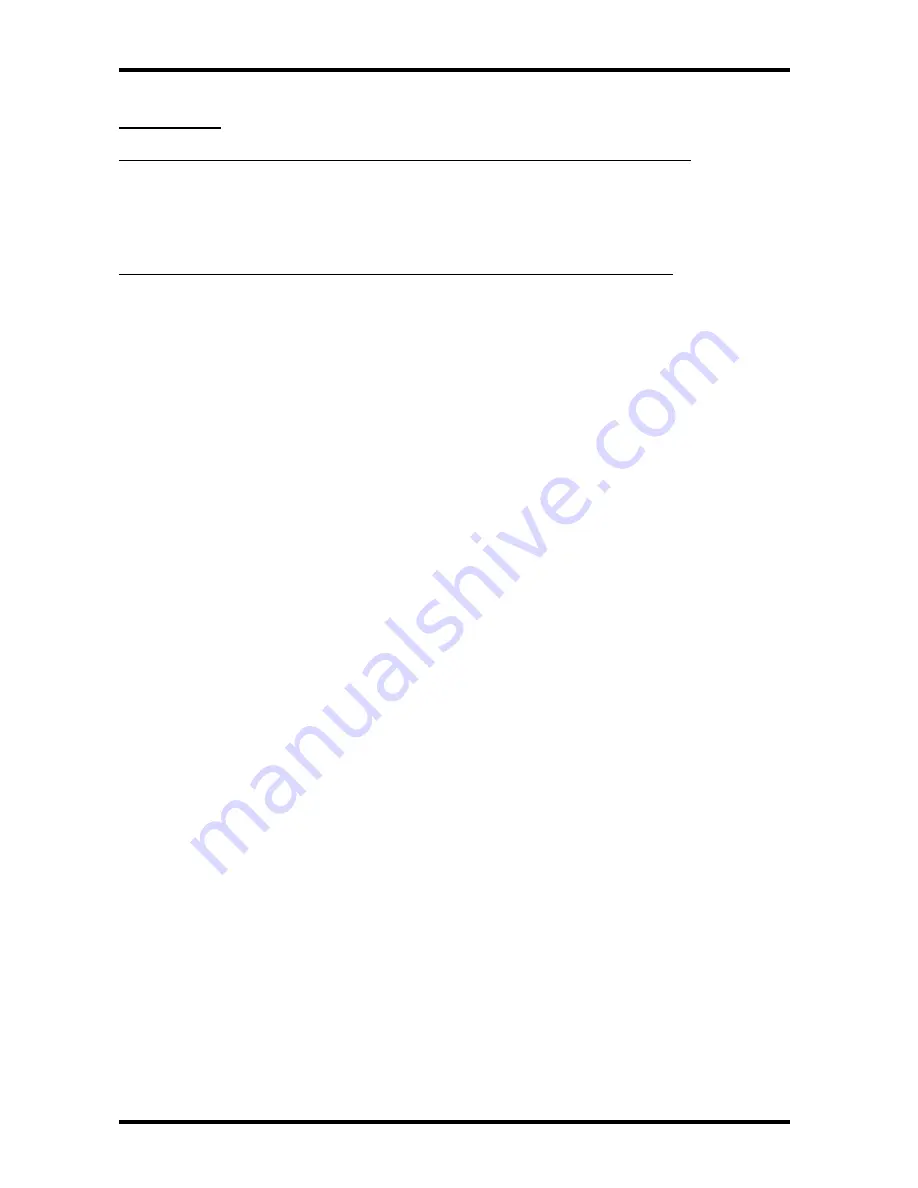
Instruction book for compressor type HV2/200
Page 10
3.5 Stopping
To stop the compressor manually for short periods, the following procedure should be used:
A
Flip the compressor’s manual unloader to the vertical position to unload the LP suction valve.
B
Open the drain valves.
C
Stop the compressor.
When stopping the compressor before prolonged downtime, use the following procedure:
A
Drain old oil, clean the crankcase sump and fill with new oil.
B
Apply a suitable corrosion inhibiting oil to the compressor valves, non-return valves, cylinder walls and
open surfaces of the crankshaft.
C
If there is a danger of frost, drain the cooling water.
D
Set the manual unloader in the horizontal position so that there is no load on the compressor’s suction
valve.
E
Turn over the compressor by hand once a week.
F
The starter panel and other electrical equipment must be similarly protected against corrosion damage.