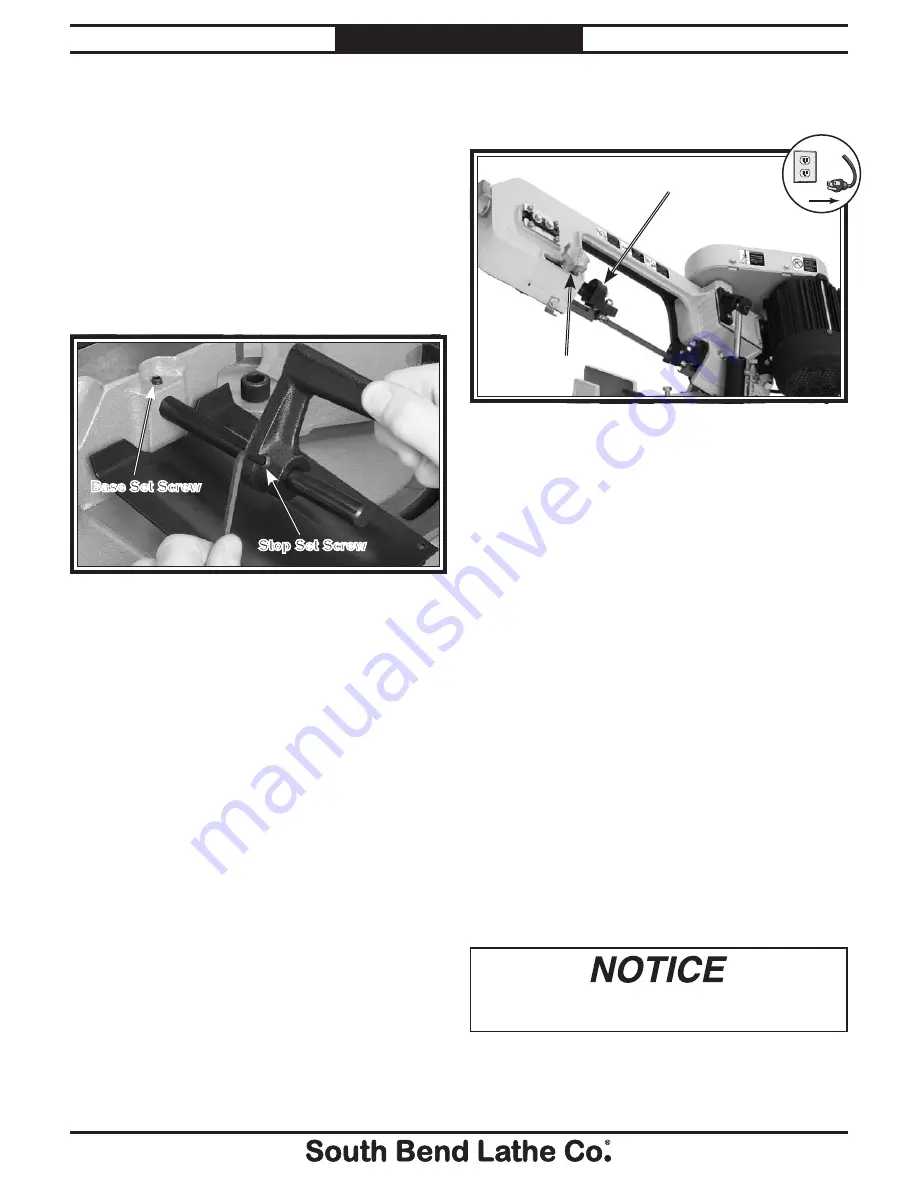
For Machines Mfg. Since 8/09
Model SB1018
-31-
O P E R A T I O N
Operation Tips
Review the following tips to help you safely and
effectively operate your bandsaw and get the
maximum life out of your saw blades.
• Use the work stop to quickly and accurately
cut multiple pieces of stock to the same
length.
• Allow the blade to reach full speed before
engaging the workpiece. Never start a cut
with the blade in contact with the workpiece.
• Pay attention to the chips produced by the
cutting operation and use their appearance
to fine-tune the blade speed, feed speed,
and pressure (refer to the
Chip Inspection
Chart
on
Page 28
).
• Wait until the blade has completely stopped
before removing the workpiece from the vise,
and avoid touching the cut end—it could be
very hot!
Release blade tension at the end of each use
to prolong blade life.
Blade Guide
2.
Loosen the knob shown in
Figure 42
and
slide the blade guide to within
1
⁄
2
" of the
workpiece, then re-tighten the knob.
Figure 42. Blade guides.
Blade Guide
Knob
!
Work Stop
4.
Slide the work stop onto the work stop rod
and tighten the stop set screw.
Figure 41. Installing stop rod.
Base Set Screw
Stop Set Screw
The work stop allows you to repeat cuts at the
same length.
To adjust the blade guide:
1.
DISCONNECT BANDSAW FROM POWER!
2.
Insert the work stop rod approximately
3
⁄
4
"
into the vise base.
3.
Tighten the base set screw (
Figure 41
).
The upper blade guide should be positioned to
within approximately
1
⁄
4
" of the workpiece for
all cutting operations. The support provided by
keeping the blade guides close ensures straight
cuts by keeping the blade from twisting and
drifting off the cut line.
To adjust the blade guide:
1.
DISCONNECT BANDSAW FROM POWER!