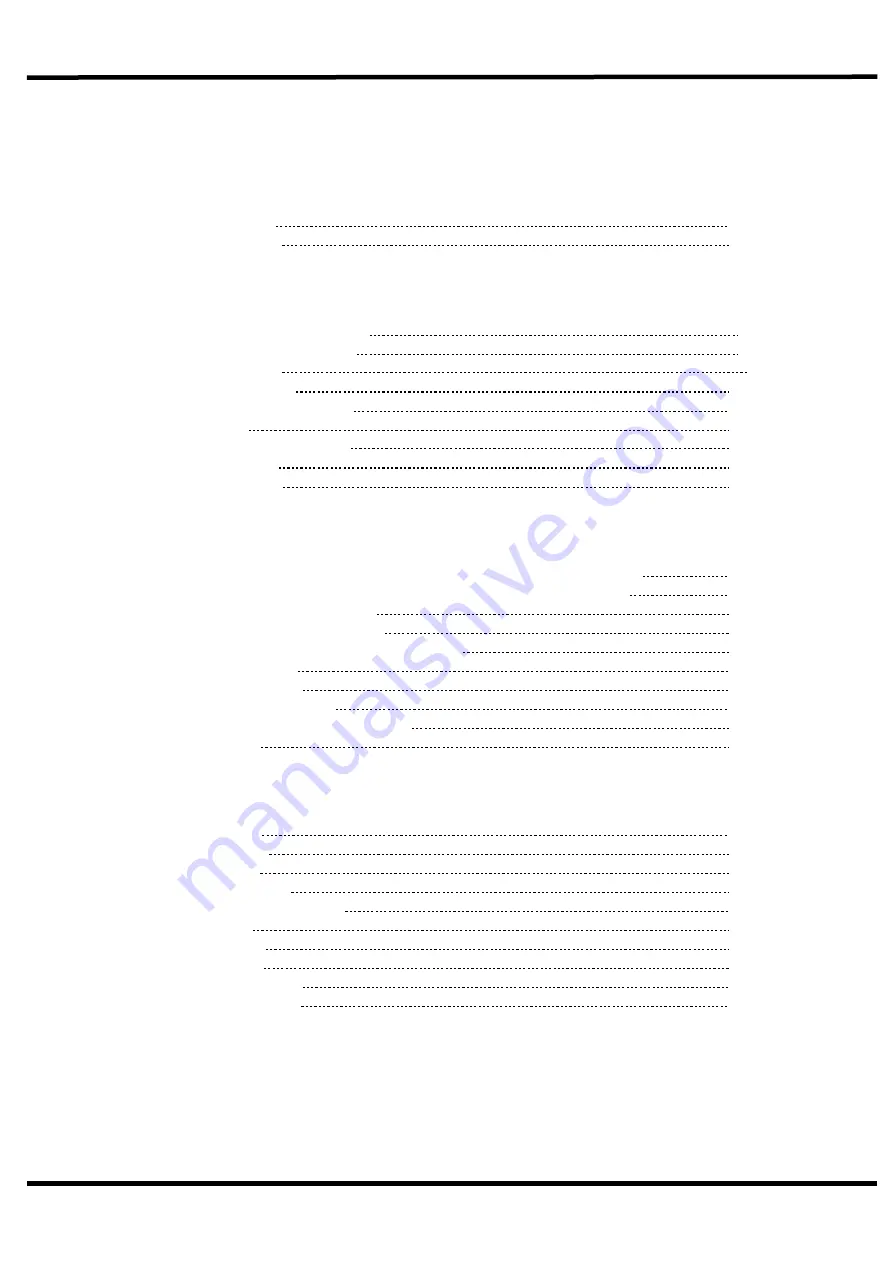
TWIGA CLASSIC
3
Contents
General Information
Introduction
5
Specification
6
Safety
Safety Recommendation
7
Overhead Power Lines
9
Safety Decal
11
Warning Signs
11
Road Work Guidelines
11
Training
12
Tractor Requirements
12
Lighting Kits
12
Lifting Points
12
Installing your Machine
Attaching your Machine to the Tractor
– Using 3 Point Linkage
13
Attaching your Machine to the Tractor - Using Axle Mounting
17
Running up your Machine
19
Removing from the Tractor
20
Hydraulic Proportional Controls - 2SV
21
Cable Controls
22
PILOT Controls
23
Operation Warnings
24
Moving into Transport Position
25
Operation
27
Options
Oil Cooler
29
Head Float
30
Arm Float
31
Debris Blower
32
Hydraulic Rear Roller
33
Autopilot
34
Quad Saw
39
Cutter Bar
42
Telescopic Arm
43
Forward Reach
44